Holograms boost 3D printing efficiency and resolution
A new method allows the fabrication of millimetre-scale objects within seconds using significantly less energy than previous approaches.
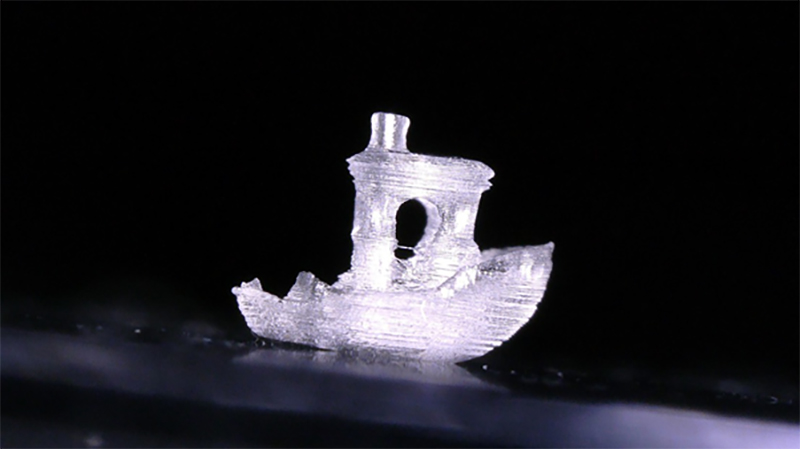
Scientists at EPFL and the University of Southern Denmark have used holographic projections to bring unprecedented resolution to a light-based 3D printing technique.
While traditional 3D printers work by depositing layers of material, tomographic volumetric additive manufacturing (TVAM) involves shining laser light at a rotating vial of resin until it hardens where accumulated energy exceeds a certain threshold.
An advantage of TVAM is that it can produce objects in seconds, compared to around 10 minutes for layer-based 3D printing. But a disadvantage is that it is very inefficient, because only around 1% of the encoded light reaches the resin to produce the desired shape.
Researchers from EPFL’s Laboratory of Applied Photonic Devices, led by Christophe Moser, and from the University of Southern Denmark Centre for Photonics Engineering, led by Jesper Glückstad, have reported a TVAM method in Nature Communications that significantly reduces the amount of energy required, while simultaneously boosting resolution.
The technique involves projecting a 3D hologram of a shape onto the spinning vial of resin. Unlike traditional TVAM, which encodes information in the amplitude of projected light waves, the holographic method takes advantage of their phase.
‘All pixel inputs are contributing to the holographic image in all planes, which gives us more light efficiency as well as better spatial resolution in the final 3D object, as the projected patterns can be controlled in the projection depth,’ Moser summarises.
Better options
The holograms are generated using a technique called HoloTile, which was invented by Glückstad.
HoloTile involves superimposing multiple holograms of a desired projection pattern, and eliminates random light interference called speckle noise that would otherwise create grainy images.
Although holographic volumetric additive manufacturing has been reported previously, the joint EPFL-SDU team’s approach is the first to yield such high-fidelity 3D-printed objects, largely thanks to the use of HoloTile.
EPFL student and lead author Maria Isabel Alvarez-Castaño explains that another unique aspect of the approach is that the hologram beams can be made ‘self-healing’, meaning they can spread through a resin without being thrown off course by small particles. This property is essential for 3D printing with bio-resins and hydrogels that are loaded with cells, making the method ideally suited for biomedical applications.
‘We are interested in using our approach to build 3D complex shapes of biological structures, allowing us to bio-print, for example, life-scale models of tissues or organs,”says Alvarez-Castaño.
Next, the team aims to improve the efficiency of their method another two-fold.
Moser says that with some computational enhancements, the ultimate goal is to use holographic volumetric additive manufacturing to fabricate objects by simply projecting a hologram onto a resin, without needing to rotate it. This could further simplify volumetric additive manufacturing and increase the potential for high-volume, energy-efficient fabrication processes.
He adds that the fact that the holograms can be coded using standard commercial equipment adds to the practicality of the approach.
This content is distributed under a Creative Commons CC BY-SA 4.0 license.