EV battery production from recycled cathode active materials
The UK's first electric vehicle (EV) battery cells have reportedly been produced using recycled cathode active materials (CAM).
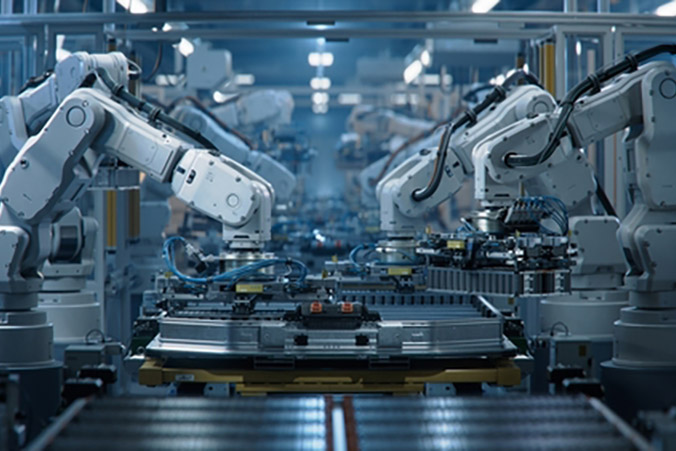
Industrial robot arms assemble EV battery pack inside automotive smart factory
© IM Imagery / ShutterstockThe pouch cells were manufactured at the UK's at the UK Battery Industrialisation Centre in Coventry using recycled CAM from Altilum's recycling facilities in Devon.
The battery cells will now undergo validation studies with an automotive original equipment manufacturer.
Under EU Battery Regulations, new EV batteries sold into the EU will need to contain minimum levels of recycled lithium, nickel and cobalt from 2031, with further increases in 2036.
Altilum shreds end-of-life batteries to produce a fine powder known as black mass. The company claims it can recover more than 95% of the critical battery metals, including lithium. The cathode metals are upcycled to produce a nickel-manganese-cobalt 811 CAM for re-use.
The group's planned ACT4 recycling plant in Teesside should produce 30,000t of CAM a year – which it says is enough to meet nearly 20% of expected UK demand by 2030.
Imperial College London has found that Altilium's recycled EV battery materials can match, and even surpass, the performance of virgin mined materials, enabling longer battery life, faster charging times and lower costs.
Lifecycle analysis from Minviro has found that cathode materials produced using the recycled materials could be 74% lower in climate change impact compared to using primary mined materials from a Chinese supply chain.
This news comes as Toyota Motor Europe announces a Toyota Circular Factory to process vehicles at end-of-life at its plant in Burnaston, UK.
Toyota says activities will begin in the third quarter of 2025 and aims to become a centre of excellence for future recycling operations across Europe and globally.
The plant aims to process vehicles around three key areas: re-usable parts, commodity items that can be re-manufactured, and materials that can be recycled.
Finally, Toyota intends to recycle raw materials such as copper, aluminium, steel and plastic. These recycled materials would then replace virgin materials as much as possible in the production of new parts for new vehicles.
'We initially anticipate recycling around 10,000 vehicles a year in our UK facility, which will give new life to 120,000 parts, recover 300t of high purity plastic and 8,200t of steel - among other materials,' comments Leon van der Merwe, Vice President of Circular Economy at Toyota Motor Europe. 'As a next step for the Toyota Circular Factory concept, we plan to roll out similar operations across Europe.'