Cork-based waterproof coating for fibre food packaging
The cork of oak and beech trees is being used to produce a multifunctional coating for fibre-based food packaging.
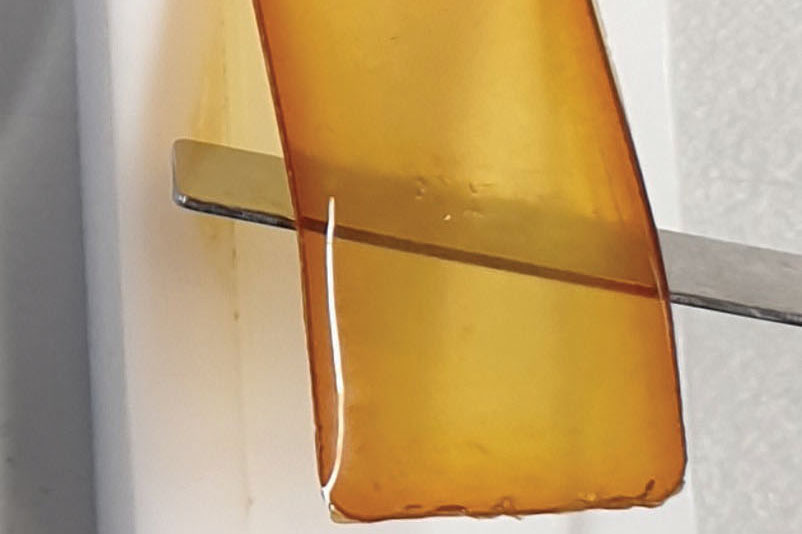
The coating is being made for products such as baked goods and dry fruits where water-vapour resistance is a high priority.
Partners in the BioBarrier4Fiber project, hosted at the Fraunhofer Institute for Process Engineering and Packaging IVV, say the coating is processable, sealable, highly flexible and an effective water vapour barrier.
Fibre-based substrates are conventionally coated with protective layers against gas and moisture permeation with fossil-based polymers that hinder recyclability, like polyethylene and ethylene vinyl alcohol.
Current bio-based approaches use renewable polymers such as polysaccharides, proteins and waxes as a barrier for water vapour or oxygen. The team is unaware of a bio-based material that combines all these attributes.
Their coating consists of suberin fatty acids (SFAs) from the cork of oak and beech trees. Trees use suberin as a natural protective barrier to control water in and out of cell walls.
Project coordinator and researcher Lorenzo Tomei says, 'SFAs are fascinating materials with a complex chemical structure. They are the backbone of the biopolymer suberin, which plays an essential role in tree plant physiology.' They were chosen for the highly functional, polymerisable, aliphatic acids of variable length and structure.
Oak and beech trees are a common European species used for commercial products such as wine corks, barrels, timber and plywood, which generate a large amount of waste, notes Tomei. He cites estimates from trade association Deutscher Holzwirtschaft e.V. that around 1.4mln m3 of debarked oak and beech logs are produced annually in Germany.
If the outer bark is ~5% of the tree’s total dry mass, 74,000m3 of bark is discarded in Germany each year, he highlights.
Some species, such as the cork oak grown for wine corks, have significant amounts of suberin – which can be 50% of the dry mass. 'Such a high content makes it quite interesting for extraction,' Tomei says.
A pre-treatment homogenises the bark for controllable extractions, before extractive depolymerisation. Finally, they separate the molecules from the residual biomass and recover the SFAs.
By accurately selecting parameters, such as catalyst content and extraction solvent, they can control both quantitative yields and the quality of extracted materials. The goal is to obtain the suberin building blocks, so they have the greatest freedom in the subsequent formulation in coating materials. The team aims to select bio-based materials for solvents and additives if possible.
Tomei shares, 'Most of our development efforts have gone into testing many different process conditions and seeing how the performance…is affected. We have now made more than 90 different extracts only to understand this very crucial step in the process.'
The coating is designed to be a barrier throughout the product’s lifecycle, ensuring quality and extending shelf life. The project, which runs to May 2025, includes storage trials in real-world conditions with food samples.
Due to their complexity, the project will not focus on liquid packaged products, vacuum packaging, or recyclability – but Tomei notes, these may be considered as a follow-up.
The team says scaling will require many industry partners, including forestry companies for sourcing raw materials, biorefineries and chemical industries for extracting and making suberin intermediates, and coating and packaging manufacturers for turning materials into end-user products.