Elastane recycling in sight
A non-toxic extraction process has been developed at TU Wein in Austria to separate elastane from other textiles.
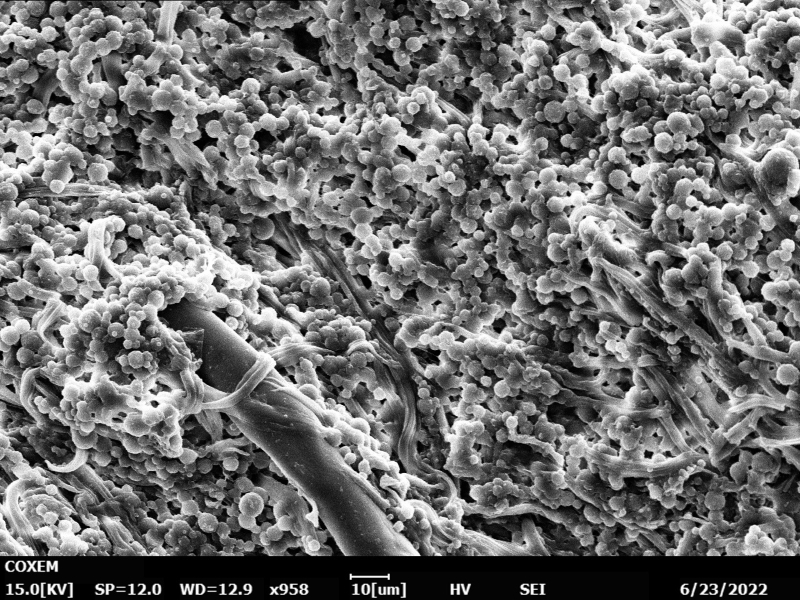
The use of the synthetic polymer fibre based on polyurethane, even in small quantities, makes recycling of mixed textiles challenging as shredders cannot cope with the stretchy material. This leads to blockages and clumping in the machines.
Here, an elastane quantification tool has been developed to detect and measure how much elastane is present in a garment. The method is based on mid-infrared spectroscopy.
The next step was to separate the elastane from other fibres. Six different organic solvents were tested for performance in dissolving elastane out of textile waste. The non-hazardous dimethyl sulfoxide (DMSO) was selected as the most favourable.
Emanuel Boschmeier, PhD candidate and lead author from TU Wien, says, 'A merger of the elastane dissolution with DMSO at 120°C for 10 minutes, solvent filtration, centrifugation and distillation, as well as the washing and drying steps for the recovered polymers, reveal the elastane separation process.'
In this way, materials such as polyester or polyamide can be almost completely separated from the elastane – and even the solvent itself can be recovered and reused.
Even when wool is combined with polyester and elastane, the individual components can be used, reports the team. The wool is broken down with enzymes under mild, harmless conditions. In the next step, elastane is separated and recyclable polyester remains.
The paper New separation process for elastane from polyester/elastane and polyamide/elastane textile waste, in the journal Resources, Conservation and Recycling, describes how dissolution experiments were conducted by putting one 3×6cm piece (around 1g) of the PET/elastane sample in a beaker filled with 150-200mL of pure solvent. Parameters such as temperatures and dwell time were adjusted next to a constant low stirring rate of 60rpm.
The paper reads, 'Samples were taken every five minutes up to 30 minutes dwell time and the low stirring rate guarantees no textile entanglement. Since it is common in industrial processes to pre-dry PET chips at ambient pressure at 120°C, this temperature was set as the maximum.'
The treated samples were then washed with tap water and pure ethanol, and then dried at ambient temperature for 72h. To determine yield, the dry mass difference before and after treatment was calculated.
In total, the paper reports 569g recovered PET and 80g recovered elastane, while 99% of the used DMSO was purified and recovered.
The paper states, 'Principal component analysis of spectroscopic measurements (ATR-FTIR) revealed excellent results for the recovered polyester and polyamide. Differential scanning calorimetry, thermogravimetric analysis and scanning electron microscopy on textile samples proved the success of the developed process.'
And, 'in principle, the process would also be applicable to textile waste containing cellulosic fibres, such as cotton/elastane or viscose/elastane, but the solvent is only partially separable from these hydrophilic fibres.'
Boschmeier says, 'Recycling of elastane-containing textiles has been repressed by the industry for years or decades and no focus was on that field until I started with that topic within the EU project System Circularity and Innovative Recycling of Textiles.'