Hot stuff – record melting point for ceramics
Scientists in Russia claim to have created the most heat-resistant ceramic material.
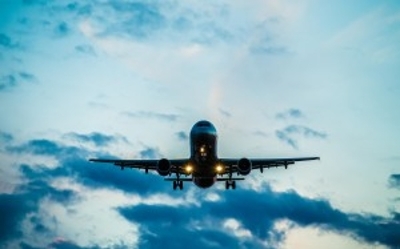
A ceramic material with the highest melting point among currently known compounds at above 4,000°C has been proven, according to researchers at the National University of Science and Technology (NUST MISIS), Russia. Due to the combination of physical, mechanical and thermal properties, the material shows promise for use in heat-loaded components of aircraft, such as nose fairings, jet engines and sharp front edges of wings operating at temperatures above 2,000°C.
The triple hafnium-carbon-nitrogen system, hafnium carbonitride (Hf-C-N), was chosen because previously scientists from Brown University, USA, predicted that it would have a high thermal conductivity and resistance to oxidation, as well as the highest melting point among all known compounds.
Dmitry Moskovskikh, Head of NUST MISIS Center for Constructional Ceramic Materials, says that the material is created by ‘self-propagating high-temperature synthesis (SHS) of non-stoichiometric HfCxNy powder and the fabrication of bulk ultra-high temperature ceramics by spark plasma sintering’. Testing shows the melting point of the material has surpassed the previous record holder, hafnium carbide (HfC).
Moskovskikh explains, ‘The SHS of the Hf + 0.5C powder mixture in a nitrogen atmosphere made it possible for the first time to produce non-stoichiometric HfC. According to the results of X-ray phase analysis, the synthesis powder consists of a HfC phase with a crystal structure (NaCl) of Fm 3m (225) and a lattice parameter of 0.4606nm.’
Efforts are being made to make spacecrafts and aircraft faster, more affordable and durable, which involves enhancing the most heat-loaded parts to protect them. Research is ‘aimed either at modifying various carbon-carbon and carbon-ceramic composite materials with various additives or coatings, or at creating multilayer coatings with sufficiently low oxidation rates. However, these approaches are not without drawbacks’, Moskovskikh says.
The first is due to uncontrolled acceleration of the oxidation process, the second is because of insufficiently high melting points of the compounds used, and the third reason is because, at temperatures above 2,000°C, the structural material’s strength will be too low.
He adds, ‘To increase the lifting force and maneuverability, as well as to reduce aerodynamic drag, it is necessary to reduce the radius of rounding of the wing of the rocket system to a few centimetres. But then, when leaving the atmosphere and re-entering, temperatures of the order of 2,000°C will be observed on the surface of the wings, and a record 4,000°C at the very edge.
‘The most promising materials for ultra-high-temperature applications are carbides and nitrides of transition metals of groups IV and V. For example, HfC is considered as a promising material for use in the aerospace industry as a protector of the most heat-loaded units of a hypersonic aircraft, [such as] jet engines, turbine blades, combustion chambers, nose fairings, sharp edges of the wings.
‘This compound [HfC] possesses not only one of the highest melting points, Tmelt ≈3,927°C, but also high hardness of 25.5GPa and elastic modulus of 4,61GPa. Also, carbides and nitrides of transition metals of groups IV and V form triple compounds – carbonitrides – which, as a rule, have higher melting points compared to binary compounds, higher mechanical and chemical properties.’
To test the material, the team has compared HfC with the synthesised HfCN. They placed densified samples on a graphite plate shaped like a dumbbell with a similar graphite plate on top to avoid heat loss, before hooking it up to a battery to start the heating process. ‘The melting temperature of the samples was determined by comparing their microstructure before and after heating,’ Moskovskikh states.
‘It was shown that the samples located at a point with a minimum temperature T3 completely retained their shape. At a higher temperature T2, the behavior of the samples was different. HfC partially melted and changed its shape, while the HfCN remained unchanged. At a point with a maximum temperature T1, HfC completely melted and spread over a graphite plate, while HfCN only decreased in size due to sintering.’
The next steps are to accurately measure the melting point and other properties such as oxidation and ablation resistance.