Femtosecond laser fabricates ultra-precise X-ray mirrors for telescopes
Femtosecond laser micromachining has been combined with stress-based figure correction to fabricate ultra-precise and high-performance X-ray mirrors to detect and explore high-energy cosmic events.
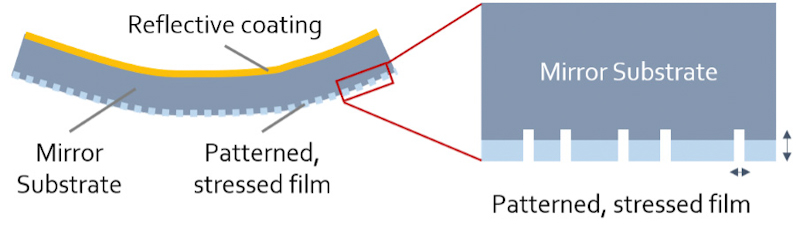
© Heng Zuo, MIT Kavli Institute for Astrophysics and Space Research
Orbiting telescopes have thousands of thin mirrors fitted to them and each one requires a precisely curved shape and careful alignment to obtain sharp images of astronomical X-rays. However, if an individual mirror is bent or deformed, this affects the telescope’s performance.
The technique, developed at Massachusetts Institute of Technology’s Space Nanotechnology Lab (SNL) and published in Optica, removes 'stressed film regions on the mirror substrate', and corrects errors in the shape of its reflective surface.
Heng Zuo, who led the research and is now Assistant Professor at the University of New Mexico, explains that ultra-thin mirrors are harder to make to the exact shape than thicker mirrors because their fabrication can severely bend them. Telescope mirrors also require highly reflective coatings and these typically have high stress, which deforms the mirrors further, she adds.
Femtosecond laser micromachining offers advantages over other fabrication techniques in rectifying these errors.
'Traditional laser processing methods typically use laser sources with pulse widths of nanoseconds or longer, which result in much larger thermal effects and can even leave micro-cracks in the target materials,' she explains.
'In comparison, femtosecond lasers are capable of controllably producing highly precise features, such as holes, channels and marks on various materials, with little collateral damage.'
Another benefit is high repetition rates, and this allows for much higher machining speeds and throughput, she continues. This means femtosecond lasers could deliver the large number of ultra-high-resolution mirrors that missions like NASA’s Lynx X-ray Surveyor will require.
SNL’s research combines the technique with stress-based figure correction – a process that applies a deformable film to the mirror substrate to adjust its stress states and induce controlled bending. To determine this, the team measures its shape and creates a stress correction map.
'The mirror surface shape, or wavefront, is measured with an interferometer before and after the micromachining so the difference in the two sequential measurements represents the change from the micromachining process,' Zuo explains. 'From the surface wavefront, we can also calculate the stress state in the mirror substrate using the well-known Stoney’s equation.'
This step allows them to determine the relationship between micromachining and changes in the mirror surface curvatures and stress states.
The team has used ultra-fast lasers to write two types of patterns consisting of holes and troughs onto the mirror substrate. 'We showed that patterned removal of periodic holes leads to equibiaxial stress states, while fine-pitched orientated removal of periodic troughs generates non-equibiaxial stress components,' she explains.
It is the combination of these two features, together with proper rotation of the trough orientation, that creates stress states, which, in principle, can be used to correct any type of error term in the mirrors. Significantly, the SNL team’s multi-pass correction scheme introduces a feedback loop.
'Most stressed-based figure correction methods are only capable of applying one correction pass, even if the target mirror profile has not been reached,' Zuo explains.
'In comparison, femtosecond laser micromachining enables a multi-pass correction scheme, where a feedback loop is implemented to reduce the figure error terms repeatedly.'
So far, the research has been demonstrated on flat silicon wafers with regular patterns. The researchers hope to develop a more complex optical set-up to correct real X-ray astronomy telescope mirrors, which are curved in two directions.