Ceramic matrix composite coatings reach new heights
Lower emissions and increased aircraft performance are billed as the benefits of a prototype machine to improve the coating coverage on ceramic matrix composites (CMCs).
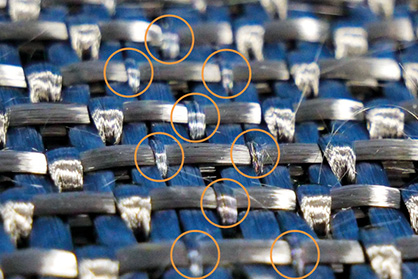
The objective was to develop a new reel-to-reel coating technology to replace the current batch coating method.
A project on Continuous Interface Coating for Silicon Carbide (SiC) composites, or CICSiC for short, is being delivered by The University of Sheffield Advanced Manufacturing Research Centre (AMRC), UK, in collaboration with Archer Technicoat Limited, TISICS Metal Composites and Cygnet Texkimp.
The research has focused on the manufacture routes for these composites, of particular interest for high-temperature (2,000°C) applications in sectors such as aerospace, space and nuclear, boosting the thermal and fuel efficiency performance.
The interface between the fibre reinforcement and the matrix is a critical component of the CMCs. The project aims to develop equipment and processing know-how for uniform, continuous coating of interfaces on SiC fibres, such that the mechanical properties of the materials can be more closely specified to enhance their aerospace application.
In the batch coating method, a preform made from uncoated fibre is treated in one step, making it difficult to ensure even coverage of all areas of the preform with equal precision. The new method uses a reel-to-reel process to apply the interphase coating.
This model enables tight coating tolerance by treating the fibre before it is shaped into a thicker and complex-shaped component preform, where it becomes difficult to process all areas of the component with equal precision. This allows for shapes with increased complexity to be formed.
Material is wound from its original spool onto a new one with the interphase being applied in-between, ensuring uniform coating. Still on a spool, it can easily be used in fibre processing technologies.
It has been demonstrated that complex preforms (more complex than 2D woven) suitable for infiltration with a ceramic matrix can be produced in a variety of ways at an industrial scale.
The project has tested ceramic fibre supplied by Nippon Carbon Co Ltd, with coating applied in a variety of industrial-scale processing applications, such as 3D weaving – including binder yarns in an eight-layer orthogonal weave – and tailored fibre placement.
The research team say this enables the development of more efficient engines, offering significantly lower weight, cooling requirements and aircraft emissions.
'Silicon carbide composites are of interest to many industry sectors looking at high-temperature applications,' says Steffan Lea, a Technical Fellow in the AMRC’s composites team. 'The ability to produce more complex preforms from continuous SiC fibre will enable new designs and applications for this high-performance CMC material.'
Lea notes that the AMRC’s understanding of how to process SiC fibres has developed through this project. He adds, 'The AMRC has gained familiarity and knowledge on how to process SiC fibre on industrial-scale machines. Our knowledge on how to process SiC fibres on weaving looms to produce 3D-woven preforms enables the production of unitised preforms with added complexity. Using the Nicalon on tailored fibre placement allows us to make efficient use of the material, only placing it where it is required and controlling the path of the fibre to make best use of its properties.'
End-users of the coated fibre are part of the consortium’s test regime to ensure it meets industrial requirements.