Doubling down on 3D printing
Chemists and material scientists at Sandia National Laboratories, USA, have developed a process for printing non-metallic materials that they allege is five times faster than traditional 3D printing.
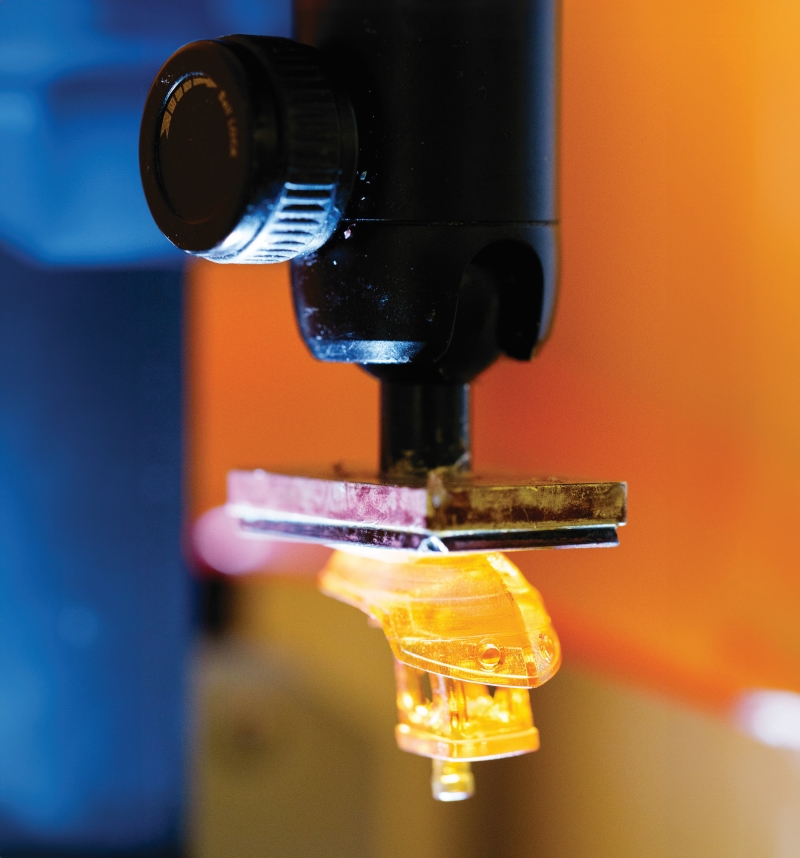
The approach, called selective, dual-wavelength, olefin, metathesis 3D printing (SWOMP), uses ultraviolet (UV) and blue light.
Conventional vat printing irradiates a vat of photosensitive liquid resin in a desired pattern. Light beneath the vat cures and hardens the resin into a polymer layer, which is lifted, and a new pattern is projected beneath to cure subsequent layers.
However, the polymer can adhere to the previous layer and to the bottom of the vat as it cures. After each layer cures, the polymer must be slowly peeled from the vat to prevent damage, significantly slowing the 3D printing process.
Materials Scientist Samuel Leguizamon explains that the cured polymer might break off the build head and damage the print during delamination, which can cause print failure.
'Conventional vat printing uses a very slow lift speed between layers to prevent damage/failure. By removing the interface between cured polymer and vat bottom, we prevent any potential damage and allow for rapid printing.'
The team was inspired by continuous liquid interface printing, along with an approach that uses dual-wavelength light for acrylic-based polymerisations.
While it still prints in layers, a second light wavelength prevents polymerisation at the bottom of the vat, allowing it to be lifted more quickly and speeding printing up to 18cm/h.
The UV light activates an inhibiting chemical to prevent polymerisation, which is irradiated in a shallow layer across the entire vat to prevent adhesion. The blue light activates only the initiator and only allows for polymerisation, so it is shone and patterned as required to create a part. It is also used at higher intensities to penetrate just beyond the blanket UV light layer to cure above the inhibited interface.
To make 3D-printed materials stronger and more versatile, the team tried dicyclopentadiene, commonly used to make paints, varnishes and flame retardants for plastics, instead of acrylic-based materials.
Leguizamon says, 'We have a patented formulation that took use of photosensitisers to rapidly initiate polymerisation and allow for the use of visible light irradiation. Poly(dicyclopentadiene) is already a commercially relevant polymer used in a variety of industries with a large global market.'
He knows of only one company to have commercialised it for 3D printing and notes it has conventionally needed reaction injection moulding, which has limited the geometries and applications.
Their current prototype has a light engine modified with a blue LED to pattern light and a separate UV lamp to inhibit polymerisation. They use a dichroic mirror to project both wavelengths from two light sources into a single vat. While it is made of multiple parts, they are open to developing a commercially viable system.
They are still studying the range of materials that can be used with the process, but are developing polyethylene-like materials and other high-performance materials for locations where machinery and parts are not readily available, such as space or at military bases.