Clear fission
The past, present and future materials challenges in the nuclear industry.
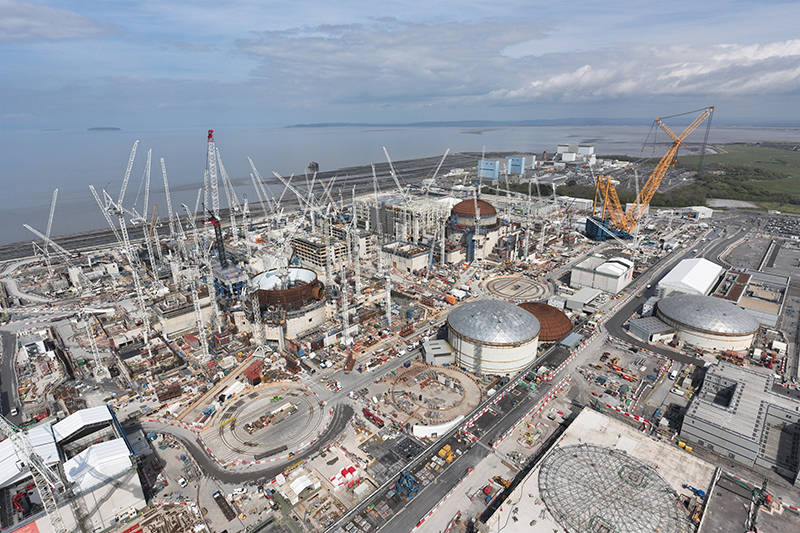
According to the World Nuclear Association, about one tenth of the worldwide energy mix is provided by nuclear fission power stations. This equates to 15% in the UK, reports the British Energy Security Strategy (around 5.9GWe).
It is anticipated this will increase to 25% of the UK’s energy mix through deployment of up to 24GWe of new nuclear capacity, providing a low-carbon baseload supply.
The simplest functions of a nuclear reactor are to:
- Sustain a chain reaction
- Attain the greatest burn-up from the nuclear fuel
- Ensure that heat is removed from the fuel in an efficient way (i.e. extraction of heat at high temperature)
Most reactors worldwide are water-based. They work by removing heat from nuclear fuel by coolant water. Depending on the reactor type, this may directly drive a steam turbine (e.g. boiling water reactor) or be used to heat a secondary coolant circuit (e.g. pressurised water reactor (PWR), water-water energetic reactor (VVER), or pressurised heavy water reactor (PHWR)).
For steam generator components, PWRs use nickel base alloys (NBAs) (Alloys 600 and 690), VVERs use stainless steel and PHWRs use NBAs (Monel 400, Alloy 600) or iron-nickel-chromium material (Alloy 800).
For the majority of operating power reactors, uranium oxide (UO2) fuel is used at low enrichment. Fuel enrichment is used to increase the amount of the main fissile isotope – uranium-235 – from a naturally occuring 0.7% to 5.0%.
The UK civil nuclear fleet has historically comprised CO2 gas-cooled reactors, many of which are now in various stages of decommissioning. Alongside the remaining operational advanced gas-cooled reactors (AGRs), the UK has a single reactor unit PWR at Sizewell B.
This is to be joined by Hinkley Point C (HPC), another dual unit PWR, which is expected to start operation in the next decade. A nuclear site licence has now also been issued for a dual unit PWR at Sizewell C (SZC) for a similar design to that being constructed at HPC.
It is expected that costs for the SZC plant will be lower thanks to operational experience with the design and build at HPC. These modern units at HPC and SZC are considered large-scale nuclear plants, with capacities of 3,200MW, each sufficient to provide electricity to six million homes.
Yet, while there are many advantages of nuclear power, challenges exist – one of which is materials degradation.
Pushed to the limits
Nuclear fuels must tolerate relatively high-thermal gradients over short distances. The pellet centre can be greater than 1,200°C, whereas the periphery might only be 400°C – a dramatic change over just 10mm.
Such gradients can lead to cracks forming within the fuel. As burn-up increases, nuclear fission leads to fission products. Xenon and krypton gases are generated from uranium and plutonium, which have a low solubility in the fuel.
The gases migrate from the matrix to grain boundaries, to locations of porosity, with cracking exacerbating this issue.
Fission gas bubbles may also be created within the matrix and at grain boundaries, and eventually – once a route is accessible – these gases can migrate to the gas space between the clad and fuel – the plenum.
These gases also have a much poorer thermal conductivity compared with helium fill gas, leading to a rise in fuel temperature and a decrease in thermal conductivity of the plenum gas.
Swelling of the fuel pellets can occur. Here, the pellet-clad gap narrows until there is a pellet-clad interaction, leading to stresses being imposed on the interior clad wall. This can lead to cladding failure in combination with the production of iodine – another fission gas – which may cause internal iodine stress corrosion cracking.
Stress corrosion cracking (SCC) is a type of environmentally assisted cracking (EAC), which can occur when three main conditions are met, as depicted in the Venn diagram below.
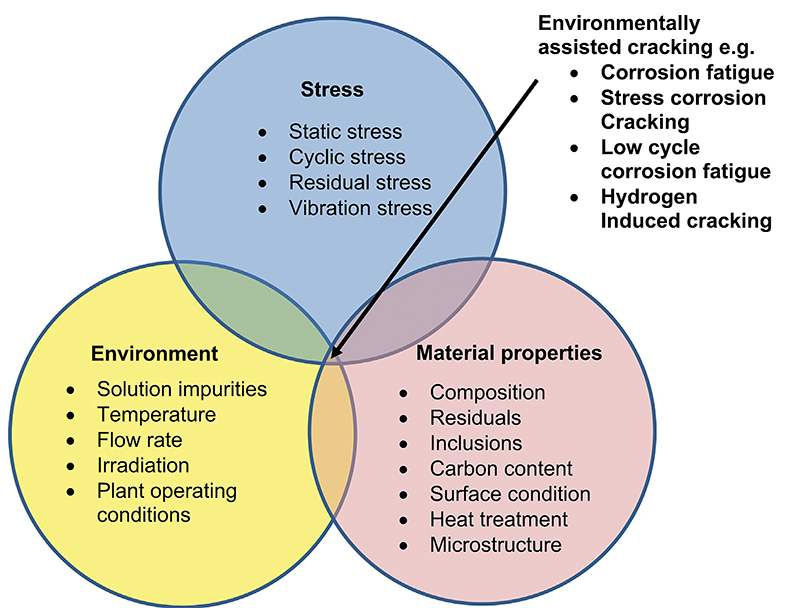
Venn diagram showing the main variables affecting environmentally assisted cracking
© Adapted from Clark et al., (2020) Nanometre to micrometre length-scale techniques for characterising environmentally-assisted cracking: An appraisal. Heliyon. 6(3) doi.org/10.1016/j.heliyon.2020.e03448. creativecommons.org/licenses/by/4.0/Reactor coolant water chemistry is tightly controlled, with typical corrosive anions such as chlorides or sulphates kept to low values of <150µg·L-1. Oxygen too is another PWR control parameter and typically reduced to below 5ppb.
Despite these controls, there are regions within the coolant circuit where impurities concentrate – or where oxygen accumulates – such as in dead legs, regions of little flow or crevices. This can be compounded by radiation, which results in a change in solution chemistry through radiolysis and leads to stable oxidising species forming such as oxygen and hydrogen peroxide.
Depending on the material in question, radiation can also lead to a change in the microstructure itself, which can include radiation hardening or even grain boundary microchemistry changes, making the material less resistant to EAC.
Susceptible materials, such as those that may have been heavily cold worked or sensitised during the manufacturing stage, may then undergo EAC initiation and propagation (see image below).
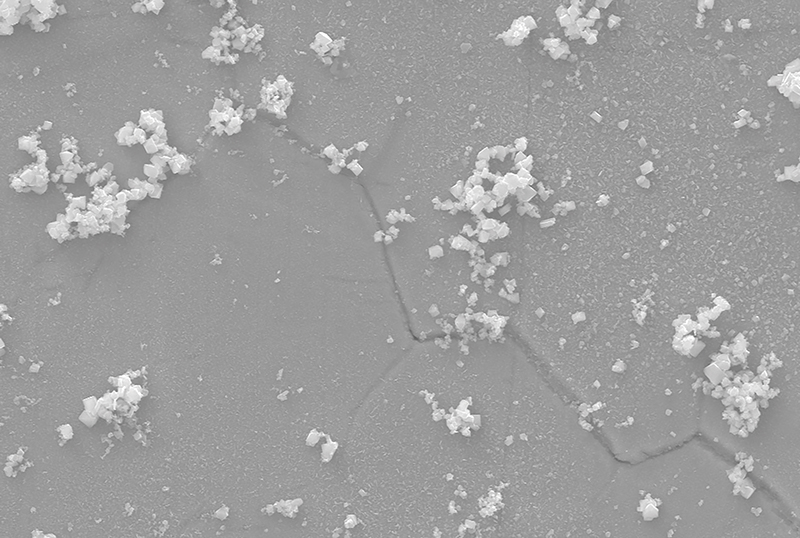
Over time, materials and jointing processes have been improved based on understanding from operating experience, alongside R&D.
Water chemistry
Additionally, water chemistry needs to be optimised, accounting for the different materials present within the circuit.
NBAs make up the largest-surface-area coolant facing material within PWRs, by far. The largest use of NBAs is for the steam generator tubing, with some compositions susceptible to EAC and corrosion. Corrosion causes the formation of metal oxide films on these surfaces, which are soluble.
Dissolution of these films allows metal cations (Cr3+, Fe2+, Ni2+) to be transferred into the coolant and transported around its circuit, reacting and then depositing on surfaces.
In the industry, these deposits are commonly referred to as fuel crud (a backronym – Chalk River unidentified deposit), forming iron-nickel spinel oxides.
If the crud precipitates on surfaces within the neutron flux (typically this occurs at fuel within the core), an increase in solute concentration of species may occur at the base of the crud. This could be made up of boric acid (used as a soluble chemical shim within the coolant for reactivity management), and alkalising agents (e.g., lithium or potassium), causing uneven fuel burn-up.
The build-up of lithium species within the crud can lead to localised corrosion of the zirconium-based cladding, causing the formation of zirconium dioxide and hydrogen. This leads to lower thermal transfer from the fuel into the coolant, thereby increasing clad temperature (which is itself a direct contributor to zirconium clad corrosion) and the formation of zirconium hydride within the clad matrix, potentially causing embrittlement.
An additional consideration is the uneven moderation that can occur with high-duty cores, due to boron hideout within the fuel crud on the upper half of the fuel assemblies. This causes a negative axial power offset, known as crud-induced power shift (CIPS). Here, the fuel in the lower part of the core becomes more depleted and can cause attrition of plant shutdown margin.
Crud within the core can also become activated. Nickel undergoes a change to cobalt-58, a beta emitter, which can be transported around the circuit. Reactors typically enter a shutdown phase every 12-to-18 months depending on the plant, which allows the core to be shuffled and plant maintenance to occur.
Prior to shutdown, changes in water chemistry can lead to large activated particulate release that deposit on out-of-core surfaces. This makes shutdown inspections and repairs more difficult, potentially leading to an increase in shutdown durations or radiation shielding at out-of-core locations.
Thankfully, such issues can be challenged through modified water chemistries to minimise oxide dissolution, changing hot functional testing, and updated materials/manufacturing processes/specifications for the fuel (e.g. ZIRLO, M5), and steam generators (e.g. replacing Alloy 600 with Alloy 690).
Modifying the manufacturing process for steam generator tubing can also minimise corrosion through cold drawing or surface modification, as well as final heat treatments.
Also, modern reactor designers and materials engineers have avoided the use of cobalt or cobalt-containing materials where possible, as activation leads to Co-60 forming, a strong gamma emitter. Removal of cobalt alloys significantly decreases primary circuit dose rates.
Modern cobalt-free replacement alloys and coatings are now used instead. Cobalt-containing alloys are limited in use to control rod drive and core barrel reactor alignment in PWRs.
Materials specifications for coolant facing materials have also now been tightened to minimise cobalt within the composition, or replacing it with another material entirely.
Again, water chemistry can be modified to mitigate such challenges. Hydrogen water chemistry is used to create a reducing environment and mitigate radiolysis, thereby lowering corrosion extent. Since the mid-1990s, zinc has been injected into PWR coolant – this becomes incorporated within the corrosion product spinel in preference to cobalt, thereby decreasing activity.
Building up the pieces
The new developments at HPC and SZC in the UK will take into account the years of learning and will use modern water chemistry approaches described above.
However, such large-scale plants require significant investment at the outset, which has led to interest in small modular reactors (SMRs).
These are expected to have a cost advantage over conventional plants due to their size and are designed to be produced in a factory setting, allowing for economies of scale and faster onsite construction. Quicker build times directly reduce overnight capital costs.
The UK is currently running an SMR competition through Great British Nuclear. The ambition is to co-fund down-selected technologies through to the site-specific permissions process by the end of 2024, with a final investment decision by 2030.
Each of the technologies currently in the competition are light water reactors. However, these designs may challenge current practices. For instance, the Rolls-Royce SMR is being designed to operate without a soluble boron chemical shim, unlike other PWRs, which is expected to result in a simpler water chemistry, and also reduce CIPS risk.
A step further, the UK is poised to demonstrate advanced modular reactors (AMRs) that will use novel coolants early in the next decade. These helium-gas cooled, graphite-moderated reactors will operate with high outlet temperatures and will be designed to be built in a factory setting like SMRs.
AMRs are expected to facilitate co-generation – the production of industrial-grade heat or hydrogen to support the UK ambitions for net-zero by 2050.
To provide additional benefits to reactor operation and accident scenarios, advanced fuels are in development for near-term use, with the UK’s National Nuclear Laboratory (NNL) working with universities and other companies (see box-out below).
Powering up
The National Nuclear Laboratory (NNL) is the UK’s national laboratory responsible for nuclear fission R&D. It occupies a unique position in taking science from inactive laboratory-scale demonstration to deployment.
It is also the custodian of world-leading nuclear skills.
The NNL has facilities and equipment that provide long-term sustainable value for the UK in four areas – clean energy, environmental restoration, health and nuclear medicine, and nuclear security and non-proliferation.
Sitting between industry and academia, NNL conducts work for domestic and international customers, and reinvests profits from these customer workstreams into its internal R&D programme known as Core Science. This programme is used by researchers to build capability to accelerate delivery of world-leading research for industry.
Examples of this are UO2 fuels being developed with enhanced thermal conductivity, and physical vapour deposition of chromium coatings on zirconium alloy cladding.
The modified fuels aim to decrease fuel centreline temperatures, while the chromium coatings lead to a more corrosion-resistant film, minimising hydrogen uptake and providing improved performance during accident scenarios.
The NNL also undertakes modelling to establish the release of radionuclides, activation, transport, deposition and diffusion within different parts of the coolant circuit. This allows researchers to validate models against past operational experience (experimental and plant data) for future designs.
NNL is also involved in supporting reactor chemistry research and corrosion activities to support the development of AMR and nuclear fusion (see below).
Fusing the gap
The first European demonstration of a tokamak-type nuclear fusion reactor (DEMO) is expected in 2050. It represents a prototype power station, building on the learnings from the international thermonuclear experimental reactor (ITER) currently under construction in France.
The plasma in a tokamak is well controlled by use of strong magnetic fields, keeping the extremely hot plasma (150mln°C) away from the inside walls of the reactor.
Carbon – known for its high-temperature resistance – had been used in the past for the inner wall at the Joint European Torus (JET) project. It was replaced in 2009 with tungsten and beryllium to reduce carbon contamination of the plasma.
Thermal fatigue of the armour is an important consideration for both ITER and DEMO. Heating from transients causes expansion, which is constrained by cooler mass around the hot material, leading to compression cycling during plasma pulses.
Given that tungsten has an intergranular failure mode, ITER will make use of armour with a specifically textured tungsten. Grains within the tungsten will be elongated and orientated perpendicular to the plasma to minimise armour delamination.
Despite this, due to the high neutron flux expected within DEMO, among other factors, alternative armour materials and manufacturing methods are being researched. These include composite materials, such as tungsten reinforced with tungsten fibres, or a tungsten-zirconium composite, as well as sacrificial tungsten castellated lattices used within limiters at the first wall.
Research at the UK’s National Nuclear Laboratory is taking place into reduced ferritic martensitic (RAFM) steel for use within the water-cooled, lithium-lead breeding blanket for the DEMO reactor.
RAFM steels have compositions where specific elements are swapped out to minimise long-lived radionuclides. The aim is to allow fusion sites to be decommissioned at a faster rate than fission stations.
RAFM steel and high-entropy alloys have been assessed in high-temperature water environments and studied through collaboration with universities. This allows sub-surface features to be studied using advanced characterisation techniques like focused ion-beam scanning electron microscopy.
Coupled with energy-dispersive X-ray spectroscopy, this can give information on the location and chemistry of precipitates, corrosion product films or areas around crack networks.
If required, further information can be obtained by extracting small regions of these materials for investigation by transmission electron microscopy.
NNL has access to gas and water loops to simulate reactor chemistry, temperature and pressure.
Work within its Core Science programme is often performed collaboratively with academia. Rigs are being developed to allow for helium gas experiments at up to 800°C and 4MPa – i.e. for commercial, high-temperature, gas-cooled reactors pressure and temperature.
Current research is centred around oxidation and corrosion of NBAs. Iron-nickel-chromium alloys operating at temperatures of more than 700°C lead to degradation as CO2 and water impurities may be present.
Such rigs are expected to be modified to allow for research at elevated temperatures, necessary for enabling high-grade industrial heat and nuclear-enabled hydrogen.
NNL has also been working with universities to assess refractory high-entropy alloys as candidates for future advanced high-temperature materials. Such alloys may provide an avenue for operations approaching 1,000°C, have elevated corrosion and oxidation properties, as well the ability to better withstand high amounts of radiation.
As industry and academia learn from the materials challenges of the past, navigate the challenges in the present and anticipate the future material science conundrums ahead, nuclear fission and fusion may assist governments around the world to meet net-zero targets by providing a steady baseload power supply in combination with renewable sources.
Nuclear co-generation indeed could be a vital enabler for the hydrogen economy, reducing reliance on natural gas.