Fabrics to composites
Recycling cellulose textiles could put the brakes on fast fashion. Professor Mike Ries, Dr Peter Hine FIMMM and Luke Mancell at Leeds University, UK reveal a circular economy approach to wearing out our clothing.
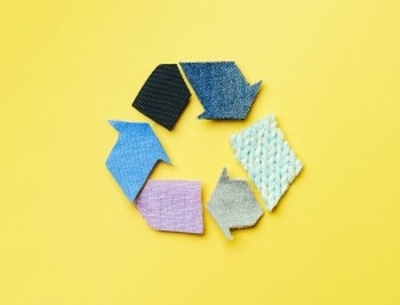
Cellulose is the world’s most abundant biopolymer, with approximately 1.5 trillion tonnes produced each year by plants, algae, bacterial secretions and various microorganisms. Cellulose has a chemical formula of (C₆H10O₅)n, where n is the degree of polymerisation, typically ranging from 300 up to 10,000.
Cellulose units join together to form chains which, through hydrogen bonding, attract each other to form cellulose microfibrils that have been found to possess useful properties such as high shear and tensile moduli. Reported Young’s modulus values of cellulose are as high as 200GPa, similar to steel (190-215GPa), yet it only has around a fifth of steel’s density. Additionally, the estimated ultimate tensile strength of cellulose can reach 17.8GPa, seven times higher than steel.
This has sparked great interest in cellulose for numerous applications such as in building materials and the automotive industry. Even more promising is the emergence of all-cellulose composites (ACCs), which could be a potential substitute to many commonly used materials that lack recyclability and biodegradability.
In 2004, an ACC comprising cellulosic fibres bound together by a cellulose matrix was first achieved by Takashi Nishino, Ikuyo Matsuda, and Koichi Hirao at Kobe University, Japan. The authors employed a two-step method, where 1) cellulose was dissolved into a solvent and then 2) cellulosic fibres were immersed into that cellulose solution. Methanol was used to coagulate the cellulose and after drying, an ACC was formed.
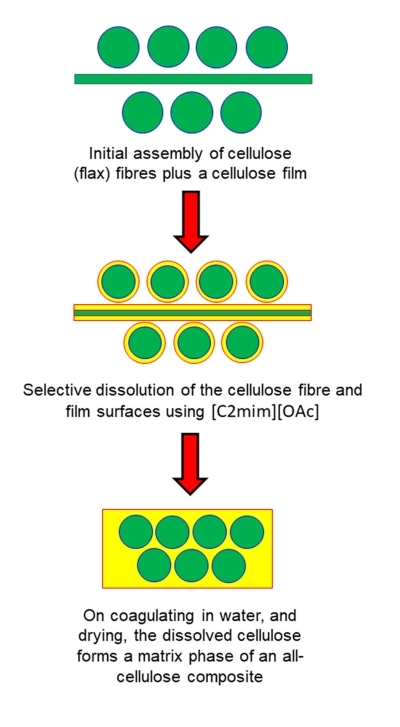
A year later, Wolfgang Gindl at the University of Natural Resources and Applied Life Sciences, Vienna, Austria, and Josek Keckes at the University of Leoben, Austria, used a one-step method, partially dissolving microcrystalline cellulose in a solvent, then coagulating and drying to form an ACC. In 2007, Nishino and Noriko Arimoto, again at Kobe University, adapted this with surface-selective dissolution of cellulose fibres, sample compression, solvent extraction and sample drying consecutively performed to produce an improved ACC. The main advantage is the ability to more precisely control the fibre surface’s dissolution, allowing for increased bonding between the fibre reinforcement and the matrix upon coagulation. This modified procedure also eliminates issues that hinder large-scale manufacture using the two-step method, such as the difficulty of incorporating the viscous-dissolved cellulose solution into the cellulose fibres.
Peel parameter
Current research at the University of Leeds, is investigating ACCs as possible green composite materials with the potential to be biodegradable. This is partially inspired by previous successful research and commercialisation of an all-polymer composite, which was highlighted in Materials World back in October 2007 (page 37). Here, heat was used to melt the surfaces of the individual polymer elements, which on cooling formed the matrix of the single-polymer composite.
This work has been coupled with an investigation into cellulose dissolution using novel and environmentally safe solvents such as ionic liquids. As cellulose does not melt, an ionic liquid (1-ethyl-3-methylimidazolium acetate [C2mim][OAc]) is used to partially dissolve the surfaces of each cellulosic element, see the schematic above. These surfaces then coagulate in water to form a matrix phase (shown in yellow) bonding the structure together. A final drying stage removes the water and a composite sheet is formed.
It is known that ionic liquids often have a maximum cellulose dissolving potential of around 20%. This proportion of a dissolved and coagulated matrix phase is not normally high enough to create a fully bonded and homogeneous composite. Therefore, we have added cellulosic film layers to the original assembly.
In this patented process, the film surfaces are now partially dissolved leading to a final composite with a high interlayer strength, while still retaining a significant fraction of the original cellulose fibres, which in these original studies was in the form of a woven flax cloth.
The structure within the ACC is of course more complicated than that shown in the schematic above, a typical micrograph is shown above in image (a). It shows how the film – in this case, two layers are used in between each layer of the woven flax cloth – is able to follow the internal contours and form an effective ‘adhesive’ layer. The additional layer increases the peel strength by an order of magnitude. The peel strength is an important parameter determining whether the material will hold together when subsequently formed into a required shape.
The current iteration of the ACC production method is a batch process, although research is ongoing with the overall vision for a continuous process.
Old pair of jeans
Now we come to different starting cellulose sources. The topic of fast fashion has been a hot talking point over the last year. Here, we show how the process can work on recycled cellulose textiles.

Some examples of these are shown above where (b) is an ACC sheet made from woven, natural undyed flax (cloth weight 100g/m²). The table below shows some typical mechanical properties from this composite. Examples (c) and (d) show cotton-based materials: (c) was made from recycled denim taken directly from a recovered pair of jeans, while (d) was made from green cotton and subsequently laser cut.
Although the manufacture of flat composite sheets from textiles is an interesting step, the potential of such composite materials is always increased if they can be formed into a variety of shapes.
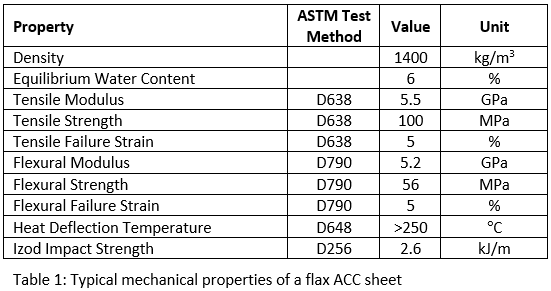
Traditionally, the route to such shaping is via thermoforming. However, cellulose is not susceptible to heat – which is the reason for the exceptional heat deflection temperature of >250°C, seen in the table above. Therefore, another strategy is required. It is well known that water – coupled with a gentle application of heat – can be used to bend or form wood, for instance, in archery bow construction. As these ACC materials can be considered a close cousin to wood, we have used this as inspiration.
Shape of things to come
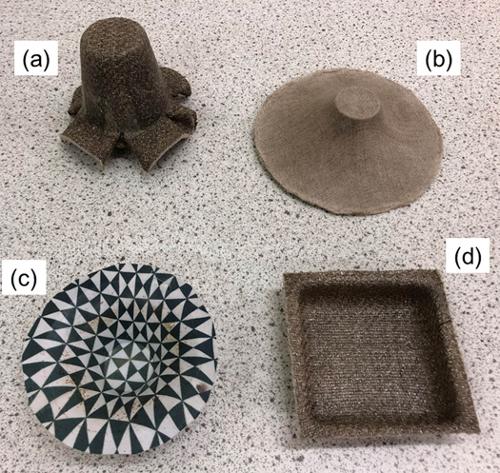
A process that we have termed ‘hydroforming’ can create ACCs with a range of shapes as shown below. These sheets are first soaked in water to significantly increase their strain to failure, while reducing their modulus and hence resistance to deformation. While we have found that heat is not required for forming – as expected it does not further increase failure strain or reduce the modulus – if the forming process is carried out at 100°C using matched metal moulds, then the part can be formed and dried at the same time. In the image below, (a) shows a plant pot type shape from a natural flax ACC sheet, made in this way using matched metal moulds, while (b) shows a loudspeaker cone-type shape. Image (c) was formed in the same loudspeaker mould but using a white cotton ACC sheet that had been previously printed by a local artist (Dominic Smith) to produce a visually striking final shape. The final picture (d) shows a tray type shape formed in the same way.
Of course, advantageous aspects of materials can also turn out to be a disadvantage. Composite materials that can easily be thermoformed then have to be kept away from the same elevated temperatures during use. For an ACC, as with most cellulose-based materials, the ability to be easily ‘hydroformed’ is a substantial advantage, however, this leaves it susceptible to water. We have found that standard varnishes work very well to waterproof an ACC sheet if exposure/resistance to moisture is important in the final application.
With calls for a makeover of the fashion industry towards a more circular economy, the ability to transform recycled cellulose textiles in such a way for a variety of applications could prove valuable.
Did you know?
Every second, the equivalent of one garbage truck of textiles is landfilled or burned globally. If nothing changes by 2050, the fashion industry will have used up a quarter of the world’s carbon budget.
Source: UN Environment