Enabling technologies to boost roll & mill performance
Watch on-demand
Please login or create your My IOM3 Account to access this on-demand webinar
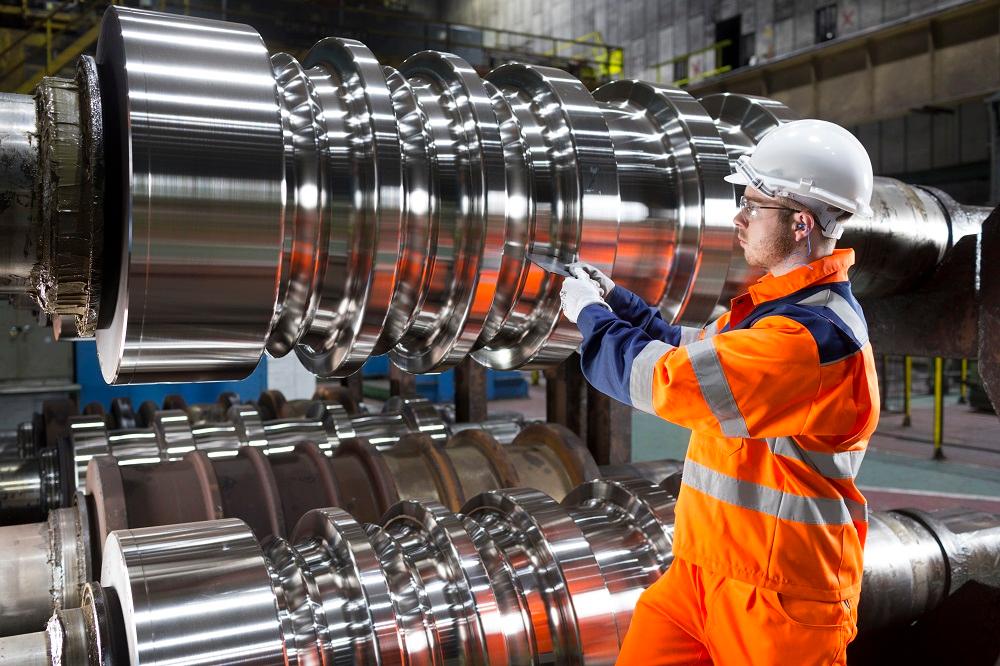
Rolling an increasingly challenging product mix amplifies the need for mills to apply advanced technologies in terms of mill and roll shop design, hardware and digitalisation, NDT systems and practices in the roll shop, complemented by rolls Value-in-Use (VIU) optimisation strategies. In this session, various technology providers will expound several types of technologies and strategies geared towards boosting roll and mill performance. The first paper will focus on enhanced Ultrasound inspection technology for optimal detection of defects in rolls. The second paper will present concepts and strategies to optimise VIU of universal sleeves for section mill rolls. The third paper will explicate how continual development over decades of Roll Shop hardware, measurement technology, automation, inspection and management software and systems over many decades that have evolved into a the ‘Digital Roll Shop’ with a fully integrated suite of software based functions. In the last paper, a novel advanced grinding approach will be revealed to tailor work roll surface topographies to the specific needs of particular hot and cold rolling applications.
Enhancing Mill Roll inspection with bi-directional Ultrasound for optimal detection of all surface and subsurface defects.
The rolls used for hot and cold rolling of steel strips are subject to severe mechanical and thermal stresses that lead to contact fatigue, wear and plastic deformations. Traditionally, the tried and tested roll inspection solution is to use Eddy Currents (EC) with some limited Ultrasound testing (UT) capability. However, the traditional approach is no longer the most reliable and efficient solution for detecting typical roll defects.
This paper examines the notable advantages of implementing a multi-channel bi-directional UT approach for the detection of naturally occurring defects. The geometry of the defects corresponding to the sensor position will be comparatively analysed by a UT system oriented in different directions with a standard uni-directional UT system.
The results clearly demonstrate a bi-directional UT system is necessary for the detection of all surface and sub-surface defects. Rollmate is the only commercial system offering true bi-directional UT capability.
The Digital Roll Shop
Presented by Alberto Croce, TENOVA S.p.A (Italy)
In the current environment of machine intelligence, the Roll Shop area is required to have high levels of digitization to provide the advanced process control and data management expected by modern rolling mills.
Pomini Tenova SpA has continually developed Roll Shop automation, inspection and management software and systems over many decades that have evolved into a fully integrated suite of software based functions. Systems such as Digital Texturing, on-line machine parameter monitoring, vibration monitoring, roll inspection, continuous profile measurement and correction plus roll shop management systems are not only able to collect, share and store data but use this information for closed loop process control and management of the entire Roll Shop area.
Several recent installations combine these software functions with the state of the art equipment and roll handling to provide a fully automatic Roll Shop area that can operate with high levels of efficiency and quality with continuous monitoring while requiring minimal operator involvement.
Universal Sleeves - Strategies for use, or.... Are The Expensive Ones Really Worth It?
Presented by Simon Wright, SJW Mill Consulting Ltd (United Kingdom)
For a Heavy Section Mill using the Universal Rolling process the sleeves for the horizontal rolls are critically connected to both the product quality and operational strategy of the business. For dimensional accuracy and surface quality in terms of consistency and longevity the correct roll material choice will not restrict the business requirements to produce the products it needs to, at the time it needs to in the batch size required.
This paper demonstrates how a universal sleeve is used throughout its life and makes the direct connection between the product mix of the mill, the commercial manufacturing program required and the overall sleeve cost per tonne produced.
Different roll stock and purchasing strategies will be discussed along with their pros and cons and the concept of the “Cascade Critical Product” will be introduced to demonstrate how sleeves can be “sucked down to size” and potentially incur high costs if not proactively managed.
Finally, the wear performance of different materials will be presented and connected to the overall cost of the rolls per tonne produced in different operational and strategic scenarios.
Surface Roughness Engineering for Rolling Mill applications - Tailored work roll surface topographies by advanced grinding
Presented by Danny Beentjes,, Tata Steel (Netherlands)
In roll shops for rolling mill rolls, grinding of work rolls according to the current state-of-the-art is focused on the following aspects:
- To remove surface layers degraded in the previous mill campaign (e.g. by wear, thermal/mechanical fatigue, oxidation-corrosion or damage from a mill incident);
- To (re-)apply the prescribed work roll profile;
- To achieve the correct roughness level, as specified for the applicable rolling mill stand.
- To grind without typical grinding surface quality deviations, such as feedlines, scratches/”comma’s”, chatter marks, burn marks or chevron patterns;
- To achieve (1) to (4) in the shortest possible grinding time.
Concerning aspect (3), the ground roughness is influenced by multiple factors, strong depending on the type of grinding wheel that is used, the bonding system & openness achieved by the manufacturing of the wheel, the grinding type of grit & wheel hardness.
The engineering of the surface roughness is mainly done on the (local) grinding machines (CNC, conventional), machines wherein the grind parameters are set and tuned, towards the desired surface finish. In general the developed mechanical roughness is measured by 2D stylus measurement with an mechanical device (according to the ISO4287 standard). The roughness parameter Ra, or mean average roughness profile derived from the stylus, is commonly used as the sole parameter to prescribe the work roll roughness in the Roll Shop for the rolling Mill application. The prescribed Ra roughness range is typically based on past experiences and is supposed to ensure a work roll surface finish that is more or less fit-for-purpose for the next mill campaign.
However, the same Ra roughness range can be achieved in many different ways, depending on the combination of work roll properties, grinding wheel properties and grinding machine settings. Experience has shown that work rolls ground in different ways – despite of having the same Ra roughness level – can exhibit significantly different behaviour in the rolling mill. Focusing on achieving the prescribed Ra roughness alone on the work rolls in the roll shop may therefore lead to sub-optimal or even poor mill performance.
Ground surface roughness topography, research, design & engineering is focussed broader and is about developing the most effective 3D ground roughness topography, best fit for the aimed rolling Mill application. As example, as part of the Tribology in the Mill bite, the effect on friction coefficient in the Cold Rolling Mill is a function of both the strip and work roll roughness. The Stribeck theory & curve describes a non-linear function of emulsion-lubricated surfaces and the friction coefficient.
The Stribeck theory on lubrication regimes is based upon the input of the (2D) Ra-roughness parameters of both the strip and the work roll to get understanding of the typical progression in the curve and its lubrication conditions (3), namely to be in:
- Boundary lubrication: load is mainly supported in the contact of both work roll and strip contact asperities, resulting in high(er) friction coefficient;
- Mixed lubrication: friction is reduced as effect of the lubrication, lowered friction coefficient, mixed lubrication is the desired condition for the Rolling Process;
- Hydrodynamic lubrication: is characterised by low friction, high skidding risk, in rolling Mills maximum avoidance to skidding and consequential risk to strip wreckage during rolling (rolling loads to go down upfront the wreck)
The 3D asperities of the combined surface roughness are found to play crucial role to these conditions and influence the behaviour of the rolling Mill process and the rolled strip quality. Illustratively, Tata Steel Europe (TSE), having Hot, Cold- and Temper Mill Rolling Mills, have pursued 3D roughness topography engineering to improve the rolling condition in a range of rolling applications, such as:
- Influence on cold rolled strip surface appearance, gloss, cleanliness (iron fines);
- Improved work roll durability: Impact on retained roll roughness, profile wear, positives in roll service lifetime and potential reuse after campaign;
- Positive effects on Rolling Mill loads, stability & rolled strip tension;
- Modified oxidation behaviour of the work roll surface in a hot rolling mill, to facilitate the build-up of a protective thin oxide layer.
In Tata Steel Europe (TSE), the research of 3D surface roughness, by optical measurements (ISO25178 standard) and the engineering of ground surface roughness topography, is seen as a key in fundamental improvement of rolling Mill processes, strip quality & Work Roll lifetime. Further 3D engineering, proved its importance in the development for hexavalent chrome-based work roll coatings alternatives and in mastering the grinding of enhanced Work Roll grades.
Confirmed Speakers