Circularity for composites
Stella Job, Sustainability Manager at Composites UK, clears up misunderstandings surrounding the recycling of composites, considers where we are now and where we need to be.
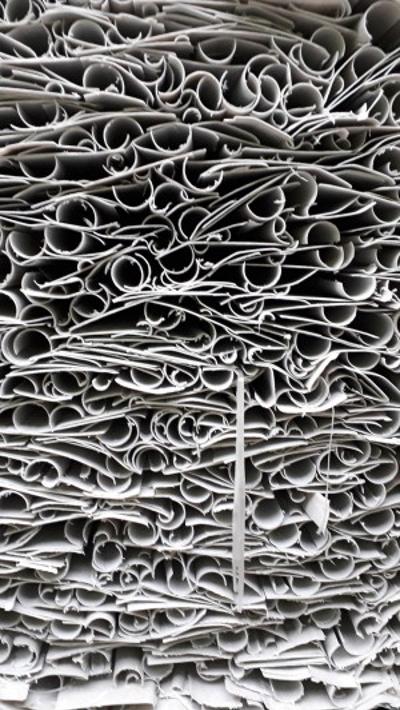
There is confusion as to whether fibre reinforced polymer (FRP) composites can be recycled. The answer is yes, composites can be recycled. Both carbon and glass fibre composites are being recycled commercially and have been for years. What is less straightforward is whether they can be recycled closed-loop, if processes are economical for end-of-life material, and if supply chains are widely available. There is still work to do and progress is being made.
Sustainability and the need for a circular economy are increasingly seen as vital to our long-term survival on Earth. Goal 12 of the United Nations Sustainable Development Goals acknowledges that ‘worldwide consumption and production – a driving force of the global economy – rest on the use of the natural environment and resources in a way that continues to have destructive impacts on the planet’. This needs to change.
FRP composite materials make an increasingly positive contribution to sustainability in numerous ways, especially through weight reduction and durability. The most fuel-efficient aircraft and the longest wind turbine blades could not be achieved without them. Extending recycling capability will have a far more positive environmental impact by validating composites for more markets than the direct impact of the recycling itself. Yet it remains that we cannot rest until we can make all our material cycles truly sustainable, and that is a long road.
Glass-reinforced polymer
Glass-reinforced polymer (GRP) composites are recycled commercially both by co-processing in cement kilns and by mechanical grinding. Thermoset composite waste in Europe is around 500kt per annum in 2020, estimated by the European Composites Industry Association (EuCIA), of which at least 95% is GRP. Most GRP scrap still goes to landfill, though increasingly it is sent to energy from waste (EfW) plants.
In cement co-processing, the resin is burnt for energy, replacing coal, and the glass fibres and mineral fillers are recycled into the cement clinker. The cement kiln route is operated as an established composite recycling programme by Neowa in Germany, which processes around 15,000t of GRP annually, with a total current capacity of 30,000t per year. Some other operations around Europe are sending smaller quantities to cement co-processing, generally mixed with other waste to regulate calorific value. Although the value of the ‘recyclate’ is low, a study from Composites UK finds cement co-processing compares favourably to landfill or EfW in environmental analysis where the polymer replaces coal. It is a good route that can be operated at scale.
Mechanical grinding of GRP has been tried all over the world over the last 50 years. Grinding to fine filler has consistently been found to be uneconomical, as the value of the filler it replaces is very low, and the finer the output material, the higher the cost in terms of energy, as it needs several passes through a milling machine. For in-house reuse of manufacturing waste, it may be viable where there is also value for marketing reasons or if disposal options are very limited or costly.
Grinding with fibre length retention is more successful, as less grinding energy is needed and the reinforcing value of the fibres is at least partially retained. This was demonstrated in 1973 by Wolfgang Unger, founder of Eco-Wolf in Florida, USA, which still sells equipment for grinding FRP and incorporating it into pre-existing spray-up equipment. Conenor in Finland has developed a process for extruded and moulded thermoplastic composites with GRP regrind in single- or multi-layer structures. They are currently improving and diversifying this through the Ecobulk project.
Gees Recycling in Italy, meanwhile, takes GRP waste from other companies and manufactures it into board products for use in bathroom interiors, shopfitting and furniture. These are embedded with RFID and NFC tags to track upstream production data and for marketing purposes, for example, if you put a smartphone on the product it will link to a page or start music or videos. Gees Recycling recycled almost 2,000t of composites in 2019.
Recycling by mechanical grinding is economically challenging and feedstock dependent, limiting it to small-scale applications, though Gees seems to be making good progress compared to others historically.
Several universities and companies, such as Reciclalia in Spain, have demonstrated GRP recycling by pyrolysis, where resins are thermally decomposed into oils and gas and fibres are recovered. As yet, none appears to be taking GRP waste commercially. Reasons for this may include the challenges of removing char from the fibres, the high-energy input required for pyrolysis (which is endothermic), the loss of mechanical properties due to processing damage and removal of the size, and the high throughput needed to gain economies of scale.
An interesting technology from the University of Strathclyde, UK, uses a fluidised bed thermal process to recover fibres, with a patented post-treatment that restores their strength to around 80% of virgin fibres, while stiffness is retained or even improved upon. This shows more promise than other processes for creating virgin-like recycled products, and it will be interesting to see if it can be scaled up economically.
Carbon fibre composites
Volumes of carbon fibre reinforced polymer (CFRP) scrap are much smaller than GRP, but the high embodied energy and cost of carbon fibre means that recycling is environmentally critical and more of an opportunity economically. Pyrolysis-based carbon fibre recycling processes are active in several countries including the UK, Germany, USA, Italy, Spain and Japan. These typically produce recycled carbon fibre (rCF) with comparable stiffness and only limited loss of strength compared with virgin fibres.
ELG Carbon Fibre in the UK now produces around 1,500t per annum of pyrolysis-recovered carbon fibre from laminates and prepreg, in addition to repurposing dry fibres from manufacturing waste such as end-of-reel. The rCF is sold as short chopped or milled fibres, or in non-woven mats, which can be infused with resin or co-mingled with thermoplastic fibres for hot-pressed applications. Short fibres for compounding with polymers are expected to be the largest markets in the longer term. The fibre forms are different from virgin woven or uni-directional (UD) fabric, which means it has taken time to spread knowledge on how to use the materials, but there has been much stronger uptake in recent years.
Alignment of fibres enables a higher fibre volume fraction (fvf), achieving specific properties closer to virgin materials. While carding can achieve limited alignment, the Universities of Bristol and Nottingham, in the UK, are both currently scaling up wet alignment processes to improve fvf. Mathilde Poulet, Technical Manager at ELG Carbon Fibre, notes that more aligned fabric or tape forms are among the missing products in the current range, though she does not expect them to fully compete with virgin UD.
Pyrolysis furnaces are very energy intensive, and several ongoing projects internationally are seeking to make more efficient systems. University of Nottingham, with support from Boeing, has developed a fluidised bed process at pilot scale, which has potential to be more contamination tolerant and less energy intensive than pyrolysis, though there is some compromise in the rCF properties.
Chemical recycling (which may be referred to as solvolysis or chemolysis) promises to recover resin chemicals as well as clean fibres, though the resulting chemical ‘soup’ is not easily converted back into high value resins, and so far it seems to be suitable only for fuel or low-grade chemical applications.
Vartega in the USA recycles scrap sourced from various dry fibre and prepreg sources using a chemical process, selling mainly pelletised rCF/thermoplastics. V-Carbon is scaling up a solvolysis process, which is now moving forward to commercialisation as a full lifecycle solution, with in-house know-how to process the recycled fibres through intermediate materials into parts.
Recyclable resins
The obvious recyclable resin family is thermoplastics, and we are seeing rapid growth in thermoplastic composites. These are mainly melt-processed, but also include reactive thermoplastics that polymerise in-mould, such as Elium acrylic resin from international company Arkema. However, melt recycling of thermoplastic composites is not as simple as it may seem, since there are still many possible combinations of materials. Recycling supply chains require higher volumes, so more common combinations, such as glass fibre polyamides, are likely to be recycled by melt processing, while lower volume applications may end up being thermally recycled, or simply incinerated.
There are ‘recyclable epoxies’ using cleavable, amine-based hardeners which cause the resin to break down more easily in a solvent. These include USA-based Adesso Advanced Materials’ Cleavamine and Indian Aditya Birla’s Recyclamine (acquired in 2019 from Connora Technologies).
Vitrimers, also known as covalent adaptable networks (CANs), supplied by companies such as Mallinda, USA, are gaining interest. These have mechanical and thermal properties of thermosets at low temperatures, but flow at high temperatures, so can be re-moulded and welded.
Wind turbine blades
The conclusions of the recent WindEurope/European Chemical Industry Council (Cefic)/EuCIA report, Accelerating Wind Turbine Blade Circularity (May 2020), are helpful. In particular, it notes that ‘the main technology for recycling composite waste is through cement co-processing. WindEurope, Cefic and EuCIA strongly support increasing and improving composite waste recycling through the development of alternative recycling technologies. This requires increased research and innovation funding’.
The report notes that while end-of-life wind turbine blades will still be only about 10% of GRP waste in Europe by 2025, volumes will increase dramatically in the next two decades due to replacing turbines and decommissioning wind farms. The physical downsizing of the huge blades will always be a costly challenge, regardless of the recycling route. Disbonding adhesives could play a useful part in mitigating the problem, though 150mm thick GRP at the blade root will never be easy to break up.
The conclusion is that many blades can safely continue beyond their stated design life, and life extension of blades is an important area where good practice is still developing. A DNV-GL standard for life extension of wind turbines now exists (DNVGL-ST-0262) and a technical specification is under development, led by Lloyd’s Register (IEC TS 61400-28). For the composite blades, work is still needed on the use of non-destructive testing to reduce uncertainty in determining asset values.
Future routes
Composites UK has set out a Vision and Roadmap for Sustainable Composites (2019), which has been developed through the UK High Value Manufacturing Catapult’s ReDisCoveR project.
Most of the current and future recycling routes result in the resin being burnt, which places a strong imperative on manufacturers to use bio-based resins so the carbon dioxide put into the atmosphere is first-generation bio-derived. This requires engagement with chemical companies and creating demand for bio content to generate economies of scale. In the long term, materials will have to be bio-based or 100% closed-loop recyclable to be ultimately sustainable. Composites UK has a useful webpage listing materials with bio/recycled content currently supplied by its members.
Manufacture of virgin carbon fibre uses a lot of energy, so in some applications it does not compare favourably in a lifecycle assessment, despite the outstanding specific properties. Solutions must include replacing virgin fibre with recycled where possible, as well as reducing fossil fuel use in production and using bio-based precursors.
Another solution lies in totally different business models, such as pay-by-the-hour, where the vehicle structures would be in use for much greater lifetime mileage. We need to think outside the box and learn to integrate technical/material solutions with sustainable business models.
Waste reduction must be addressed more rigorously. In manufacturing this means moving towards near-net shape processes, quality control, training and working with customers to eliminate wrong orders. Reducing end-of-life waste requires design to minimise material usage and increase durability, alongside implementing effective maintenance and life extension methodology. Training the up-and-coming generation to design and manufacture for circularity is essential.
Overall, it is crucial to understand the whole life impact of products, as circularity is often trumped by other factors, such as weight reduction. We must creatively bring together materials science with digital technology, business models and waste management to achieve truly sustainable material cycles.