Electrochemically extracting lithium from brine
A direct lithium extraction technology that reportedly negates the need for water and chemicals and will be powered entirely from renewable energy is being developed by an Australian university spin-off company.
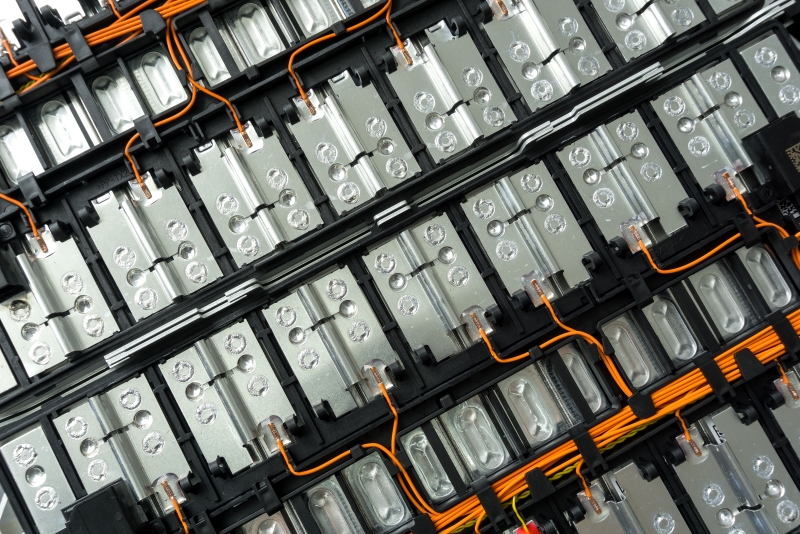
Current lithium brine recovery can take several months to years, pumping salar brine to ponds for natural evaporation. ElectraLith claims to be able to electrochemically recover, concentrate and refine lithium to lithium hydroxide within hours at a high recovery rate, with no evaporation or chemicals.
By using an electric field and a lithium-ion selective membrane (electrodialysis), lithium ions move from conductive solutions such as natural brines.
ElectraLith Chief Technology Officer Shaun Oosthuizen notes that about 1-2mln litres of water are lost for every tonne of battery-grade minerals produced by the conventional brine concentration method, which only recovers about 40% of lithium, while spodumene plants recover 70% from ore to product, with only 5% of lithium-ion batteries recycled.
ElectraLith is based on patented technology developed at Monash University, Australia, by Professor Huanting Wang.
The exact nature of the polymer-ceramic membrane used is confidential until the second-generation system is fully patented, but the parts are said to be similar to the solid-state electrolyte technology automotive companies want to use in Li-ion batteries – which similarly enables selective electro-filtration.
Oosthuizen says that the membrane technology is well-proven and seawater desalination plants have been using the same membranes for nearly two decades.
The conventional evaporation process uses ponds of various ages. The concentrated brine is filtered and ion-exchange purified to remove contaminants. Chemical solvents and reagents recover any byproducts through precipitation and the treated brine is finally dosed using a chemical such as sodium carbonate to form lithium carbonate. Technologies such as reverse osmosis are used to speed up concentration.
Oosthuizen points to the mandate from Chile, which produces around 40% of global lithium, to move to direct lithium extraction to reduce water loss in the desert. He says that a selection of direct lithium extraction technologies have emerged but most involve pH changes or require organic solvents and brine heating up to 80°C, using more energy, fresh water and chemicals.
For their electrodialysis method, ElectraLith wants to use solar or hydro energy from geothermal brines. The aim is for zero water losses and to reinject the brine into the well.
They say electrodialysis reversal will ensure the membrane is regenerated. 'We have put the use of green solvents as a priority in the manufacture of the membranes, and the polymers employed are recyclable. The ceramic is non-hazardous,' notes Oosthuizen.
He reports that the process is energy efficient, with every watt used representing the movement of charged lithium ions (as 1 mol of lithium = 1 Faraday) across the membrane.
'It represents the most energy efficient process at present.'
The membrane can be standalone or retrofitted to existing operations. Oosthuizen says they are still optimising the arrangements, as resources vary widely between geothermal brines, salars oilfield brines and battery recycling plants.
ElectraLith wants to operate at pilot scale but have tested samples from Rio Tinto sites, from lithium-bearing jararite processing in Serbia to the Rincon project in Argentina. They aim to prove the technology commercially within 24 months.