Battery ‘biographite’ from wood by-products
A ‘biographite’ for lithium-ion batteries that is made from forestry by-products is being commercialised by CarbonScape in New Zealand.
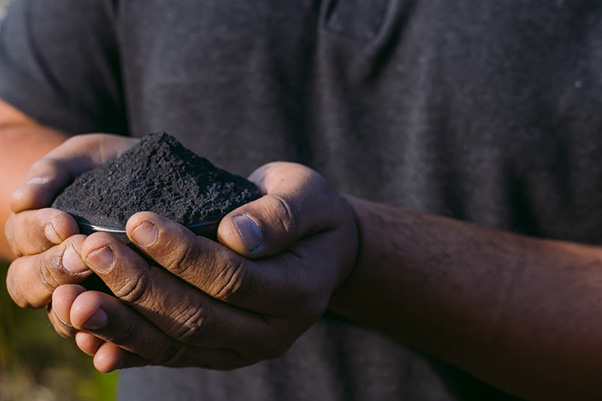
A leading supplier of wooden construction material in Europe – Stora Enso – is said to be investing US$18mln, along with other partners such as battery innovator ATL, in the material made from by-products such as wood chips.
Graphite is around 50% of a lithium battery. In June this year, Reuters reported Project Blue’s forecast of a 777,000t per year deficit in supply by 2030. The article also quoted Benchmark Intelligence analysis that US$12bln of investment is needed in graphite by 2030, with 97 new mines by 2035 to meet demand.
CarbonScape pitches the biographite material as an alternative. It reports that high levels of crystallinity mean that the biographite anode has greater capacity than synthetic graphite at more than 360mAh/g.
Charging and discharging of a battery with biographite is also said to be identical to that of a conventional device, while the wood-based material is reported to reduce CO₂ emissions by up to 30t per tonne of material, cutting the carbon footprint of each battery by a third. This could potentially reduce sector emissions by more than 86Mt of CO₂ per year by 2030, suggests the firm.
CEO Ivan Williams shares, 'The [manufacturing] process is formally known as thermo-catalytic graphitisation. In brief, we pyrolyse wood chips into charcoal, add a catalyst, and then catalytically graphitise it. We then purify, densify and coat this ‘raw’ graphite to make battery-anode-quality graphite. We fully recover and recycle the catalyst afterwards.'
He continues, 'We have honed this process to run at half the temperatures required to make synthetic graphite, and to produce it in hours, not weeks – meaning it is also far less energy intensive and therefore cost competitive.'
The material has been tested in real world, multi-layer cells up to several Amperes in hour per size, using both nickel-manganese-cobalt and lithium-cobalt-oxide cathodes, the company states.
'Our biographite anode compares well to all electric vehicle and other market specifications. The cells have undergone hundreds of cycles without significant reduction in capacity at 25°C and 45°C.'
On the carbon accounting, Williams clarifies that the energy required for manufacture has been considered when working out the overall emissions.
'Our carbon emissions calculations are based on an inclusive carbon balance, in accordance with the relevant European norms,' Willams says. 'To start with, we figure out the negative emissions associated with biographite production – atmospheric carbon (CO₂) is captured by trees, so this counts as a negative emission – we first calculate the amount of carbon stored in wood. Then we calculate all the positive carbon emissions from the process and associated electrical energy consumption (which has a defined CO₂ emission per kilowatt hour). The sum of negative (captured carbon) and positive emissions provides the overall carbon footprint for biographite.'
The new material can reportedly be produced locally to ensure secure supply chains for European and US battery manufacturers. Williams adds that the type of wood by-products used does not affect battery performance but can affect the economics.