Electrochemically removing copper from steel to aid recycling
Recycling steel with electro-refining has been demonstrated by the University of Toronto, Canada, and Tenova Goodfellow.
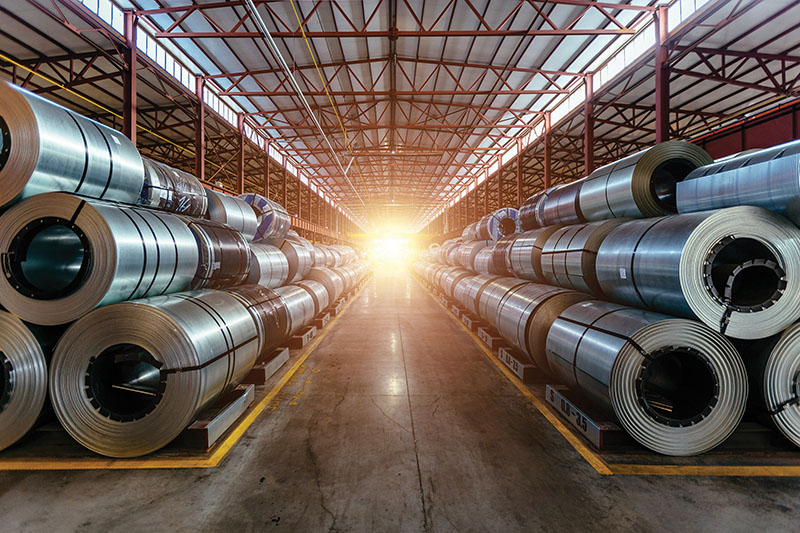
This can allow the first electrochemical removal of copper from steel and reduce impurities below alloy level, say the engineers behind it. By-products are liquid iron and sulphur.
Although only 25% of steel is recycled, the global demand is projected to grow over the next two decades.
Traditional steel recycling methods use an electric arc furnace to melt scrap metal. As separating copper from scrap before melting is tricky, it remains in recycled steel products. This can be detrimental to a material if it is above 0.1wt.%.
Also, copper concentration increases as more scrap metals are recycled, explains Professor Gisele Azimi, limiting the secondary steel market to lower-quality products, such as reinforcing bars for the construction industry.
The new approach could enable higher-grade products, such as galvanised cold-rolled coil for the automotive sector, or steel sheets for deep drawing for the wider transport sector. It uses an electrochemical cell that can withstand up to 1,600°C.
In the cell, electricity flows from the cathode to the anode through an oxysulphide electrolyte made of steelmaking waste – slag. It is fabricated by pre-treatment, chemical activation, mixing, shaping, sintering and thorough characterisation. Applying electricity to one side of the cell forces the copper to react with the electrolyte and emerge from the iron. At the other end, they simultaneously produce new iron.
The team says it decreases copper in molten iron to 790ppmw, or below 0.08wt.%, from 0.43wt.% copper content.
Azimi says slag is abundantly available, low cost, a by-product and contains a variety of oxides – including silicon, calcium, magnesium and aluminium – which are essential in many electrochemical processes. These can enhance the electrolyte’s conductivity and stability.
They plan to source slag from metallurgical processes, especially steel production, because 'the choice of slag source is critical as it determines the composition and quality of the final product', Azimi notes.
Before treatment, the metal is ground to a fine powder to increase surface area and facilitate better chemical reactions. Sieving produces a uniform size with consistency, and then the chemically activated slag is mixed with other necessary components, such as ionic conductors. The electrolyte is shaped typically into pellets or thin films and sintered for the required density and structural integrity. This needs a controlled atmosphere to prevent unwanted reactions and maintain purity.
The researchers say the technique also works with scrap iron that contains carbon and copper, removing both with great efficiency. They have tested various copper levels at 0.43wt.% and 0.21wt.%, achieving 0.079wt.% thereafter.
The whole process takes up to two hours, as any longer and the removed copper returns to the iron.
Azimi highlights that the ionic conductivity of the slag-based electrolyte is comparable to conventional ones, but using slag significantly reduces raw material costs. They did not test if the electrolyte is recyclable, but believe it can be.
The team notes the ratio of electrolyte to impure iron is large due to lab-scale limitations, and so can be reduced at pilot scale.
They hope to use the electro-refining process to remove other steel contaminants, including tin, and plan to conduct a lifecycle analysis before moving to pilot scale with the industry partner.