Building a new industry
The UK Green Alliance’s latest report lays out a plan for the construction sector to move forward in a less resource-heavy and wasteful way. Alex Brinded reports.
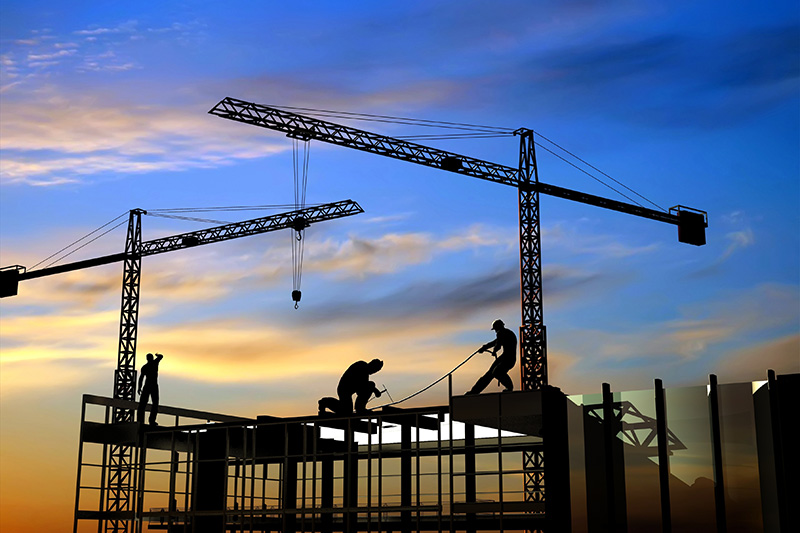
The latest report from the UK Green Alliance on Building for a greener UK economy highlights that the construction sector uses more raw material than any other in the UK, produces the most waste and accounts for 25% of UK carbon emissions.
A launch event at The Building Centre in London, UK, featured a panel debate with Dr Danielle Densely Tingley, Senior Lecturer in Architectural Engineering at the University of Sheffield; Rachel Hoolahan, an Architect and Sustainability Co-ordinator at the architectural firm Orms; and Mark Edwards, the Head of Sustainability for Gatwick Airport.
One of the report’s authors, Green Alliance Policy Analyst Heather Plumpton, issued a call to action in her introduction. 'We need a resource-use target. With carbon, we know where we need to be at a given time as there are very clear plans for it. We can reduce raw material use by 35%...We think government should use this report as a baseline to spur action on.'
The report quotes how embodied carbon will account for half of the built environment’s emissions by 2035, as outlined by the UK Green Building Council. It cites research that says, in 2018, this was 43MtCO₂e on a consumption basis, which includes emissions in overseas supply chains – 60% of which came from materials extraction and production.
Research quoted in the Green Alliance report, in turn, finds that the UK construction sector uses nearly 100Mt of materials for new buildings and infrastructure projects each year, which does not include material usage for internal fittings like bathrooms and kitchens. The Green Alliance says that 61% of construction materials are used in buildings while 39% are in infrastructure.
In 2020, UK Research and Innovation reported that the construction sector uses 0.5Mt of minerals every day from home and abroad. Green Alliance suggests that raw material usage per building should be reduced through better design, reusing components and materials, and increasing recycled content. They say that materials should also be used at their highest value for as long as possible, by prioritising renovation to extend existing building lifetimes.
The analysis shows that, by 2035, currently available techniques and technologies could reduce raw materials use by more than a third, which they say could reduce the sector’s carbon footprint by 39% as well as relieving pressures on land-use, biodiversity and waste.
The authors have compared a business-as-usual scenario with a 2035 circular scenario – where chosen interventions have been modelled for their cumulative impact. They say these measures could prevent 418Mt of raw material being extracted, which equates to the amount of material needed to build 1.7 million detached houses.
The study is based on a soon-to-be published analysis by researchers at the UK FIRES academic consortium, which has put together a comprehensive baseline for material use in the UK construction industry. Two workshops with industry representatives and academics were held by the report authors to test their findings, and they spoke to 16 companies and trade associations.
Being bold
Densely Tingley strongly kicked off the debate around the report’s findings with, 'Why is it going to take to 2035? The technologies are available now. The 35% is a start.'
The report stresses how the consulted experts agreed that current technology can lead us towards a circular construction sector, with a need to focus on implementing best practice.
Densely Tingley asked the question, 'What if we banned resource use…as academics we can ask that. How does that change our existing buildings? It is not just what we can do now but what can we deliver in the next few years.'
Hoolahan continued the thought-experiment, asking, 'What if we closed landfill or take the opportunity to use no materials'. Hoolahan felt that there needed to be more urgency, especially with how long a building can take to be erected. 'Some of our projects were conceived 15 years ago. I was surprised design was not a bigger part [of the report].'
The experts consulted by the Alliance suggested that to avoid overspecification and over-ordering in infrastructure projects, upper limits on material use should be included in design codes, in addition to the lower limits to ensure infrastructure strength.
Asked if the picture was different for his sector, Edwards said, 'Yes, there are some differences with infrastructure but there are some commonalities. They [infrastructure projects] do not have an end of life. Most of us came here on the [London Underground]. The Bakerloo line is nearly 130 years old. These things are there to serve society’s needs. But there are differences in the way things are funded publicly and privately, which can see massive difference in infrastructure management. How do we align all these incentives?
'The entire construction industry is project based. How do we take things from one project and use it on another? The crucial thing is making sure it happens in different areas.'
The think-tank recommends the government emulates the Netherlands by introducing a sector-specific resource-reduction target for construction. They outline three main areas for change: financial incentives and support, more circular design and retrofitting, and better data.
Densely Tingley said, 'I would love us to get to a national database. We need to think about what is coming out at end of life. Getting it down to these really simple starting points.'
Hoolahan echoed Plumpton, 'Most architects have caught up to where the carbon lies in the building. If we can shift that to circularity.'
Edwards called for alignment within the construction industry to reuse the same components. He argued that it was not difficult to find reusable materials. “I would suggest that buying a second-hand car is more complicated than reusing a window.'
The issue is working out what happens if an item or component is damaged in transit before it is repurposed. 'The whole industry needs to get more comfortable with reuse…Why is there a pathological view that everything has to be new?'
Backing reuse
Hoolahan shared a case study from her firm Orms. 'We started simple and looked for something that was relatively low risk. We started with bathrooms and sinks.' She described however that there is always a kick-back reaction to suggesting that something could be reused, with people asking if it is broken or inherently damaged in some way.
The Green Alliance report details that reuse and recycling of steel, glass, aluminium, timber and concrete aggregate could equal 18Mt of sector demand.
'There are now protocols in place to safely take steel out of buildings. The bigger problem is concrete, and it is going to be sticking around for a very long time. [Perhaps it is about] keeping the building there and not knocking it down,' pointed out Hoolahan.
Concrete makes up 79% of virgin material used in building construction, and an even higher proportion in infrastructure. In 2018, more than 60% of upfront carbon emissions in the sector were from concrete and other cementitious materials. In 2020, the Mineral Products Association outlined plans to use carbon capture and storage to meet net-zero carbon targets.
Plumpton revealed that steel and aluminium make up only 3% of material use by weight in constuction but account for 26% of the industry’s upfront carbon emissions. This highlights that recycling is a significant intervention for aluminium, plastic and glass, as well as steel, where it can majorly rescue virgin material demand. The report suggests that design improvements and reuse can increase recycling to up to 95%.
To drive action, the publication urges the UK Government to address the imbalance between Value-Added Tax (VAT) for new build and retrofitting, with the former being zero and the latter charged at 20%.
They also recommend that the current VAT ‘holiday’ in the UK for energy-saving products like insulation and heat pumps becomes permanent. And that this should be extended to other retrofitting activities that preserve or improve a building’s environmental performance.
A funding package for small companies could also help bring to market new solutions that improve the reuse of construction materials.
In 2015, Experian estimated that even if VAT on housing renovation and repair were to drop 5% in the UK, it would be a boost of £15bln over five years and create nearly 100,000 extra jobs in construction and the wider economy.
Hoolahan asserted, 'VAT is super frustrating. It is a very hard sell, when you show them [clients] the price together with 20% on extra. We are telling the government, deal with the VAT issue. It needs to be balanced out or preferably switched around.'
Edwards had two things on his wish list. One is an effective resource management service in one place. 'Like a dating service for materials that can incorporate the Carbon Budget. These things exist but there are a gazillion of them. Two, some kind of construction business that can store these materials and do the testing for second life and become a logistics business.'
Materials passports were also mentioned as worth pursuing for buildings so that crucial information about the materials and components used can be tracked. They recommend measurements such as material intensity, reused material content, recycled material content and reusable materials.
The 2035 circular scenario modelled included increasing the use of Modern Methods of Construction (MMCs) to 30% in housing and commercial buildings. MMCs include onsite technologies and offsite manufacturing of building components. Up to 90% less waste has been reported in some cases, according to the House of Lords Science and Technology Select Committee in 2018.
The report cites that pre-manufacturing can reduce embodied carbon by 45% as well as enabling of energy-efficient buildings. Some case studies say that it can increase building quality, with 70% less onsite labour and projects being 20-60% faster. The UK Government has a taskforce to accelerate MMC, with its Affordable Homes Programme requiring up to 25% of new housing to be delivered in this way. However, the Alliance noted that some experts were concerned that some pre-manufactured homes are difficult to recycle.
Down with demolition
Green Alliance points to London as being a good model for central government as all developments bigger than a minimum size must submit a circularity statement. They also suggest that pre-demolition assessments should be mandatory – to replace existing buildings we need to justify the demolition.
Before applying for a demolition permit, Densely Tingley says it is important to think about how you can reuse the structure or the materials. 'We need Extended Producer Responsibility so sellers can take resources back,' she suggested.
Hoolahan added, 'The manufacturers should have to demonstrate how to uninstall [their product]. Managers do not understand that their products are really hard to get out.'
The Green Alliance and the panel agreed that whatever happens the construction sector needs to change – also addressing problems with productivity, supply chain risks, housing and affordability crises, and an ageing workforce that needs re-skilling.
'Dematerialisation goals are incentives to move quickly,' Edwards summarised.
Costing construction mixed waste
A tool to measure the ‘true cost’ of waste on Scottish construction sites has influenced a new industry protocol.
A series of studies by researchers at Glasgow Caledonian University, UK, culminated in a two-month field trial in 2022. Here, the cost of waste items found on multiple Scottish ‘mixed-waste’ construction sites was calculated using their tool.
It has now been adopted by Zero Waste Scotland as part of its Site Waste Reduction Protocol to enable staff to record and quantify everything.
The protocol outlines how to best use the calculator, which includes guidance on monitoring skips, estimating quantities and classifying material types. When enough data has been collected, the calculator can produce reports to show what types of materials are being wasted and why, how much these have cost the businesses, and enables the carbon footprint to be calculated.
Tracking construction materials
Materials passports are being used on the 8,550m2 Edenica office being constructed in the City of London, UK, by the Waterman Group consultancy.
These are digital datasets that describe the characteristics of materials, and components in products and systems so that they can be recovered and reused at the building’s end-of-life.
A sustainability team from Waterman is working alongside project manager Third London Wall to ensure the materials passports contain key characteristics of selected building materials in a centralised database.
Edenica is a pilot project and the first scheme in the City of London to be designed as a storage bank where materials are held for reuse.
Designed by Fletcher Priest Architects, the office block on 100 Fetter Lane for BauMont Real Estate Capital and YardNine is designed to optimise operational energy.