HERO coatings to boost turbine engine efficiency
A single-layer approach to protective coatings for turbine engines could increase efficiency while also simplifying the manufacturing process.
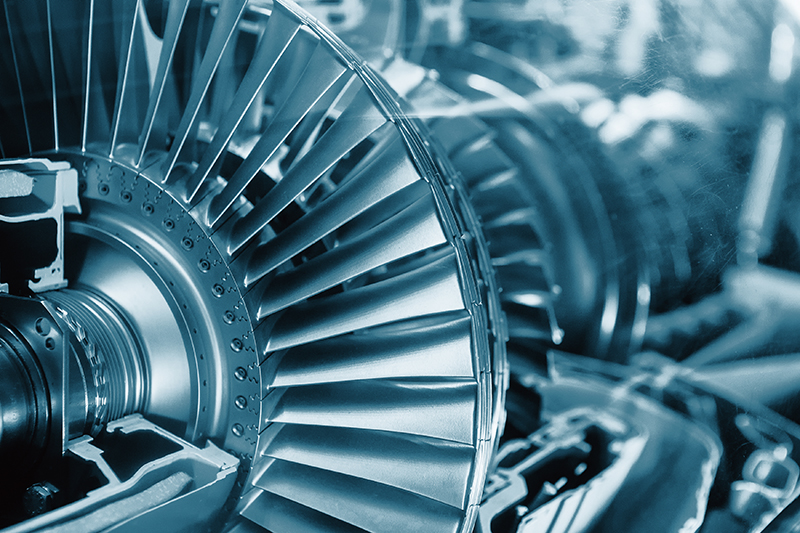
Turbine engines produce more work output per heat input at higher temperatures, but those same higher temperatures can damage the blades.
Currently, two types of coatings are used to protect them, neither of which can tolerate temperatures of 1,900°C, explains the team at the University of Virginia (UVA), USA.
One option is coated nickel-based superalloys that can tolerate up to around 1,200°C. Another option is multi-layered ceramic composites, which are limited by the melting temperature of silicon at around 1,400°C.
The increased energy efficiency that is possible at 1,900°C is a priority for the ARPA-E ULTIMATE programme of the US Department of Energy (DoE), which supports this research.
Now, a research team, led by Professor Elizabeth Opila at the UVA, claims to have developed freestanding materials that can tolerate higher temperatures.
The team has returned to refractory metal alloys as the substrate, which were mostly abandoned since the 1960s because of poor oxidation resistance. These coatings would reportedly enable refractory metal alloys to be used in turbine engines at higher temperatures.
Opila explains how 'mixed rare-earth oxides enable low-thermal conductivity coatings that are compatible with refractory (high-temperature) alloys, and they are incredibly stable in high-temperature combustion environments'.
She adds, 'We called these coatings ‘HERO’ coatings, for their high-entropy rare-earth-oxide composition, and also because they could ‘save’ refractory alloys from rapid degradation in the high-temperature oxidising conditions.'
From the start, the team aimed to produce 'a single-layer coating that could meet all performance requirements and would therefore be more economical to produce', Opila shares.
Additional barrier layers may be needed in some cases, she acknowledges, but suggests that 'starting simple challenges current environmental and thermal barrier coating designs that are complex multilayer solutions for protection of turbine blade materials'.
The key to these coatings is tailoring the properties to best protect the underlying substrate by combining multiple rare-earth oxides, such as yttrium, erbium and ytterbium.
The mixed powders are densified at high temperatures using conventional spark plasma sintering. The optimal mixtures were identified through first-principle calculations, as well as machine learning and validated expected properties, by working with UVA Associate Professors Bi-Cheng Zhou and Prasanna Balachandran.
The paper published in Scripta Materialia describes how, 'The criteria for multi-component rare-earth-oxide composition selection has three main components. First, multiple rare-earth cations of varying size and mass in rare-earth oxides are desired to increase phonon scattering and reduce the coating thermal conductivity.
'Second, a cubic phase is desired to reduce stresses due to anisotropic thermal expansion upon cooling. Third, we choose yttrium oxide as the cubic-phase base material due to its lower cost and mass relative to the other rare-earth oxides.
'Additional rare-earth-oxide components are selected to optimise coating properties,' reads the paper on Opportunities for novel refractory alloy thermal/environmental barrier coatings using multicomponent rare earth oxides.
A collaboration with UVA Professor Patrick Hopkins’ ExSiTE Lab, was, Opila reports, 'essential for [determining] the three-fold reduction in thermal conductivity [to 2.3W(mK)] we obtained by mixing rare-earth oxides'. Low-thermal conductivity coatings reduce the underlying alloy surface temperature.
These coatings were then applied to alloys as test coupons using two standard manufacturing methods. One technique heats the material to a molten state before spraying on the surface. The other is applied as a liquid mixture that dries and hardens.
These coupons were tested for thermal conductivity, thermal expansion and thermal stability in the high-temperature, high-velocity steam expected in combustion product gases.
A thermal expansion match between the alloy substrate and the coating is key to coating adherence. Stability was also verified against molten deposits that might be found in turbine engines.
Processing of the coatings has already been demonstrated by working with the Commonwealth Center for Advanced Manufacturing. Next steps are to continue development and validation of these coatings, funded by the US DoE’s ARPA-E programme.