Engineering timber
Dr Martin P Ansell FIMMM, Honorary Reader in Materials at the University of Bath, UK, presents latest research in wood science and timber engineering, and how this supports the wider construction industry.
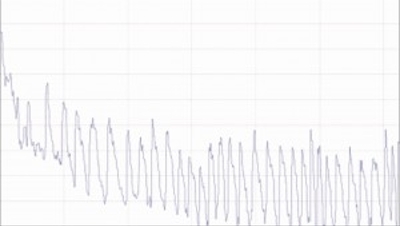
The extraordinary versatility of wood and its role in construction is reflected in recent advances in science and timber engineering. The understanding of wood science is a pre-cursor to optimising the structural performance and durability of wood and its composites, and their application in timber engineering.
Wood may be defined as the cellular, fibrous material that forms the trunk and branches of a tree, while timber is wood prepared for use in building and carpentry following felling, sawing and drying. In addition to solid timber, there are many composite timber products based on sawn wood or wood veneers, including plywood, cross-laminated (CLT) and glue-laminated timber (glulam), and laminated veneer lumber (LVL).
Microstructure and measurement of microfibril
Commercial transmission and scanning electron microscopes have been in common laboratory use since the early 1970s, revealing the intricate microstructure of wood.
Softwoods such as Scots pine and Douglas fir have cell dimensions of approximately 30 micrometres, with each cell being a multilayer composite with concentric primary and secondary cell walls. The S2 layer is the thickest and contains a right-hand spiral of cellulose microfibrils, in a matrix of lignin and hemicellulose. Cellulose is nature’s stiffest polymer so to maximise the mechanical properties of wood along the grain, the angle of the cellulose microfibrils to the cell axis – the microfibril angle (MFA) – should be minimised and, in general, the density of the wood should be maximised.
The MFA and density can be measured using the SilviScan-3 system. A thin radial strip of wood from the pith to the bark is carefully machined and scanned with an X-ray densitometer, an optical microscope, a digital camera and an X-ray diffractometer. The system measures MFA and annual ring density as a function of the radial distribution of annual rings, each one comprising lower density early wood and higher density latewood.
As shown on the image pictured, measurements made at 200 micrometre intervals are plotted as a function of distance from the pith across 32 annual rings. Beyond the first few annual rings, close to the pith, the MFA settles down to a range from approximately 15° in the earlywood to close to 0° in the latewood. Hence, the SilviScan-3 system allows foresters to evaluate the potential of forest or plantation-grown timber as a function of location with remarkable accuracy. From this, high-grade timber can then be supplied to the construction industry.
Transparent and densified wood
Researchers at the Wallenberg Wood Science Center at Stockholm’s KTH Royal Institute of Technology, Sweden, and the University of Maryland NanoCenter and Energy Research Center, USA, reported on developing optically transparent wood in 2016. To achieve this, part of the lignin content of the wood is removed by soaking it in a solution containing sodium hydroxide and sodium sulphite. Hydrogen peroxide solution is used to remove the remaining lignin, following which the wood colour becomes lighter. Wood is vacuum infiltrated with optically matched epoxy resin or methyl methacrylate. An optical transmittance of approximately 85% and haze – amount of light diffused or scattered – of 71% are achieved and the wood cells act as waveguides.
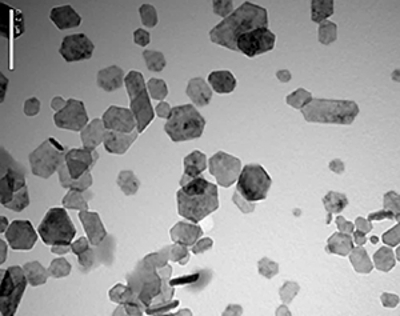
A similar chemical treatment with sodium hydroxide and sodium sulphite, followed by pressing, is employed to produce densified wood. For this, the cell cavities in the wood are completely collapsed and the cellulose microfibrils in the cell wall become well aligned. This results in a similar density to commercial densified wood, but in an adhesiveless process unlike established adhesively bonded densified products. Specific tensile strengths – tensile strength divided by density – greater than most structural metals and alloys, including high specific strength steel and lightweight titanium alloys, are claimed. Compared with unmodified wood, strength is improved by a factor of 12 and work of fracture by a factor of 10. A later study in 2018 reported cross-laminated densified wood to have outstanding ballistic resistance.
Carbonised wood composites
New materials based on carbonised wood are produced by pyrolysing wood in argon at 650-1,000°C followed by infiltration with liquid metals and semi-metals. One approach is to infiltrate the cellular carbonised framework with liquid silicon by capillary action at temperatures greater than 1,450°C under vacuum. The silicon reacts with the carbon to form silicon carbide. Good thermo-mechanical properties result with applications including heating elements, high temperature absorbers and medical implants.
A second approach is to react carbonised wood with titanium metal powder in a molten salt mixture of potassium chloride and potassium fluoride at temperatures between 700-1,000°C. Titanium carbide crystals formed on the surface of the carbonised template resulting in high porosity and strength. Potential applications for TiC/C ceramic composite include high temperature resistant exhaust gas filters, catalyst carriers, wastewater treatment and acoustic and heat insulation structures.
Lastly, one can vacuum infiltrate carbonised wood with molten aluminium alloy to fill cell cavities. The resulting fibrous structure is a reverse metal matrix composite with low thermal expansion coefficient and mechanical properties dependent on the wood porosity.
Nano-coatings for wood
Multifunctional nanomaterials are applied to timber by surface coating for applications in buildings.
Anti-fungal and biocidal coatings are based on silver, zinc and copper. Prevention of UV discolouration is achieved with oxides of titanium, zinc, silicon, iron and cerium. Photocatalytic, self-cleaning and depolluting coatings are usually based on titanium and zinc oxides. Oxides of silicon and aluminium together with clays and lime enhance the scratch-resistance of timber as well as providing it with increased hardness and wear resistance.
Further advantages of applying nano-coatings to timber result in improved waterproofing, anti-wetting and anti-staining qualities, enhanced fire-resistance, and deacidification.
Whole log X-ray scanning
Moving from the forest to the sawmill, much has happened in recent years to maximise the quality and yield of sawn timber. Computed tomography (CT) whole log scanning with X-rays has been introduced in many sawmills around the world by Microtec of Bressanone, Italy. CT scanning through 360 degrees produces a 3D reconstruction of the sawn tree trunk to reveal internal defects including knots, pith, splits, resin pockets, embedded bark and decay pockets. The maximum feed speed is up to 180m/min. With reference to the distribution of defects, the system designs an optimum cutting pattern based on maximum value recovery.
Robotic timber construction
In a collaboration between Architecture and Digital Fabrication, ETH Zurich and ROB Technologies AG, Switzerland, robotics has been used to manufacture industrial timber structures using additive digital fabrication techniques. Throughout, the timber components are grasped, manipulated, positioned and fastened robotically. A six-axis overhead gantry robot at ERNR Holzbau AG enables fully automated fabrication of lattice girders. Gripping, positioning, trimming and nailing take place in a maximum workspace of 48m x 6m x 1.9m.
Hybrid timber structures
Timber frame and glulam buildings are well-established as materials of choice for domestic dwellings, industrial premises, sports stadiums and supermarkets. The 21st Century has seen a growth in the construction of spectacular hybrid structures which incorporate timber.
For example, the Savill Building in Windsor Great Park, UK, is comprised of a double curvature roof connected via steel transfer plates to a steel perimeter tube, connected in turn to tubular steel legs supporting the whole structure. The double layer grid roof is built from long timber larch laths, spliced together from defect-free pieces, and clad with green oak from the Windsor estate.
The Richmond Olympic Oval, Vancouver, Canada, is a hybrid structure with a composite glulam/steel roof mounted on a concrete and steel substructure. The wood/steel arches span 100m with hollow triangular sections that mechanical, electrical and plumbing services pass through. Furthermore, the glulam incorporates spruce-pine-fire wood affected by mountain pine beetle infestation.
Other examples of hybrid buildings in the UK include Curtain Place, B&K and the Sky Believe in Better Building, both constructed by B&K Structures. Curtain Place is a six-storey development situated in Shoreditch, UK, comprising hybrid steel and CLT. The Sky Believe in Better Building is a hybrid structure situated in Osterley, West London, UK, comprising a glulam frame with CLT floor, roof and stability walls, together with perimeter wall cassettes.
Tall timber buildings
Inevitably, construction with timber brings us to headline-grabbing tall timber buildings. Treet – The Tree – is a 14-storey residential tower, 49m in height. It comprises prefabricated building modules with structural glulam columns for stiffness connected by steel plates and dowels.
CLT floors and walls are mounted independently of the glulam framework. Fire safety is ensured by fire stops on the façades for every second storey utilising the horizontal glulam beams in the external trusses. Fire-resistant lacquer is applied to wood surfaces and there are intumescent fire seals in gaps between timber members. Fire safety is further enhanced by a sprinkler system and the provision of elevated pressure in escape stair shafts for safe evacuation.
Until recently, the tallest timber building in the world was the Brock Commons Tallwood House located on the University of British Columbia campus in Canada. It is 53m-high, with 17 storeys of CLT panels supported on glulam columns with reinforced concrete stairwells and lift shafts.
The timber elements are encased in gypsum board and the whole building is protected by an automatic sprinkler system. The compartmentation of the building and the design of coherent, sealed joints limits the spread of fire. The façade cladding is comprised of a high-pressure laminate containing 70% wood fibre which exceeds Canadian fire ratings.
In March 2019, the 85.4m-high Mjøstårnet was opened in Brumunddal, Norway, and is now the world’s tallest timber building. The structure is based on large glulam trusses, columns and beams with CLT walls for secondary load bearing. The 18-storey building has a floor area of 11,300m2 and contains a hotel, restaurant, apartments, offices and a rooftop terrace. External panelling is heat-treated thermowood impregnated with fire retardant.
A review of the academic and commercial literature reveals much exciting activity in wood science and timber engineering. Wood is essentially made from sequestered carbon dioxide and water so, without getting into an environmental debate comparing wood with other engineering materials, it is beneficial to lock up carbon by growing more trees and producing more timber products and structures.
The unabridged version of this item can be found here.