Efficiently extracting lithium from waste liquids
At least five times more lithium is retrievable from waste liquids with a common mineral than other adsorbent materials, says a team at Oak Ridge National Laboratory (ORNL), USA.
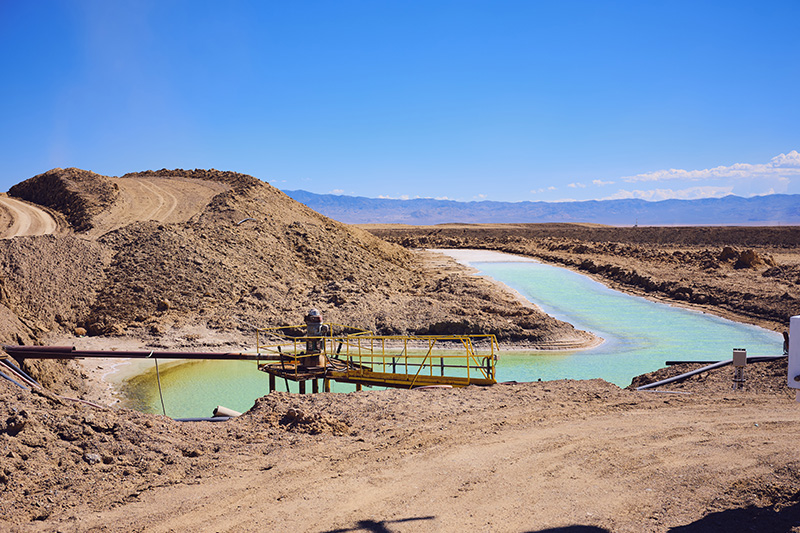
The method uses aluminium hydroxide – which is abundant in the Earth’s crust – as a sorbent for lithium sulphate. It relies on the less stable and more reactive amorphous crystalline polymorph of aluminium hydroxide (Al(OH)3), instead of one of the four highly ordered structures. The researchers say it is cheap, readily available and easy to handle.
The mineral could extract lithium from liquids leached from mining sites, oil fields and used batteries.
The key advantage is that it is said to work in a wider pH range of 5-11 compared with direct extraction methods.
The team reports near-perfect efficiency, capturing 37mg of lithium per 1g of recoverable sorbent from 2g and 20ml of brine solution. They say this is around five times more than a crystalline version of Al(OH)₃ known as gibbsite, previously used for lithium extraction.
ORNL Corporate Fellow Parans Paranthaman remarks that acid-free extraction occurs at 140°C, while usual methods roast mined minerals at 250°C with acid, or 800-1,000°C without.
The powder extracts the lithium ions from a solvent to form a stable, layered, double hydroxide (LDH). Treatment with hot water then causes the LDH to relinquish the ions and regenerate sorbent, which can be reused.
'Lithium, aluminum-layered, double hydroxides react with hot water and leach out the sorbed lithium into the water as lithium salts (delithiation process) and the solid is bayerite,' explain Paranthaman and ORNL Materials Chemist Jayanthi Kumar, who co-led the project.
Their approach was guided by calorimetry measurements, revealing the optimal form of aluminium hydroxide for enhanced extraction efficiency.
By using scanning electron microscopy (SEM) during lithiation, the team has observed how the lithium is adsorbed by the charged neutral layer of aluminium hydroxide with atomic vacancies.
Kumar describes the vacant site as being so small it can only fit cations the size of lithium, and not sodium and potassium.
'SEM provided invaluable insight into the surface morphology of the parent phase both pre- and post-extraction,' note Paranthaman and Kumar. “This enabled us to discern any phase transformations occurring during the extraction process, thereby facilitating a comprehensive understanding of the mechanism at play.'
The first step extracts 86% of the lithium from the leachate or brine, while running it through a second time picks up the rest.
A lifecycle analysis compares the benefits of a circular economy for lithium extraction from waste, to a standard model using sodium carbonate. It concludes this method uses one-third of the material and one-third of the energy.
The team is partnering with a company on large-scale extraction. They want to extract more lithium and regenerate the sorbent to its amorphous form, as it currently changes to a crystalline structure, which is less reactive. The resulting bayerite needs either more time or more concentrated solution to react.
Paranthaman claims less than 2% of lithium for manufacturing is from North America, and this method opens up sources all over the US, from brines to solutions from recycled lithium-ion batteries.
'[The technique has] been tested on brine solution, mineral extracts and battery recycling, and it has shown tremendous performance – preconcentration or purification is needed to improve the selectivity over divalent and trivalent cation impurities present in the feedstock,' conclude Paranthaman and Kumar.