Cold welding aluminium and copper to improve EV range
Cold welding to make aluminium-copper hybrid conductors could help reduce electric vehicle (EV) weight.
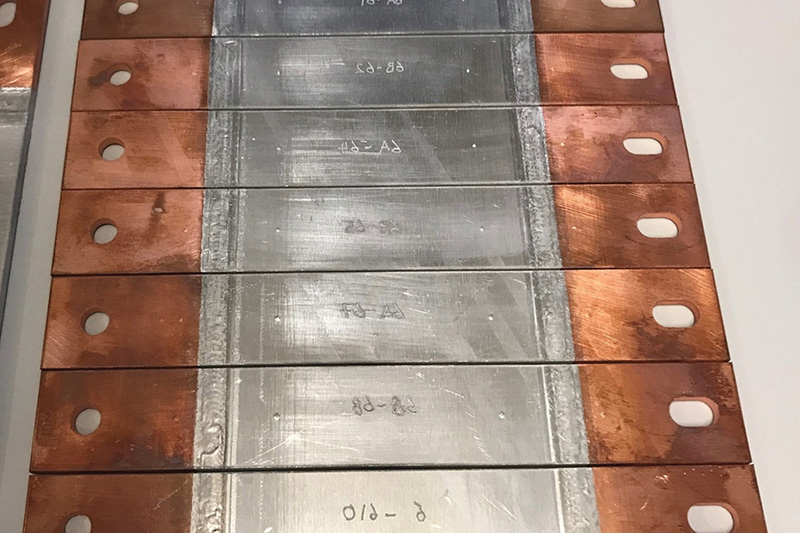
Replacing some of the copper in these conductors makes EVs lighter and more energy efficient, says a team at the Norwegian University of Science and Technology (NTNU).
They suggest cold welding can harness both metals’ properties without compromising conductivity.
During the welding process, aluminium and copper are mixed together at the atomic level on the contact surface, and usually the higher the temperature, the better they mix. However, brittle crystals, known as intermetallic phases, often form and these have poorer conductivity than the pure metals.
To stop brittle crystals forming, they have invented the Hybrid Metal Extrusion and Bonding (HYB) technique.
PhD research fellow Jørgen A Sørhaug at NTNU describes it as very similar to friction stir welding, which uses frictional heat from a rotating tool to join materials.
HYB also uses a rotating pin but it performs continuous extrusion of a filler metal – in this case, an aluminium alloy with high concentrations of silicon and magnesium.
The continuous extrusion is achieved through the pin’s rotational movement in a rigid housing. This pulls the wire through an extrusion chamber above the pin, before it goes through some dies that are part of the pin.
'This duality is beneficial,' Sørhaug says, 'as the extruded metal can fill any gaps – intended or not – between the profiles being joined.'
The welds were then analysed using precision electron diffraction, high-resolution transmission electron microscopy, and X-ray analysis.
The researchers conclude that HYB is better suited for joining aluminium and copper than other welding methods because of the thinner and slower-growing intermetallic layers at the interface between the metals, which helps prevent the mechanical and electrical properties of these conductors from changing.
Sørhaug adds, 'We want to control both the heat input and the material deformation to control the amount of intermetallic phases.'
The aluminium-copper conductors made have a ratio of about 50:50, resulting in a weight reduction compared with just copper conductors of ~35%, says Sørhaug. He thinks the potential weight reduction could be as high as 50%.
As aluminium is mechanically weaker than copper, the group says more research is needed before it can replace copper.
They suggest making an aluminium alloy with other elements and thermomechanically treating it could increase strength.
'But aluminium alloys are often sensitive to high temperatures, and their strength will generally be weakened by welding. We have therefore also investigated what causes this strength reduction at the atomic level and how we can improve the alloys to better withstand heat,' says Sørhaug.
NTNU will continue researching cold welding of aluminium and copper in a new project with SINTEF. The aim is to better control the temperature and tailor plastic deformation at the nanoscale.
Sørhaug would also like to further investigate the effects of magnesium, silicon and copper in the aluminium part, and how that influences the conductors’ strength and electrical conductivity. As well as the effect of alloying elements on the weld’s interface properties.
Sørhaug postulates that, as EVs have 30-80kg of copper wiring and a car is ~2,150kg, copper makes up 1.5-4.5% of the weight. He estimates the total weight reduction from using aluminium-copper hybrid wires to be about 1-3%, but the biggest appeal for industry, he notes, is the cost reduction.
The HYB technology is now at Sintef Manufacturing in Raufoss, where Sørhaug is investigating whether it can be integrated with an industrial friction stir welding machine.