Decarbonising glass production
Can glass production be more sustainable?
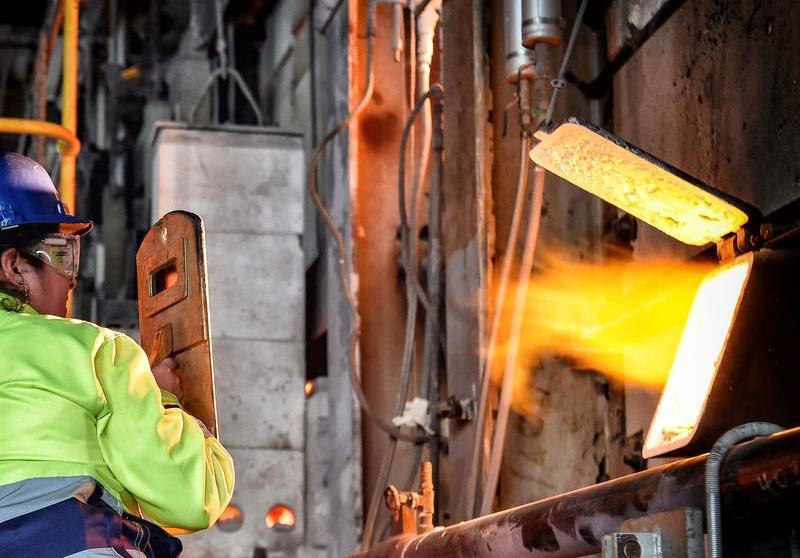
It is hard to imagine a world without glass. Glass materials underpin all aspects of our lives. Not only in common applications such as bottles and glazing, but also in a host of other applications ranging from reflective glass microspheres for road markings, flakes that improve corrosion resistance of paints, fibre optic cables to transmit data and even surgical materials to help bones heal.
Glass is also essential in many of the technologies that will enable a more sustainable society, such as the generation of renewable energy. It provides the transparent, impermeable barrier for photovoltaic solar cells and strengthens wind turbine blades.
Glass wool is used to insulate our roofs and walls, while modern glazing systems can significantly reduce the amount of energy required to heat and cool our buildings (thanks to complex nanometre-thick coatings on the glass surface that reflect infrared light but transmit visible light).
However, one of the main challenges associated with manufacturing glass is that the raw materials need to be heated to high temperatures to melt them – typically above 1,500°C. This requires a lot of energy, often from the combustion of natural gas.
British Glass’ net-zero strategy states that the mainstream UK glass industry produces around 3.5Mt of glass per annum, generating more than 1.5Mt of CO2. This is approximately 1% of total UK emissions. Of these emissions, 75-85% are from fuel combustion and 15-25% are from the raw materials, depending on the amount of recycled glass used.
Over the past 40 years, the glass industry has seen a 50% increase in the energy efficiency of the UK’s glass furnaces. This has been achieved through improvements in furnace designs, better process control and increased amounts of recycled glass used to make new glass products (reducing furnace energy requirements as well as the need for virgin raw materials).
According to a recent lifecycle analysis by the European Container Glass Federation, a tonne of recycled glass could save 670kg of CO2 by reducing melting energy and process emissions.
However, the rate of reduction in CO2 emissions per tonne of glass produced has fallen over recent years as the industry gets closer to the theoretical minimum energy required to manufacture glass using conventional technologies. As such, new approaches to manufacturing glass are required if the industry is to achieve its net-zero targets by 2050.
While many technologies and concepts have been identified and tested at lab-scale that might help decarbonise the glass industry, we must overcome several barriers for them to be widely adopted within commercial plants.
Hot stuff
A typical glass manufacturing site will have only one or two furnaces, each with a typical output of between 400-900t of glass per day and costing upwards of £40mln to replace.
Operating at temperatures above 1,500°C, these furnaces can hold more than 2,000t of molten glass and are expected to operate continuously for between 15-20 years without being cooled down.
Glass manufacturers are understandably cautious about trialling any new technology that might affect the consistency of their production processes, especially the furnace, where it can take several days for contamination to be washed through the glass tank. Worse still, such contaminants could even risk damaging the furnace refractories and drastically reduce the furnace life.
Industrial trials can also be expensive. Large multinational manufacturers can only afford to invest in R&D on a few large-scale developments, and this knowledge certainly won’t be shared with competitors.
So, despite the glass industry coming under increasing pressure from its supply chain to decarbonise its operations, or face losing out to other materials such as plastic and aluminium, the industry is struggling to develop the new technologies it needs.
In response to these pressures, the industry, led by British Glass, acknowledged that the only way for the industry to decarbonise by 2050 is if a new, unified approach is adopted.
Manufacturers from across the world and various sectors within the industry – container, float, fibre, tableware, pharmaceutical and speciality – would need to join forces with materials suppliers, equipment developers and customers (such as mainstream brands like Diageo, Heineken and Velux), and academia to pool their respective resources. This would help identify, develop, de-risk and deploy the new and innovative technologies needed. It is out of this vision that Glass Futures was born.
Securing the future
Recruiting its first full-time employees just over four years ago, Glass Futures opened its new £54mln research facility in St Helens, UK, last June, and is due to commission a globally unique 30t/d glass pilot furnace towards the end of 2024. This will be equipped with a host of capabilities to investigate a wide range of new technologies that are capable of decarbonising the glass sector.
As a not-for-profit membership organisation, Glass Futures has already attracted more than 42 members, including glass manufacturers from all sectors of the industry that collectively operate more than 300 glass furnaces, plus suppliers, global brands, industry bodies and several universities.
Glass Futures is also working closely with government bodies such as UK Research and Innovation and the Department for Energy Security and Net Zero (DESNZ), helping to secure more than £100mln of grant funding over the last five years for its members and partners.
A number of key research areas have been identified to focus efforts to decarbonise the sector.
Low-carbon fuels
More than 80% of the energy required to manufacture glass is used within the ‘hot-end’ of the process, where the raw materials are melted to the point at which they can be formed into the final product. Identifying low-carbon fuels that can replace natural gas provides the greatest opportunity to reduce emissions.
Electric melting, whereby electricity is passed between electrodes within the molten glass (that is electrically conductive at high temperatures), offers the most efficient route to heat the furnace. Although electric furnaces have been in use for several decades, 100% electric melting technologies are currently limited to furnaces of up to 250t/d.
A new furnace in Germany, operated by Ardagh Group, is now exploring up to 80% ‘electric boost’. There is a lot of work required to understand how to maximise the amount of electric melting in a standard furnace.
Glass Futures’ furnace will explore electric boost designs. Work with industry partners will examine how a glass furnace fitted with electric-boost capability can help balance the load on the local electricity grid, using more electricity when supply is high and demand low (e.g. on a windy, sunny day), then switching to other renewable fuels when demand for electricity is high.
The pilot furnace will also be equipped to assess hydrogen fuels, including the full range of blends with natural gas, from 0-100%.
Trials by Pilkington UK in 2021, on a single port, demonstrated that effective melting can be achieved with 100% hydrogen flames. Extended trials with 15% hydrogen by volume blended with the natural gas on the whole furnace showed minimal impact. Firing 100% hydrogen increases the moisture level in the atmosphere which can adversely affect melt properties. The impact of firing hydrogen on the furnace refractories is being investigated.
At Pilkington, we saw a relatively modest increase of 20% in the NOx emissions. As such, there are plans to investigate the best operational configurations for hydrogen use – both within the furnace and across other parts of the manufacturing process, such as the channel taking the glass from the furnace to the forming sections (the forehearth).
Biofuels also offer a route to replace natural gas, particularly those derived from waste streams such as from biodiesel manufacturing, or from agri-residues. These by-products can be converted to liquid or gaseous fuels through pyrolysis, gasification or anaerobic digestion.
Before the 1970s, glass furnaces were typically fired on heavy fuel oils, and so modern glass furnaces can be converted to run on biofuels with minimal modifications to the infrastructure and therefore with relatively little additional investment.
Over the last three years, Glass Futures has undertaken a number of trials demonstrating the viability of a range of biofuels, both on a large-scale combustion rig and at industrial scale. Current projects seek to identify more affordable biofuels, with a strong emphasis on sustainability and avoiding any unintended consequences for the environment or communities that are local to their sources. Collaboration with the UK-based Supergen Bioenergy Hub will help to build this understanding.
Also, biofuels are of particular interest in regions of the globe that are unlikely to have access to significant and reliable supplies of renewable electricity or green hydrogen by 2050.
In Africa and South America there are also significant volumes of agri-residues that can often pollute the air if burnt, or local waterways if dumped in fields. Glass Futures is currently working with partners in Nigeria to explore how sustainable biofuel supply chains might be established in these regions, using fuels produced from waste agri-residues to supply local glass plants.
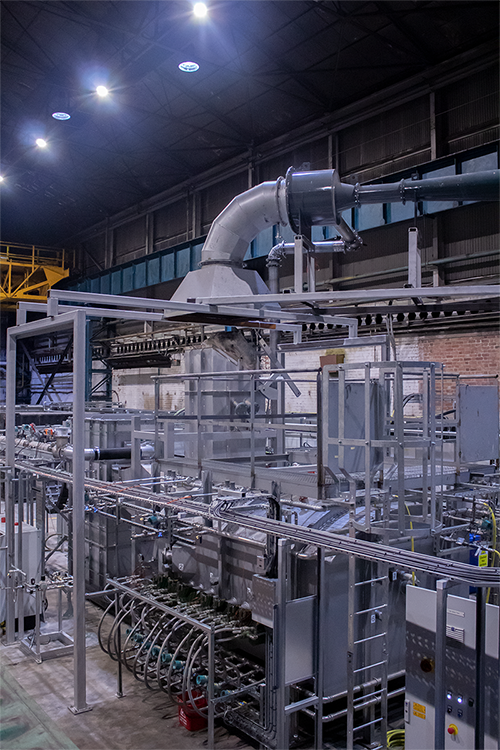
Carbon capture
If carbon emissions can be captured, then by also using biofuels, the glass sector could sequester more CO2 than it emits.
A project to undertake Europe’s first carbon capture trial in the flat glass industry is underway with C-Capture Ltd and Pilkington UK. It has received £1.7mln of funding from DESNZ’s Net Zero Innovation Portfolio, and is part of the £20mln CCUS Innovation 2.0 programme, aimed at accelerating next-generation carbon capture, utilisation and storage (CCUS) technology in the UK. Additional private sector contributions support a £2.7mln total for this multi-industry project.
The C-Capture technology will be moved to the Glass Futures pilot facility later this year to assess performance for a series of future furnace scenarios, such as hydrogen firing.
Many manufacturers are looking to transition towards oxy-fuel furnace technology, whereby pure oxygen (potentially using the oxygen produced during electrolytic hydrogen production) is fed directly into the glass furnace with the fuel. This can be up to 30% more efficient than a conventional furnace drawing air through large regenerators and reduces NOx emissions.
Alongside burning biofuels, it could offer a lower-cost route to capturing the CO2. Most of the emissions will consist of H2O and CO2, which should mean it is more straightforward to separate, compress and capture the CO2 – as opposed to exhaust streams with lower CO2 concentrations. There are plans to assess this through oxy-biofuel trials later this year.
As well as capturing CO2, the glass sector also needs to identify solutions for transporting it to be used or sequestered. The COREu project is a €30mln Horizon Europe project, funded by the European Union and led by Norwegian research institute SINTEF – in which Glass Futures is a project partner. The programme is looking to develop and demonstrate the full CCUS supply chain.
Waste heat recovery
The industry has already adopted several waste heat recovery technologies, from Organic Rankine Cycle systems to generate electricity, to regenerators that preheat incoming gases and systems using hot waste gases to preheat raw materials. Other glass plants have provided heat to local district heat networks.
Work is underway to explore how waste heat might drive other industrial processes that require high temperatures. Projects include a novel carbon nanotube fibre product under development by Q-Flo, UK, and a system built by Pilkington UK, to convert waste plastic into fuels to power the glass furnace, as well as opportunities to use waste heat to generate low-carbon hydrogen.
New and recycled content
Glass Futures’ new pilot line will also provide a valuable platform to trial new raw materials and glass compositions with potential to reduce process CO2 emissions, melting rates and furnace temperatures.
Opportunities for increasing the proportion of recycled materials fed into the furnace will also be investigated, alongside how by-products and wastes from other sectors may be used.
For example glass manufacturers currently use a material produced from steel blast-furnace slag – Calumite – as a replacement for the limestone, sand and other additives used.
However, the availability of Calumite is likely to decrease as the steel industry transitions away from blast furnaces so other such by-products are needed. This will need extensive trials to understand the impact on the glass chemistry and melting dynamics.
Improved process control
Current glass manufacturing processes are often controlled manually so there is significant scope to improve process control. For example, furnaces are often operated above the minimum required temperature to provide a process ‘cushion’ to avoid defects such as un-melted batch materials, or small bubbles (‘seeds’) that can result from insufficient refining or poor convection flows as the molten glass passes through the furnace.
Improved process control, sensors and furnace modelling can help understand how the glass melts and flows through the furnace and, in turn, identify how to minimise the energy used in furnaces to produce the final glass product.
Once formed, the glass product has to be cooled down from ~800°C in a controlled manner, over several minutes, to remove internal stress within the structure. This is necessary to avoid catastrophic product failure when in service, but takes 40-60 minutes after forming. Often defects are only detected after the glass has been annealed and so can lead to significant quantities of defective products being produced before the problem is identified and rectified.
Improved sensors and control systems will help identify defects earlier, and ideally spot trends when the process is deviating so that it can be fixed before defects are created. The new pilot line will provide a valuable test bed on which to trial such technologies.
The facility will be fitted with Siemens’ SIMATIC PCS neo control system to compile data from across the pilot line onto one central system – unlike conventional glass plants that have standalone control systems for each part of the production process. The system will also mean the plant can be analysed remotely in real-time.
Collaborating with Foundation Industries
The UK glass industry shares many of the same challenges as other Foundation Industries (FIs), such as metals, cement, ceramics, chemicals and paper. Over the last four years, Glass Futures has collaborated with partners from other FIs in 17 projects, including some of the first hydrogen-firing trials of commercial ceramics and steel products, to assess the impact on product quality and furnace emissions.
Glass Futures helped form the Foundation Industries Sustainability Consortium (FISC), partnering with the CPI, Lucideon, the Materials Processing Institute and the Henry Royce Institute.
So far, FISC partners have received £38mln in funding to develop technologies that can improve the sustainability of processes across the FIs, with research focused around alternative fuels; circular economy, feedstock, recycling and reuse; digital control and sensors; process optimisation and sustainable materials development.
The consortium is working closely with FI sector partners to develop future cross-sector research programmes.
The challenge to decarbonise the glass industry is formidable, nonetheless Glass Futures offers a route to achieve a net-zero industry that is sustainable and actively reduces CO2 levels in the atmosphere, and an industry that supports training and employment for the people that live and work in the surrounding regions.
This is only the first step in the net-zero journey. Even though the current glass pilot line is still under construction, the team is already considering what future furnace designs might look like, and even how future glass manufacturing plants might be integrated into wider manufacturing clusters, local towns and cities to create a sustainable manufacturing sector and society.