Getting a feel for the real world of STEM
Philipa Kugonza, Mechanical Engineering Student at Coventry University, UK, undertook a Year in Industry at Rolls-Royce joining forces with Staff Technologist Andrew Russell FIMMM to hone the manufacturing of compressor blades.
The teacher perspective
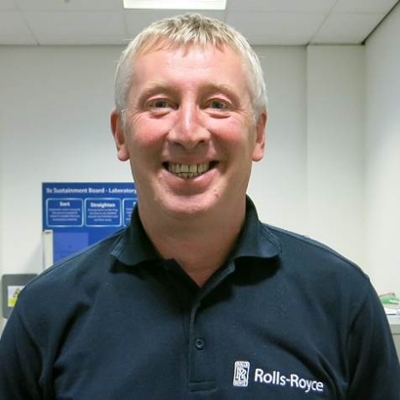
[We] involve students in technology, science, engineering, business and finance across the UK by providing challenging and engaging projects.
How does the Year in Industry work?
The Year in Industry programme is administered by the Engineering Development Trust, whose aim is to involve students in technology, science, engineering, business and finance across the UK by providing challenging and engaging projects. Successful applicants are paired with selected employers for a 12-month period and given ownership of a pre-determined specific project or contribute to a much wider business objective.
What is the goal with these placements?
These placements provide the student with a flavour of what it’s really like to be involved in their chosen vocation. The student gains valuable real-world experience which will aid them both in the final years of their degrees and upon graduation. From an employer’s perspective, a Year in Industry student brings fresh, innovative ideas and ways of thinking which provides a valuable contribution to the business. It also helps to create a talent pipeline of students who may wish to return on completion of their chosen degree.
Why is it important to mix traditional education with industry experience?
By mixing traditional education with a placement in industry, the student obtains a much broader perspective and appreciation of their preferred career choice. Being able to talk to and learn from industry-based professionals is an invaluable development opportunity for a student.
How can students pursue a placement?
Students interested in pursuing a Year in Industry placement should contact the Engineering Development Trust in the first instance.
What was your involvement in Philipa’s placement?
My role regarding Philipa’s placement was to provide an interesting, high-quality project which is representative of the work we perform in a manufacturing environment. Establishing a project charter and agreeing specific, measurable, attainable, relevant and time-bound objectives were key to the success of the placement project.
The student perspective
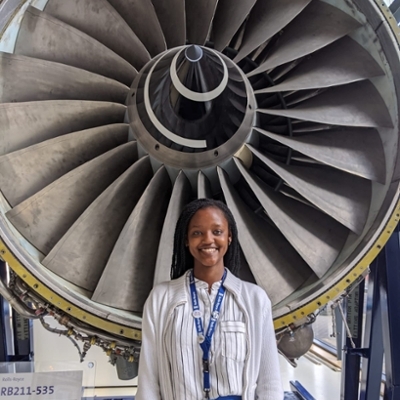
I worked with so many brilliant people that shared their career stories with me giving different perspectives on what a career in engineering is.
Why did you want to do a Year in Industry?
My course is quite broad – Mechanical Engineering – and I wasn’t sure what field of engineering I wanted to specialise in after I graduated. I did a Year in Industry to explore these options and gain practical experience to help me figure out what area of engineering I wanted to focus on.
What did you do in your placement?
I was involved in several mentally stimulating projects that challenged me to expand my technical knowledge and work with a diverse team that always supported my learning experience. As a process modelling engineering intern, my main project required me to use finite element analysis (FEA) software to better understand the forging process and microstructural evolution of compressor blades to increase yield. I was responsible for managing the modelling project to completion. Additionally, I was involved in a project aimed at meeting the company’s sustainability targets. This involved the development of a portable filtration system referred to as a Coolant Health Unit to recycle machining coolant and reduce impact on the environment.
What have you learnt from a year with Rolls-Royce?
When I started my Year in Industry, I had just completed my second year at university and was unsure of what the relevance of some of my modules were to the real world. The placement year with Rolls-Royce gave me an opportunity to apply the university knowledge in solving real-life problems. I was exposed to several parts of the company that gave me a chance to explore my interests. This helped me to select my final-year option modules at my university, such as FEA. This is because I really enjoyed it to develop a deeper understanding of Rolls-Royce manufacturing processes.
What would you say the benefits of industry-focused placements are?
I would highly recommend doing a Year in Industry or any form of work experience/internship because there is so much you learn on the job that you wouldn’t usually be taught in a lecture hall. Industry-focused placements open you up to a range of learning opportunities to develop your skillset and grow your professional network. During my placement, I worked with so many brilliant people that shared their career stories with me giving different perspectives on what a career in engineering is. It also gave me a better understanding of the different roads to chartership and how I could maximise my time left at university to solidify the foundation of my career.
Do you have any tips to anyone wanting to do something similar?
My advice would be – don’t be afraid to apply for a role that you feel slightly under-qualified for. You don’t need to have 100% of the skills required for every role because recruiters understand that you are at the early stages of your career. Just be keen to learn and reflect on all feedback you are given. Before I applied to Rolls-Royce, I had some unsuccessful applications elsewhere. I used the feedback I received to improve my CV and better sell myself.
I applied to Rolls-Royce through the Engineering Development Trust by submitting my CV and cover letter. I then had a phone interview and went on to do psychometric tests. The best way to pass psychometric tests is practice. I was later invited to an assessment centre at Rolls-Royce where I had 1:1 interviews with recruiters and group activities with other candidates. A few weeks later, I was contacted and offered the role.
Tell me about your plans for the future?
In the short term, I’ll be returning to Coventry University to finish the final year of my Mechanical Engineering course and explore options for a Master’s programme. In the long term, I can definitely see myself pursuing a career in manufacturing engineering. I’d preferably want to work in the aerospace sector, however, I don’t want to close my mind off to the other fields of engineering just yet. I’m hoping to get some more work experience in the near future and continue to work on my professional development and personal growth.
Refining the toolkit
This was a collaborative project between the Materials and Process Modelling Group and the Gas Turbine Compressor Blade Manufacturing Team. The objective was to optimise the manufacturing of a high-volume component by using a commercial forge modelling software package.
The images illustrate the sequential forging steps used in the early hot forming stages of manufacture. The billet is transferred to the split die extrusion tooling and the material volume is redistributed in the die.
Under the supervision of Dr Sam Gardner, Philipa substantiated the existing thermomechanical processing parameters and highlighted dimensional improvements to the extrusion die tooling. These were subsequently adopted and now form part of a robust manufacturing method.
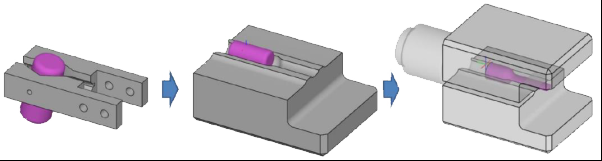