Heating up the future of heavy industry
An electrically conductive firebrick that stores heat from renewable sources could power industrial processes.
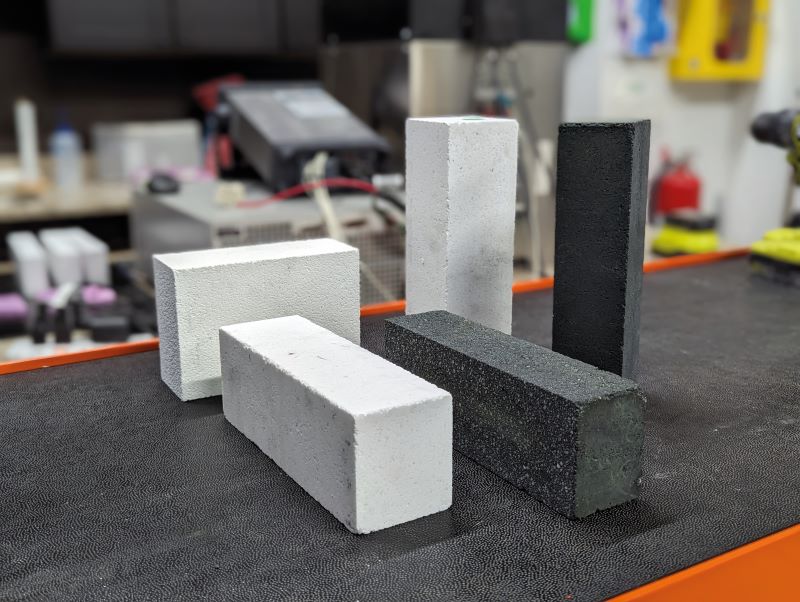
The ‘E-Bricks’ are developed by Electrified Thermal Solutions, a spin-out from the Massachusetts Institute of Technology (MIT), USA.
They are designed to resolve one of the most challenging aspects of global decarbonisation – industrial heat – which consumes 19% of global primary energy. Currently, 85% of this is derived from fossil fuels.
Firebricks are cheap and commonplace clay bricks used in fireplaces and ovens, but they have been a focus for researcher Daniel Stack since 2014 due to their ability to reach fl ame-like temperatures and potential to store heat from renewable sources.
Previously, the innovation was limited as a solution for industrial use because of the need for electric resistance heaters to warm the bricks.
As a PhD student at MIT, Stack worked with Principal Research Scientist Charles Forsberg to produce electrically conductive ceramic firebricks, replacing the resistance heaters so the bricks produce the heat directly. They call these ‘E-Bricks’.
Since then, Electrified Thermal Solutions has worked to commercialise the technology, developing the Joule Hive Thermal Battery (JHTB).
The JHTB converts renewable electricity into thermal energy up to a temperature of 1,800°C – a critical threshold for the most demanding industrial processes. Typical competing thermal batteries are limited to 1,000°C or below, say the researchers.
Stack, co-founder and CEO of Electrified Thermal Solutions, explains the challenges. 'Traditional electric heating systems all encounter challenges with oxidation that make it difficult for them to match the performance and reliability of fossil-fuel heating systems that industry is accustomed to.
'These traditional electric heating materials, namely metallic alloy elements (Fe-Cr-Al and Ni-Cr), SiC, MoSi₂, carbon and tungsten, all oxidise and burn out when exposed to air or other oxygen-containing gases – which constitutes the atmospheres of most industrial processes.
'The oxidation reaction is exponential with temperature, such that the hotter these heaters run, the faster they burn out and must be replaced. In the case of carbon or tungsten-based heaters, oxygen readily reacts with these materials without any mitigation, such that a closed or controlled atmosphere is required to operate them as electric heaters, and costly temperature-limited heat exchangers are required to interface with industrial furnaces.'
The problems caused by oxidation reactions are central to the development of the chemically-modified chrome-alumina-based ‘E-Bricks’, which are 100% oxide and so do not oxidise, allowing them to run hotter and operate in standard atmospheric conditions.
They are said to be 98% similar in composition to traditional firebricks while exhibiting semiconducting electrical properties and the team believes they could operate for decades.
The Joule Hive technology was operated at the scale of an elevator-sized pilot for cyclic heating and hot gas generation, achieving a Technology Readiness Level of 6 on the US Department of Energy (DoE) assessment scale, which confirmed its readiness for scale-up to industrial applications.
The first JHTB product will have a standard ~5MW of power output, while storing 25MWh of thermal energy.
Stack highlights that, 'Industrial heating operations frequently require tens to hundreds of megawatt heat, which are power levels that are typically transmitted and distributed at tens to hundreds of kilovolts on power lines. The E-Bricks are engineered to take this voltage directly. This is critical to the practicality of the solution for large heat loads since it removes the need for expensive power equipment at the customer site.'
Commercial scalability has been built into the research from the start, with the E-Bricks based on existing manufacturing capabilities and supply chains.
The modular architecture reportedly allows for flexible deployment, from cement kilns to chemical processing facilities, and the firebrick arrays are stored in insulated, off-the-shelf, metal boxes.
Cycling and power perturbation tests of the brick stacks are ongoing in preparation for megawatt-scale commercial demonstration in 2025, with further funding from the US DoE.