Battery insulation
A patent for non-woven, ceramic fibre mats for battery insulation in electric vehicles.
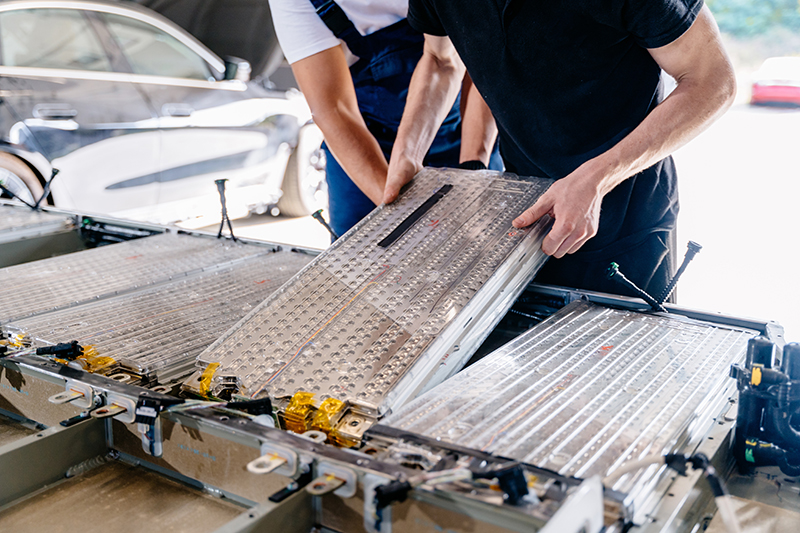
Mats made from non-woven webs of ceramic fibres find various applications in electric vehicles. For instance, they are wrapped around the fragile, ceramic-monolith cores of catalytic converters and diesel particulate filters to shield against shock and vibration damage, compensating for thermal expansion and preventing the leakage of exhaust gases.
Ceramic mats can also be used as thermal insulation materials inside engine exhaust pipes and catalytic mufflers. More recently, these materials are proposed as thermal and fire barriers to prevent thermal runaway events in or around batteries in electric vehicles (EVs).
However, commercially available ceramic-mat materials contain fibres of alumina and/or silica with diameters below 3µm. Such fibres can become airborne during mat production or their use, and are respirable by humans leading to health concerns.
European patent EP3790850B1, granted to 3M Innovative Properties Company in March 2024, describes non-woven ceramic materials that appear to mitigate this problem.
In particular, the patent claims protection for an EV battery module comprising a predominantly 2D or 3D non-woven structure with a plurality of discontinuous, polycrystalline, aluminosilicate, ceramic fibres.
According to the patent, these fibres allow the non-woven structure to withstand high-operating temperatures. The predominantly 2D non-woven structure is a mat, sheet, or blanket, and has a major surface dimension that is at least 10 times larger than its thickness direction.
The fibres are cohesively bonded together using a fired precursor inorganic binder, siloxane. Each cohesively bonded discontinuous fibre is bonded to one or a plurality of other such fibres at one or more locations along its length.
The inorganic binder mitigates the health concerns associated with the potential release of respirable aluminosilicate ceramic fibres.
The patent further explains that oil-based, liquid, binder precursors (such as silicone oil, a member of the siloxane family) are particularly preferable, as surface tension can result in the liquid after application, accumulating at points of contact between adjacent fibres. Bonds between fibres form at these points of contact after the binder has been fired.
Such precursor inorganic binders can also be applied easily by immersing the non-woven structure into a bath or by spraying the precursor onto the structure.
The patent also claims protection for a method of making the non-woven article.
This involves flowing an aqueous, ceramic precursor sol through multiple orifices to produce a plurality of substantially continuous or continuous filaments. Then removing at least a portion of the water from the filaments to partially dry them, passing these dried filaments through an attenuator to draw them to a desired diameter, and then collecting them as a non-woven web on a surface.
The aqueous, ceramic precursor sol used comprises at least one of alumina particles or silica particles dispersed in water, as well as at least one of a hydrolysable aluminium-containing compound or a hydrolysable silicon-containing compound.
In principle, the attenuator can be controlled so that the resultant filament has a diameter no less than, or equal to, 3μm, making it non-respirable.
According to the patent, substantially continuous or continuous filaments can be chopped into shorter fibre strands to produce the discontinuous fibres used in the non-woven article. Alternatively, the attenuator itself can segment the filaments to a desired length. The patent also includes several experimental examples that illustrate the production of aluminosilicate fibres and non-woven mats.
Several of these examples produced fibres with minimum diameters above 4μm, with fewer than 2ppm of the fibres with diameters below 3μm. In contrast, some of the comparative examples, based on commercially available ceramic blankets, contained over 49,000ppm fibres with diameters below 3μm.
The examples also illustrate how a precursor inorganic binder leads to the formation of a cohesive or self-supporting, fired, ceramic-fibre, patterned mat.
In contrast, comparative examples prepared using an organic binder, or no binder at all, are unable to achieve cohesive or self-supporting fired mats. Moreover, the examples appear to show that combining a precursor inorganic binder with an organic binder can lead to cohesive or self-supporting mats both before and after firing.
The inventors explain that before, and possibly during, the initial stages of firing, the 3D shape of a green-fibre, non-woven structure can be held together by using organic binders. However, the organic binder is effectively burned off at later stages of firing, when inorganic binders are more useful to maintain the 3D shape. The claimed invention therefore requires an inorganic binder, while the use of an organic binder is merely preferred.