AI probe to monitor fluid production
Rheality and Clean Engineering, UK, are commercialising an artificial intelligence (AI)-based sensing system to optimise fluid production.
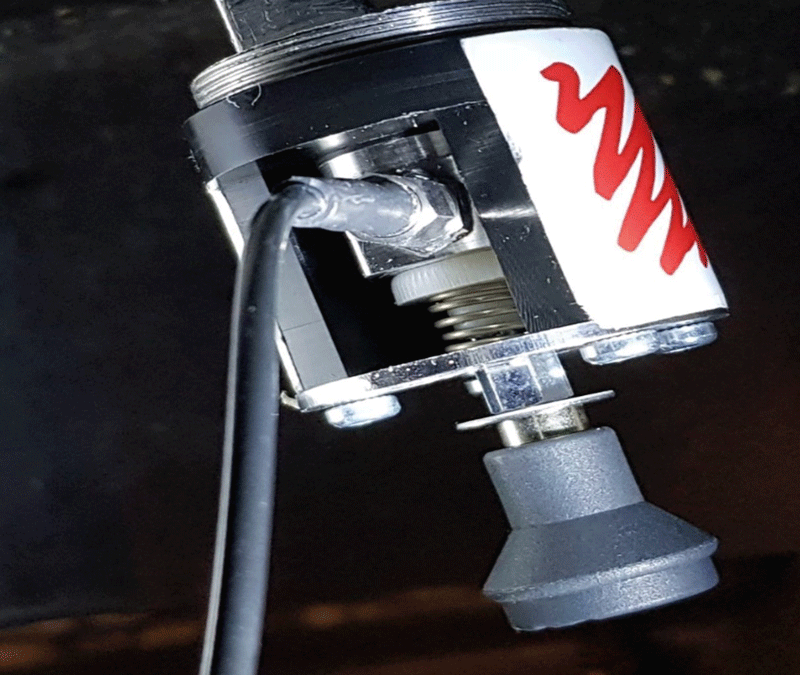
The aim is to enable manufacturers to monitor the inside of production pipes without having to halt the process.
The sensing system could help reduce power consumption and raw material wastage while also maximising throughput and product quality.
‘Hundreds of millions of tonnes of materials are wasted each year because of quality control problems,’ says Federico Alberini, Associate Professor at the University of Bologna, Italy, and one of the researchers who worked on the system.
‘Many fluid processing systems were designed 30, 40, 50 years ago and have not evolved to meet modern needs. Manufacturers are still taking batch samples at intervals to understand what is happening inside their fluid flows. It’s costly, difficult to control and it’s wasteful.
‘I saw there was opportunity to retrofit a technology to tell us what is happening in real-time, to provide in-line intelligence that will allow operators to continuously fine tune their systems.’
There are three components to the new system – a probe which is retrofitted to a pipe in manufacturing, a probe that transmits micro-vibrations generated by fluid flow, and a piezo sensor that detects the vibrations.
‘The signal is interpreted by our AI software so that we can extract information even in the presence of multi-phase flow,’ shares Alberini.
Rheality’s probe, he says, can be made from any metal material. ‘In fact, the beauty of our technology is its flexibility and adaptability. Usually, we can use the same material as the pipes that it is retrofitted to. All the materials are proprietary, their choice and is dictated by function.’
In addition to laboratory tests, Rheality has conducted field trials in oil and gas, food and chemicals. ‘We have deployed into production plants that process up to 250t/h of material, in very challenging environments – ambient temperatures from 40-60oC – as well as process conditions [that are] high pressure, >300 bar, [with] acidic, non-Newtonian fluids,’ Alberini describes.
Through these trials, the team reveals that it can identify the effect of changes in composition in real-time, whatever the fluid state and pipe diameter.
‘We are currently achieving a level of accuracy between 1-2%, and we can trace dynamic changes that occur in as little as one-tenth of a second,’ says Alberini.
Moving forward, the ‘technology is infinitely scalable. The sky’s the limit. And it’s ubiquitous, so it can be installed anywhere, even in complex pipe networks. Any fluid production system with an unknown variable or variables is an opportunity where we can introduce greater efficiency and profitability’.
Alberini adds, ‘Our aim is to bring a new level of efficiency, sustainability and profitability to industrial processes. We are currently operating in food, oil and gas, and chemicals, but can easily expand to other kinds of application. We can now monitor several process parameters, which was previously not possible, but has been made possible thanks to the effectiveness of our AI and the richness of the information we can gather.’