AI unearths tough microstructures in composites
An artificial intelligence (AI) system from MIT melds simulations and physical testing to forge materials for diverse engineering uses.
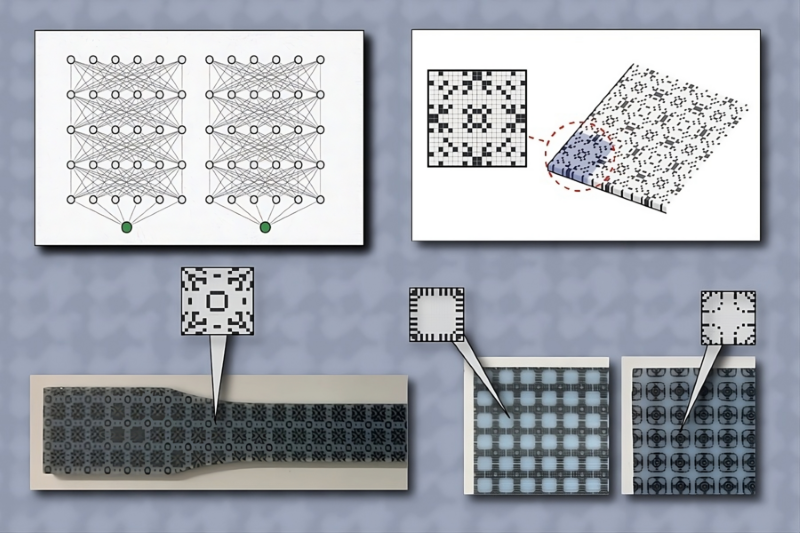
A new computational pipeline developed over three years efficiently identifies stiff and tough microstructures suitable for 3D printing in a wide range of engineering applications. The approach greatly reduces the development time for high-performance microstructure composites and requires minimal materials science expertise.
© Alex Shipps/MIT CSAILThe new system integrates physical experiments, physics-based simulations and neural networks to navigate the discrepancies often found between theoretical models and practical results.
As a result, they have discovered microstructured composites that are much tougher and durable, with an optimal balance of stiffness and toughness.
A key to this approach was the use of neural networks as surrogate models for the simulations, reducing the time and resources needed for material design.
'This evolutionary algorithm, accelerated by neural networks, guides our exploration, allowing us to find the best-performing samples efficiently,' says Beichen Li, an MIT PhD student.
The research team started the process by crafting 3D-printed photopolymers, roughly the size of a smartphone but slimmer, and adding a small notch and a triangular cut to each.
After specialised ultraviolet light treatment, the samples were evaluated using a standard testing machine — the Instron 5984 — for tensile testing to gauge strength and flexibility.
The team is focused on making the process more usable and scalable.
An open-access paper on the work was published in Science Advances.