Digital solutions for greater circularity?
Dr Ryan Nolan of the University of Exeter, UK, shares insights from a new report on how manufacturing can prepare for a digital future.
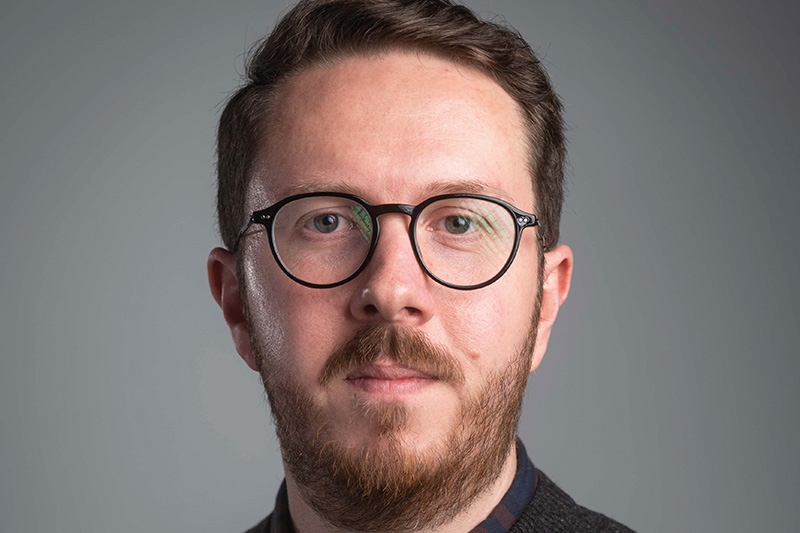
The potential for digital technologies to reduce carbon emissions in manufacturing is staggering. Existing tools such as the industrial Internet of Things (IoT), machine learning and smart sensors that monitor component performance and condition are predicted to contribute almost one-third of the required reductions by 2030.
One area where these technologies can have a significant impact is in supporting and enhancing a circular economy. Many materials can only be used for a limited time before they become useless or harmful. This is a big problem for manufacturers who want to make products that last longer and use fewer resources.
Through regenerating the natural world, reducing the need for virgin materials, and reusing and recovering resources to avoid waste, a circular economy represents a critical pathway to achieving net-zero in manufacturing and beyond.
The recently published Digital World 2050 report is the result of a six-year study from the Connected Everything Network, funded by the UK Engineering and Physical Sciences Research Council. The report, co-authored by researchers from the Universities of Exeter, Nottingham, Liverpool and Cambridge, UK, finds that a digitally enabled circular economy can be a key enabler to better material circularity in the future and support net-zero targets.
For example, adding digital tags or markers to materials can tell manufacturers how to reuse, recycle, or restore the highest possible value to materials for as long as possible.
The report challenges traditional assumptions that waste is unavoidable through the concept of zero-waste manufacturing. While it may be the case that waste is undesirable, by viewing it as an under-utilised, recoverable resource, we can begin to think differently about our relationship with it, as well as its function in the economy. This is one of the key principles underlying the concept of the circular economy.
Really, it is less about avoiding waste and more about retaining value through circulating materials and extending their useful lifespan through reuse, repair and remanufacturing.
There has been increasing support for adopting a circular economy as a means to reach net-zero targets, including in the Independent Review of Net Zero, commissioned by the UK Government and published in January 2023. Among other things, it recommends the establishment of a circular economy taskforce to monitor ambitious plans for decarbonisation.
As such, it is the perfect time to onboard solutions enhanced by currently available technologies.
Digital technology such as IoT – systems of internet-connected devices that communicate and share data – can support the shift from linear to more circular modes of operation.
IoT platforms that enable product tracking throughout supply chains can incentivise zero waste by rewarding sustainable product designs, utilisation and management.
Providing organisations with deeper knowledge of their operations is beneficial to their own day-to-day activities, and these technologies also help manufacturing (and other sectors) become more transparent in their processes across supply chains as they try to meet environmental and sustainability goals.
Transparency is increasingly important for consumer confidence and providing assurances against claims of ‘greenwashing’.
The challenge
For a long time, business as usual has been about moving wastes out of industrial processes and into waste management bodies. Manufacturers face a challenge in that materials are not infinitely reusable or recyclable.
To maintain the highest possible value for as long as possible, manufacturers need information on the critical materials, products or components they recover. Meanwhile, repair technicians may not have access to disassembly guidelines for electrical equipment, and plastic recyclers may not have full knowledge of the chemical make-up of the materials they process, including the presence of toxic substances.
To maintain a product’s value in the economy for as long as possible, information on its design, composition and condition is therefore critical. Information is key, and this is what digital technology brings to the equation.
Manufacturers must also radically alter their business models if they are to address grand challenges around climate change, poverty reduction, food security, biodiversity, sustainable consumption, and equality. In many cases, the complex realities of these challenges are forcing the transition.
Advocates of the circular economy maintain the importance of stretching beyond reverse logistics such as reuse and recycling to actively regenerate natural resources. Circular or ‘regenerative’ business models aim to deliver meaningful net-positive environmental and social value, rectifying the environmental and societal damage caused over the past decades of manufacturing that has been driven by the economic bottom line. Naturally, this presents many challenges to the manufacturing sector as well as exciting opportunities for innovation.
Tackling complex social and environmental symptoms
of our existing economy requires system-level innovation, and in line with circular business models, manufacturers need to take a holistic approach that uses digital technologies to consider every stage of their value chain – from sourcing raw materials to designing products that can be easily maintained, upgraded and reused.
The success of such transformative change lies in successful collaboration. The revolutionary potential of digital solutions has been slower to materialise in manufacturing than some might have expected, but this is partly due to an absence of connected thinking between manufacturers and those producing digital tools.
The adverse effects of this are solutions that are either not quite right or that are too advanced for current capabilities in the sector. It is therefore vital that solutions are proposed to bridge this divide and create spaces for knowledge transfer.
Of course, to realise the full potential of a digitally enhanced circular economy in the manufacturing sector, timely collective action from stakeholders, such as governments, key industry partners and funders, is required across a range of issues.
Recommendations
The Digital World 2050 report presents a vision of how digital technologies can enable circular manufacturing in the UK and beyond. The report outlines five key recommendations that aim to support the transition to a more sustainable and resilient manufacturing sector.
The report also showcases some examples of digital circular solutions that illustrate the potential benefits and challenges of this approach. As advocates for a more circular economy enhanced by digital solutions, the authors of the report call for more collaboration and innovation among stakeholders in the sector to create a positive impact for society, economy and environment.
As a result of research carried out for the report – which included roundtables with industry experts, a review of grey literature, and building case studies – more than 25 recommendations surfaced, all of which address important issues that need to be taken seriously in the pursuit of a smarter and more circular manufacturing sector.
However, in the interest of simplifying a vastly complex picture, the report concludes with five strong and consistent recommendations that cut across the themes, including:
- Connecting digital technology developers to manufacturers – for digital solutions to land in the sector and truly contribute to its development, the technologies developed must be relevant to manufacturers. This seems an obvious point, but the slower-than-expected adoption of certain tools in the sector is in part a result of a disconnect between knowledge of what is required now and what might be required when collaborations and capabilities have matured.
- Reducing digital manufacturing knowledge barriers – if manufacturing is to become a smarter, more agile sector, it is important that new tools and solutions are as simple as possible to implement. Thanks to platforms and visual interfaces that remove the need for deep technical know-how, it is now simpler for more of us to create powerful applications and programmes. This logic must be adopted in the roll-out of new technologies to ensure smooth and timely adoption and scaling.
- Consolidating digital manufacturing guidance – the internet is a powerful source of information, but the knowledge landscape can be a fragmented environment and the best sources can be difficult to identify. This makes it more difficult for manufacturers interested in digital tools to access clear, up-to-date guidance on best practice. We need to highlight initiatives such as the Knowledge Transfer Network, and make sure good quality sources are appropriately signposted, to support manufacturers in accessing the knowledge they need at the point of requirement.
- Supporting employee wellbeing during the transition – digital solutions may pave the road to a cleaner, more circular future for manufacturing, but the people working across supply chains must be brought along for the ride. In the face of potential anxiety and uncertainty among employees that can be reasonably expected with the introduction of cutting-edge digital tools, employers must consistently communicate and train the workforce so that employees can be confident in their roles. This is about futureproofing the technical dimension of the sector, while producing teams of digital advocates who will move forward with new skills and capabilities.
- Promoting transparency of value chain data – a digitally enhanced circular economy for manufacturing will produce a lot of data, and a lot of valuable data that can be leveraged to inform the transformation of other sectors and industries. Therefore, it is vital that information is shared as widely as possible. Transparency around the value chain data could contribute to scaling circular economy practices across sectors, but it is a huge task that requires a decisive break from practices typically employed in the linear economy in both the private and public sectors. Support is required for manufacturers willing to open their data for the future of the sector.