Durable nanoscale metals for fusion reactors
Researchers at Massachusetts Institute of Technology (MIT), USA, have found a way to make structural materials last longer under the harsh conditions inside a fusion reactor.
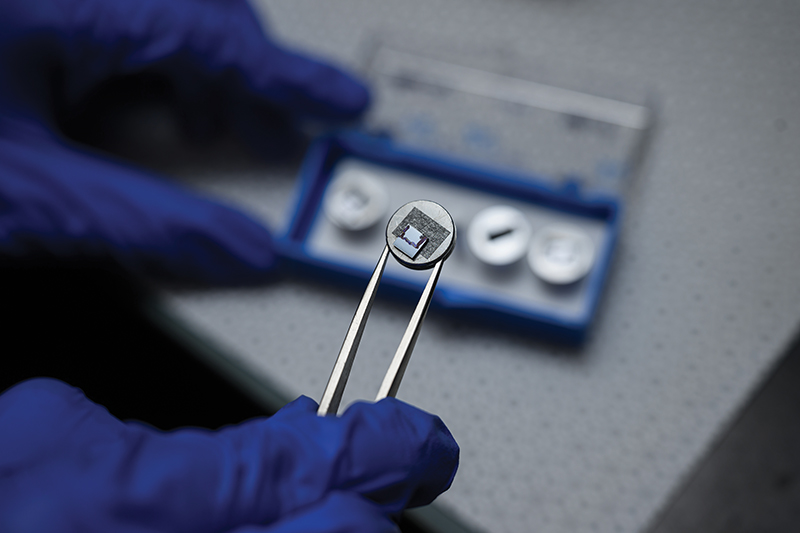
Samples of the iron-silicate composite. The black mark shows where the sample has been subjected to helium implantation
© Gretchen ErtlThey claim to have designed a helium-absorbing iron silicate that prevents the reactor’s vacuum vessel from cracking and failing.
Fusion power reactors rely on superheated plasma reacting inside a vacuum vessel and releasing fast, high kinetic, energy neutrons into a coolant. The transferred heat eventually drives the reactor’s electricity-generating turbine.
However, finding a material durable enough for the vacuum vessel that keeps the plasma and coolant apart, while also allowing the neutrons to pass through the coolant, poses a challenge.
Major structural failures can occur when the fusion neutrons penetrate the vacuum vessel walls and interact with the nuclei of atoms in the structural material, which then gives off particles.
Professor Ju Li at MIT explains how these particles turn into helium atoms that move with low 'embedding energy' for absorption.
These helium atoms instead congregate in the grain boundaries of metals used to construct the vacuum vessels. This is where potentially catastrophic failure can arise, explain the researchers, since the grain boundaries 'form a percolating 2D network'.
As helium atoms repel against other atoms, they initially push open the grain boundary, creating a crack that culminates in the vacuum vessel breaking.
MIT’s solution is to add nanoscale iron silicate (Fe2SiO4) particles to the vessel’s walls, which has a helium-embedding energy below the metal’s grain boundaries. The team’s objectives were two-fold.
First, they had to determine whether the preferential absorption of helium by one phase could offer protection for the other phase and the grain boundary, leaving them almost free of helium. Second, they sought to determine which phases might offer the best helium-absorbing capability.
Starting with the first, 'We prepared titanium aluminide with a minimal amount of tungsten and boron (Ti-48Al-2W-0.08B, at%), which exhibit a nano-lamellar structure consisting of two distinct phases – the γ phase and the α2 phase', explains Li, 'and the helium-embedding energy is 0.5eV lower in the α2 phase, so it should protect the γ phase'.
Once helium ions were implanted at 750°C with an energy of 800keV, they used transmission electron microscopy (TEM) to examine the spatial distribution of helium bubbles. They noted a high density had formed in the α2 phase. In contrast, the density in the γ phase was seven times lower, with no noticeable segregation at the boundary between phases.
Postdoc So Yeon Kim then focused on iron because it is the principal metal found in vacuum walls and identified Fe2SiO4 as a helium-absorbing compound.
It is fabricated by mixing nanoscale particles of silicate (SiO2) with iron powders using ball milling. Placed in a mould, the powder mixture is pressed into a disc and sintered at 800°C to produce Fe2SiO4.
'The energy required to incorporate a helium atom into a phase (i.e. helium embedding energy) can serve as a figure of merit – the lower the energy, the easier it is for a phase to absorb a helium atom,' Kim says.
'In addition, the neutron friendliness of the chemical elements used, the phase stability of the compound, and its mechanical and adhesion strengths to the metal matrix are also important considerations.'
The team proposed that the ‘atomic-scale free volume’ could provide an indicator of low helium-embedding energy.
After implanting helium in a Fe-Fe2SiO4 composite and using X-ray diffraction, the TEM images show a significant reduction in diameter and number density by more than 20% and 50%, respectively, say the researchers.
And adding only 1vol.% of Fe-Fe2SiO4 to the vacuum’s vessel is reported to achieve the required reduction in helium bubbles. 'The amount of helium we need to sequester is 0.1-0.2 atomic % in steels, assuming operation over 10 years,' says Kim.
'Therefore, we need one iron silicate per thousand iron atoms, which corresponds to 0.6-1.2vol.% of iron silicate in the steel composite.'