Beyond Glass: Silica sand applications
Glassmaking is silica sand’s main application, although the mineral straddles an array of uses and is making a play for new markets. Michael Schwartz finds out more.
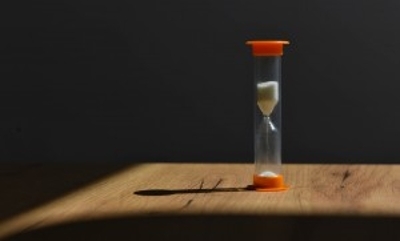
In mining terms, silica (SiO2) is most commonly found in either a crystalline state or amorphously after weathering or plankton fossilisation. Surface mining in open-pit operations is the main method of extraction, although underground and dredging techniques are also deployed.
The extracted ore then undergoes considerable processing to increase the silica content by reducing impurities – 95% SiO2 content is preferred for industrial and manufacturing applications. It is then dried and sized to produce the optimum particle size for the intended application to meet customer specification.
One company, Select Sands, which operates in Arkansas, USA, supplies a detailed list of the uses for silica sands, notably:
- Glassmaking – silica sand forms the primary component of many types of glass, to the extent that its own chemical purity determines the colour, clarity and strength of the glass. This is before ground silica is used in fibreglass and reinforcing glass fibres.
- Metal casting – ferrous and non-ferrous, where metal parts ranging from engine blocks to sink taps are cast in a sand and clay mould to produce the desired shape. A high-fusion point of 1,760oC helps generate stable cores and moulds and prevents interaction with catalysts and binding materials, before the core sand can be recycled for new cores and moulds.
- Everyday applications – ranging from food processing to soap and dye production, SiO2 is the main component in chemicals such as sodium silicate, silicon tetrachloride and silicon gels.
- Metal production – with silica sand working as a flux to the melting points and viscosity of slags for greater efficiency.
- Construction – industrial sand is the primary component in many building products. Examples include whole grain silica for flooring compounds, stucco, roofing shingles, skid-resistant surfaces and asphalt mixtures to provide packing density.
- Paints and coatings – for improved appearance and durability.
- Ceramics – ground silica can regulate drying and shrinkage and improve structural integrity.
- Water filtration – with uniform-sized industrial sands removing contaminants.
Energy Bound
High-purity (99% SiO2) silica sands are available in the US state of Arkansas, where Select Sands works the Ordovician St Peter sandstone formation. These sands, known as the Ozark Operations, have seams that register thicknesses of up to 150 metres and are considered a major source of both premium quality industrial sands and Tier 1 quality fracking sands.
The oil and gas sectors are firmly in the company’s sights, given Arkansas’ proximity to the Texas, Louisiana and Oklahoma shale-plays, with potential savings in transportation costs over sand mines in Wisconsin, for example. Further areas for expansion are new-end markets, namely solar panels, specialty coatings, wind turbines, polymer additives and geothermal energy systems.
UK profile
One benefit that silica sand operators possess in England is recognition as a mineral of national importance within the country’s National Planning Policy Framework (NPPF), with a requirement to maintain landbanks at individual sites. In Scotland, Local Authorities should plan for the working of silica sand while in Wales applications are dealt with on a case-by-case basis. Northern Ireland, meanwhile, has a strategic objective to facilitate sustainable minerals development.
In Britain, the Silica and Moulding Sands Association (SAMSA) is the principal trade association for the UK silica (industrial) sand producers. With its parent organisation the Mineral Products Association, SAMSA provides the lobbying platform for silica sand producers regarding government land-use planning, environment, energy, health and safety and other legislative and policy matters. SAMSA currently represents 10 of the UK’s leading industrial sand producers and is represented in Europe by The European Association of Industrial Silica Producers, through The Industrial Minerals Associations - Europe.
The silica sand industry has a longstanding and proven legacy of high-quality restoration for nature conservation after use. Operators are also at the forefront of maximising efficiency by investing in the latest mineral processing techniques, for example, electromagnetic technology to reduce the iron content of glass sands and inverter technology in motors to allow more efficient use of speed. Computerised monitoring of mobile plants at quarries, meanwhile, means less idling time. Less aggressive braking and acceleration also play their part in a smoother, less wasteful process.
SAMSA and its members have recently worked with the British Geological Survey (BGS) in a fundamental review of the Silica Sand Mineral Planning Factsheet, bringing interested parties up to date on the importance to society of silica (industrial) sand and downstream products.
Materials World asked Richard Page, the SAMSA President, several questions on the UK’s generation and usage of silica sands. In the case of reserves, for example, both SAMSA and BGS point out that the term reserves should only apply, where in the land-use planning system, valid planning permission has been granted and the reserve can be extracted.

In the last decade, 12 new permissions, both for new sites and for extensions to existing sites, have been granted. In general, during this period, the quantity of new silica sand reserves has kept pace with increased production rates. However, permission for new reserves must take into consideration the different specifications of the industrial sands necessary to meet specific markets and the significant investment involved in both the permitting process and bringing a site on-stream.
Glass production remains a prominent downstream use for UK-excavated silica sand. Figures for 2018 show 29% of the sands went into glass manufacture, 30% for horticulture and leisure uses, 5% for foundries and 36% for other industrial applications such as water filtration and rail braking material.
On the move
In the UK, there is an almost total reliance of the silica sand sector on road transportation. One site, however, operates primarily via a rail link. The Leziate quarry near King’s Lynn, Norfolk, uses rail to supply glass manufacturers in Yorkshire and northwest England. Ship transportation is also used, but again in one location only – the Lochaline silica sand mine
in Scotland. This is the only underground sand mine in Europe, comprising pure white sandstone extracted by room and pillar. After drilling, blasting, loading into dump trucks and moving to the surface where impurities are removed, the sand is mostly taken by ship from a dedicated pier. However, the importance of industrial sands to manufacturing and other industries ensures that processed silica sands travel the length and breadth of the UK.
Argentina’s shale plan
Three South American countries – Argentina, Uruguay and Brazil – hold significant silica sand reserves. As an example, Canada’s U3O8 Corporation owns 38% of South American Silica Corporation and has selected certain properties precisely because of their suitability for use in Argentina’s Vaca Muerta shale oil and shale gas region. Sand quality and short transportation distances are crucial in this respect.
Argentina has seen how fracking has helped turn the USA into an oil-exporting nation after a period as a declining oil producer. Shale gas is displacing coal in American power stations, with consequent reductions in greenhouse gas emissions.
Argentina imported US$7bln worth of oil in 2015, and identifies fracking as a way to achieve energy independence – hence the need for silica sand. Vaca Muerta is a highly significant factor in this drive for self-sufficiency, containing the world’s third largest shale gas and fourth largest shale oil reserves. What is more, conventional oil production has bestowed upon Vaca Muerta much of the infrastructure it needs to function. Partnerships with key international companies such as Chevron, Total, BP and many others are set to guarantee efficient operations.
U3O8 notes Argentina’s potential to become what it describes as the ‘energy powerhouse of South America’, by developing these shale oil and gas reserves. Solar resources from northern Argentina’s Atacama Desert and wind resources from the country’s southern Patagonian region would contribute their own major renewable energy input.
A real challenge
Recent research by Imarc Group has identified the global silica sand market to be worth US$8bln, attributing much of this to the many uses that can be found for it. Using silica sands as a proppant has advanced growth of the market, with further increases down to upcoming infrastructure projects in transportation and leisure. Glass, however, still accounts for over a third of that market and remains the largest end user.
Silica sand resources cannot, of course, last forever. There is a real challenge to this sector of the minerals industry to balance increased demand from ever-growing new uses with the need to discover new resources, while at all times applying environmentally friendly mining methods and sensitive restoration.
Did you know?
Lochaline silica sand mine in Scotland is the only underground sand mine in Europe, comprising pure white sandstone extracted by room and pillar. Lochaline has a long tradition of producing pure silica for applications and was renowned for the production of periscope lenses and gun sights during the war years.