Fast-setting cement solution?
Scaling up calcium sulphoaluminate cement manufacture.
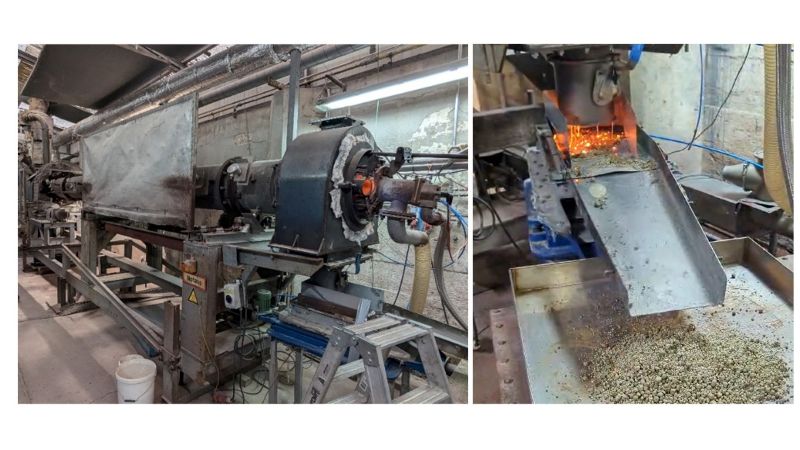
The cement manufacturing process is well known for being energy intensive and emits approximately 0.8kg of CO₂ for every kilogramme of traditional Portland cement (PC) clinker produced.
The combination of high emissions, coupled with the scale of production (4Bt globally annually) contributes to roughly 8% of total anthropogenic CO₂ emissions worldwide. To put this in perspective, if the cement manufacturing industry were a country, it would rank as the third-largest emitter of CO₂, only succeeded by China and the US.
The Green, Circular and Smart Cement Manufacture project – part of the UK Research and Innovation Future Leaders Fellowship – is exploring innovative approaches to manufacturing alternative, low-CO₂ binders using industrial by-products and waste materials.
The aim is to enable calcium-sulphoaluminate-based (CSA) cements manufacturing in the UK.
Keeping up with calcium
CSA-based cements are a promising alternative, low-CO₂ binder to the traditional PC.
One of the main advantages of the CSA manufacturing process is its compatibility with the existing PC-manufacturing infrastructure. The raw materials used for manufacturing CSA cements are also similar, though CSA uses less limestone and more alumina and gypsum.
Despite this, the widespread manufacturing and use of CSA cements have been limited due to the higher manufacturing costs, mainly attributed to the cost and availability of bauxite, which was believed to be a necessary source of alumina.
About 90% of CO₂ emissions in the cement manufacturing process comes from the calcination of limestone and the fuel burnt to achieve the required kiln temperature. PC binder systems have alite (C₃S) as the primary reactive phase (note: cement chemistry notations, C: CaO, A: Al₂O₃, S: SiO₂, $: SO₃), and it is a lime/calcium intensive phase that requires an operational synthesis temperature of ~1,450°C.
Did you know?
Although the interest in calcium sulphoaluminate (CSA) cements as a low CO₂ binder has increased in recent times, CSA cements have been commercially used for decades as a special cement.Initially patented by Alexander Klein in 1966 as an expansive binder, CSA cements have evolved into standalone binders over time.
Unlike PC, CSA binders have ye’elimite (C₄A₃$) as the primary clinker phase. The synthesis of the ye’elimite phase requires less limestone and lower kiln temperatures, meaning lower process (raw material) and fuel CO₂ emissions.
CSA cements typically have ye’elimite with belite (C₂S) and calcium sulphate (C$) as the other primary clinker phases.
Additionally, CSA cements are reported to have a porous clinker structure, reducing the energy needed for grinding the clinker. This translates to an overall 25-35% reduction in CO₂ emissions in manufacturing compared with PC, based on their phase assemblage.
CSA cements, based on their phase composition, have different terminologies – such as the belitic calcium sulphoaluminate (BCSA).
The cement’s properties also are directly linked to its clinker phase composition. By changing the composition of the primary clinker phases ye’elimite, calcium sulphate and belite, we can vary the cement’s characteristics, such as being rapid hardening, achieving a high early-age strength, self-levelling, cavity/mine/bulk filling, expansive and self-stressing.
The rapid setting and expansive nature of the CSA cements make the construction process faster, easier and enhance structure service life. The durability performance after decades of service has also recently been shown as good, with a wide range of applications such as concrete for bridges, infrastructure buildings, runways and taxiways for airports, pavement concrete road-repair and production of concrete pipes.
The compressive strength typically increases with the ye’elimite content. Increasing the gypsum content relative to ye’elimite enhances the expansion characteristics, however, this would also increase the manufacturing cost due to the higher demand for alumina.
The BCSA cement with the composition of about 20-30% ye’elimite and 50-60% belite could be an optimal balance, diminishing the requirements for high-alumina-containing raw materials and enabling the use of high-alumina clay instead (with additional alumina supplements where required).
Blending recycling
BCSA cements can achieve similar strength to PC but in a much faster timeframe. The ye’elimite phase would hydrate rapidly, forming a dense microstructure at early ages (within a few hours) and contributing to the hardening and early-age strength. Belite hydration at later age contributes to long-term durability performance.
PC binder also often relies on supplementary cementitious materials (SCM) like fly-ash or ground-granulated blast-furnace slag to reduce the overall carbon footprint (and improve durability). However, BCSA cements can achieve the desired characteristics without them and can also be blended with gypsum (calcium sulphate) to alter/refine the mechanical properties, such as compressive strength and expansion.
This distinction is critical when recycling cementitious materials, as the hardened cement paste of a blend cannot be readily refired into a clinker. One of the crucial steps in making the cement industry sustainable would be to include circularity in the cement manufacturing process.
While recycled concrete aggregates have been successfully reused, this process always leaves behind the discarded cementitious fines, composed of hardened cement paste, and could potentially be used as a raw material for manufacturing cement. However, when PC systems are used as PC-SCM blends, the chemistry of the originally manufactured clinker significantly changes.
PC systems, depending on C₃S for the hardening and early-age strength, require a high-lime content to synthesise. This limits alternative materials and lower-grade limestone use to produce PC, as the raw meal has stringent chemical limits to ensure the required phase assemblage forms during clinkering.
So, when PC-blended hardened cement paste must be reused, this requires an additional dose of lime to meet the requirements of the raw meal.
BCSA cement, on the other hand, can be fully recycled at the end of life, especially if the sulphate source is produced in the kiln as anhydrite. The recycled cement can be incorporated as a raw material for the raw meal. BCSA typically is used directly or blended with gypsum, which is also one of the raw materials used for synthesising and so does not affect the raw meal.
Further to this, BCSA cement can accommodate alternative low-grade materials in the raw meal if used in a diluted manner.
Overall, when used in applications where time is of the essence, BCSA’s cost could easily be justified, however, it may never replace PC for all commercial applications. If we can use alternative cheaper sources of alumina, we can potentially also make BCSA an economically direct alternative.
Actualising alternatives
The main bottlenecks for BCSA cement is its high-alumina demand, in particular in the UK where bauxite is scarce. This can be overcome by using alternative industrial by-products.
Several researchers have worked on synthesising BCSA at laboratory scale using alternative materials rich in alumina, such as fly-ash (from coal combustion), granulated blast-furnace slag (from steel manufacturing),aluminium sludge (from water treatment), alumina slag and red mud (from aluminium manufacturing).
However, alternative materials come with their own logistics and technical challenges. To name a few, the local availability of the material, and the inevitable impurities and minor elements present in them. These minor elements could affect the clinkering process, but if used in diluted amounts, the adverse effects can be diminished.
In this study, we focus on using one such alternative alumina-rich material, understand its implications on the clinker and check the feasibility of using it for manufacturing BCSA cement in a semi-industrial trial using only UK-sourced materials in the raw meal. The by-product from the secondary aluminium production process was identified as an alumina source from within the UK.
Recycling aluminium from scrap is achieved using the secondary aluminium process. Aluminium is one of the most recycled materials, with over 30Mt of scrap aluminium being recycled globally, according to the International Aluminium Institute.
The recycling is accompanied by considerable amounts of by-products. A salt flux is added with the scrap metal to remove the impurities, which is finally collected as the slat slag. This is refined to extract the viable aluminium and leaching the salts to be reused in the process, leaving behind the non-metallic by-product (NMP).
NMP is considered a waste material, has found limited commercial applications and typically dumped in landfills bringing economic and environmental pressures. Although viable aluminium has been extracted, NMP ends up with over 60% of Al2O3, making it a potential alternate alumina source.
With the UK consuming about 144,000t of secondary aluminium annually, the case for using the NMP to benefit the circularity of materials in our Foundation Industries is strong. For the first time, we demonstrate the use of locally available raw materials in the UK to manufacture BCSA in a rotary kiln.
From lab to kiln
Preliminary studies at laboratory scale have explored the feasibility of using NMP in the raw meal for synthesising BCSA cement. The raw materials for the study – limestone, gypsum, different sources of clay and NMP – were sourced locally within the UK.
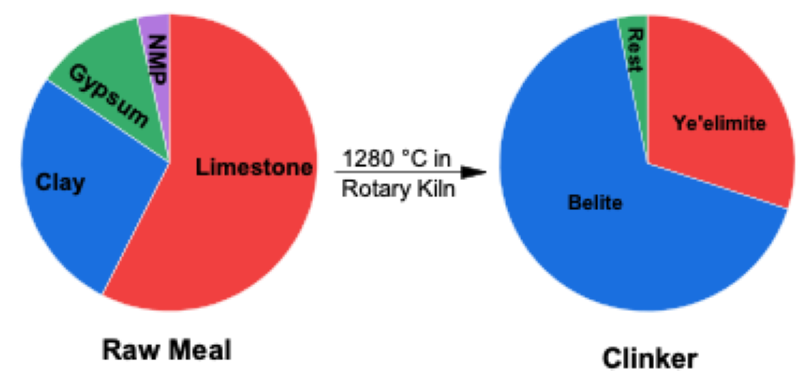
The raw meal for clinker trials used different raw materials, so the targeted clinker composition has approximately 30% ye’elimite and more than 60% belite (as a BCSA cement). By varying two key parameters – maximum clinkering temperature and dwell time (the residence duration at the peak temperature) – numerous clinker samples were produced.
The clinker samples were characterised and analysed to quantify the clinker phases and understand the role or effect of the minor elements on the clinkering reactions. The results show the influence of both the raw materials and clinkering conditions on the clinker formation. Based on these findings, one recipe and a set of clinkering conditions were selected for the pilot-scale trial.
The up-scaling of BCSA cement manufacturing was conducted at IBU-tec Advanced Materials AG, Germany, using a pilot kiln. The kiln, with the dimension of 0.3m-internal diameter and heated length of about 7m, uses a direct-fired natural gas burner to reach the required temperatures.
One of the main challenges of BCSA production in the kiln is managing the sulphate content of the raw meal. The synthesis of ye’elimite requires a temperature of ~1,250°C, but the high temperature or prolonged dwell time (which can be caused by process/kiln configuration) can lead to loss of sulphur, altering the chemistry.
The environment of burning of natural gas can further create pressures, accelerating desulphurisation from calcium sulphate and ye’elimite. Thus, the key process parameters, such as the meal feed rate and form, kiln inclination and rotation, and maximum temperature, must be optimised to ensure the samples have sufficient time at the sintering temperature for completion of the clinkering reaction and not cause significant desulphurisation.
The pilot trial lasted for more than five days, using about 3,000kg of raw materials and successfully producing more than 1t of targeted BCSA clinker. The details of the raw meal and composition of synthesised clinker are shown in the pie chart opposite.
The raw materials were characterised onsite to check their oxide composition and moisture content, to correct the raw meal proportions.
The raw meal was made using the different raw materials in the required proportions, in batches of 200kg. The raw materials were blended and granulated in a mixer at 1,500‒3,000rpm (optimised based on preliminary studies) to obtain granules in the size range of 1-5mm.
The granulated samples were then continuously loaded into the pre-heated rotary kiln in the temperature range of 1,260-1,280°C (based on the findings from the lab-scale trial). The kiln was set to a 1.5° inclination and rotation speed of 2-2.5rpm, with a feed rate of 25kg/hr for the raw meal granules.
These process parameters were selected to ensure the products had about 15 minutes in the sintering zone (totally 60 minutes in the kiln), for the clinkering reactions to be completed (based on the findings from the lab-scale).
The rotary kiln and the hot clinker coming out of the kiln is shown in the main image. As a part of the quality assurance for the clinkering process in the kiln, the temperature, air-flow rates and pressure were monitored in real time. The temperature was monitored using thermocouples attached to the kiln at six different locations. Additionally, the temperature of the samples was monitored using a manual pyrometer periodically.
The temperature profile to the left shows the sample temperature (T0) and the temperature of the kiln at three locations – near the inlet (T1), mid-way through the kiln at about 4.5m from the burner (T2), and near the burner, closer to the sample outlet (T3).
Further, the clinker produced was periodically sampled every 2-3h and characterised throughout the trial using X-ray diffraction. The clinkers are predominantly found to meet the target phase assemblage, with minor fluctuations, proving the robustness of the process. The pilot trial has demonstrated the viability of using UK-sourced materials to steadily and consistently manufacture over a tonne of BCSA cement.
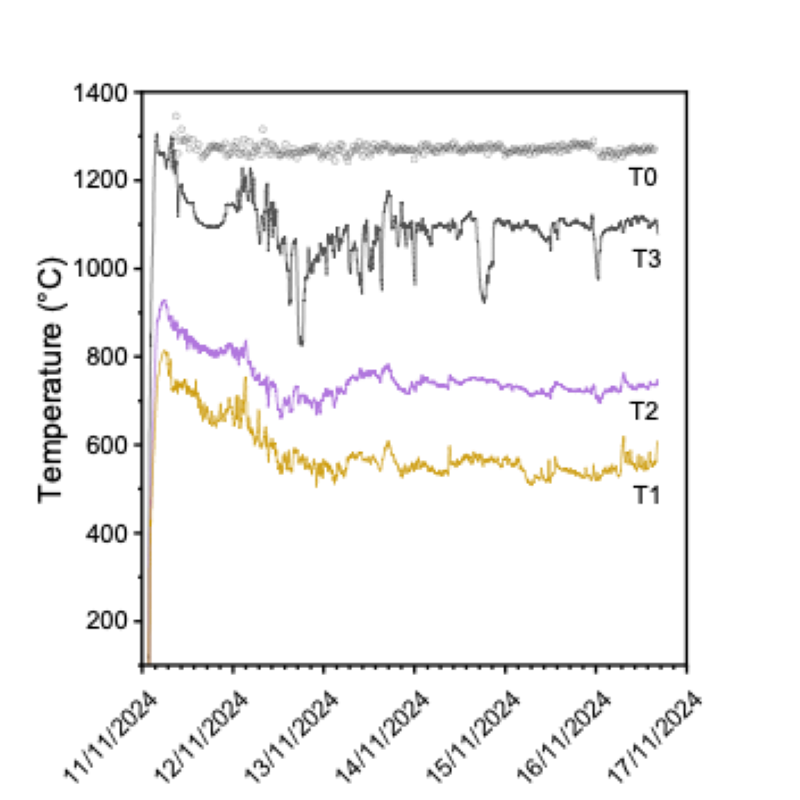
What’s next?
The next phase of the project will focus on demonstrating the performance and applications of the manufactured BCSA cement using real-world sized members. The quantity produced in the pilot trial allows for a suite of practical tests that would not normally be possible when producing materials in the laboratory at gramme scale.
After detailed studies on the mechanical and durability characteristics of the binder, the BCSA cement will be used for a small-scale demonstration project. As a fast-track project, an access ramp facility is being planned, with the site expected to be ready for public use within just one to two days of construction. This project would pave way for commercial development and adoption by the UK industry and beyond.
The overarching aim is to enable the manufacture of CSA-based cement in the UK by 2030.
This work was funded by UKRI Future Leaders Fellowship on Green, Circular and Smart Cement Manufacture (MR/V023829/2). We would like to thank IBU-tec Advanced Materials AG, Germany, and in particular Steffen Kaiser and Robert Süße for the continuous support prior to, during and after the pilot kiln trial, which was conducted in November 2024. We also thank Altek (Harsco), Imerys, British Gypsum (Saint Gobain) and ARUP for providing us with the materials used in this work.