Battery-grade lithium carbonate crystals from UK brines
A spin-out company from the University of Manchester, UK, reports to have extracted lithium carbonate from UK brines with more than 99.5% purity.
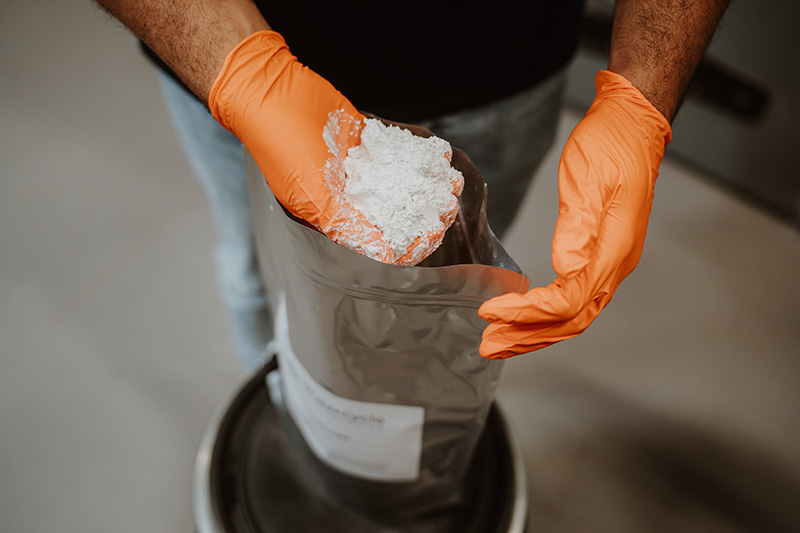
Watercycle Technologies says the pilot, partnered with Cornish Lithium, represents one of the first large-scale productions of lithium carbonate crystals in Europe with a purity suitable for use in electric vehicle batteries.
They have produced more than 100kg of the material at the site in Runcorn, Cheshire, using a direct lithium extraction and crystallisation (DLEC) technology.
The integrated end-to-end pilot is the result of an Innovate UK Smart grant and comprises three main stages, explains Heloise Grandjouan, Research Scientist at Watercycle Technologies. The first is a pre-treatment process to manage a range of 'complex waters'. Next, the brines pass through a membrane-separation filter before the solution is finally turned into lithium crystals.
'We designed the system to be easily reconfigurable, which enabled us to adapt to different brine chemistries,' explains Grandjouan. 'One of the challenges with other lithium extraction technologies is that they are not very adaptable…Brine chemistries can vary dramatically around the world, not only in their chemical composition, but also in their temperature and pressure.'
The start-up set out to overcome these challenges by creating what it describes as a 'universal mineral extraction machine'. The novel DLEC technology means they can test the entire range of brine types, explains Dr Seb Leaper, CEO and the spinout’s co-founder, unlike direct lithium extraction on its own.
The latter requires a lithium-containing solution, often lithium chloride, in its final step. However, Leaper explains this only partially resolves the challenges encountered in producing lithium crystals. A second technology provider is then needed to covert this solution into saleable salts such as lithium carbonate. And then a third provider is often required to purify the crystals to a battery-grade product.
'Our direct DLEC technology incorporates all stages and crystallises this lithium-salt solution to obtain the lithium crystals directly, producing freshwater as a by-product,' he reports.
'We take our knowledge in crystallisation science and transpose it to other sectors offering our customers a more versatile product that can produce multiple minerals, not just lithium. This also enables us to produce different forms of lithium salts that can adapt to the changing battery chemistries over time.'
They have tested the system on Cornish waters alongside other UK brine suppliers to yield this quantity of battery-grade lithium carbonate.
Leaper notes that the modular system offers a more flexible design that can be tailored for bespoke uses, while the technology’s low capital cost means smaller businesses can partner with the University’s spin-out.
Moving forward, Watercycle Technologies says it has drawn on its pilot to incorporate more diverse inputs, like solid waste, batteries and black mass. It also plans to build a new dedicated system for producing tonne-scale lithium carbonate in the next six months. The long-term plan, Leaper adds, is to 'unlock mineral reserves around Europe', so the company can deliver a sustainable supply of lithium carbonate to the continent’s 'growing fleet of gigafactories'.
'Cornish Lithium recently said we need to produce 50,000t of lithium carbonate annually by 2030 to supply the UK’s needs,” citing the importance of the UK moving away from its 100% reliance on an imported battery minerals supply.
'We will achieve this through a staged scale-up and proof of viability at each stage, [but] we believe it is harder to go from grammes to hundreds of kilogrammes than from hundreds of kilogrammes to hundreds of tonnes.'