Advancing graphene’s applications
Professor Karl Coleman and Dr Adrian Potts of Applied Graphene Materials in Redcar, UK, on scaling up graphene’s use.
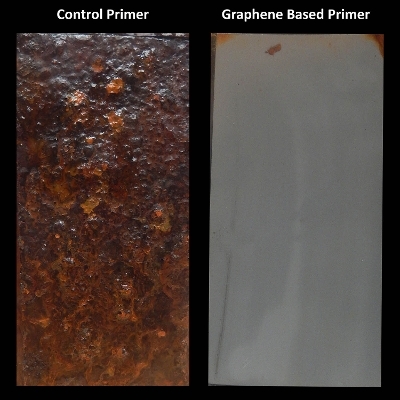
Example of well-dispersed graphene in a coating formulation for a commercial coatings system.
© AGMThe momentum behind global research in graphene in a variety of its forms has been substantial
since the pioneering work of its founders, Nobel Prize winners Professors Andre Geim and Konstantin Novosolev. But real-world applications have not developed at anywhere near the same rate. There are, of course, always challenges with integrating new and novel technologies and graphene is no exception.
The practical aspects of handling such a material and making it relevant for real life mean that alternate forms of the product offer perhaps a more practical solution to near-term application and commercialisation. Graphene nano-platelets (GNPs), for example, take advantage of some of the performance potential in combination with high aspect ratio and high specific surface area. In this platelet form, the material offers remarkable potential when used as an additive to enhance other materials technologies and opens the way to facilitating a ‘drop-in’ approach.
There are many opportunities for materials to be enhanced with graphene, including coatings – barrier, anti-corrosion and chemical resistance – composite materials and specialty high-thermal conductivity adhesives.
One of the key challenges with GNPs, however, is how to make them in volume and of a consistent format. There are two schools of thought on the approach:
- Volume exfoliation of bulk graphite – by various means including mechanical, thermal or chemical. The source materials in this process are key to quality and consistency of the resulting product, which is usually in the form of GNPs at a range of thicknesses and particle sizes.
- Bottom-up manufacturing – a more synthetic approach, whereby one builds the structure of the material from a carbon source by a thermal process.
Applied Graphene Materials plc (AGM), a spin-out company from the University of Durham, UK, predominately uses the latter approach.
Industrial capability
Process development of the bottom-up method has been key to ensure consistent quality at industrial scale. The key objectives of materials format include particle size and thickness, particle morphology and functionality achieved through laboratory to full scaling of reactor design and the capability to run materials continuously and to consistent quality. One material, A-GNP35, is made of a few atomic layers of carbon and the platelets, or flakes of materials, are tens of microns in the lateral X:Y dimensions. As such, the material has a very useful aspect ratio and specific surface area, which when combined with other attributes such as impermeability and conductivity, makes it a valuable addition to other materials that could benefit from these characteristics.
A key aspect of working with nanomaterials, and in particular graphene, is to enable the material to be used in a way that is helpful to companies developing higher performance end-user applications. Factors that come to mind are safety, dispersibility and the all-important discrete array of these tiny particles or nanoplatelets in the finished product to deliver the performance required.
The ability, or even desire, of a company focused on developing new applications to handle or formulate with nanomaterials is often assumed and this can sometimes hinder take-up or slow down developments. The important question of how to use them to good effect can be answered by working with a team of formulation experts. Delivering a fit-for-purpose dispersion of nanoplatelets that is in the correct media, with the appropriate chemistry to match the anticipated end-use is all important. Aspects such as particle size distribution and viscosity of the dispersion impact how the material is used in a production setting. Equally, knowing when to add a dispersion to a formulation also comes into play, for example, to avoid destroying the nanoplatelet structure as part of processing. Lastly, because of the efficiency of use often found with graphene materials, the loading level deployed can be very low. Balancing the addition of the dispersion with the rest of the formulation is critically important to determining successful outcomes.
In doing so, protective coatings are being developed based on the capability and know-how to disperse graphene platelets in a range of solvents, including water and common resins. It means graphene can be delivered as stabilised dispersions in a variety of matrices suited to end applications.
Key to coatings development is robust technology that can be further advanced to manufacture customer-specific dispersions with chemical compatibility to suit specific applications, particularly for anti-corrosion coatings.
Ultimately, to build on this, researchers across the community need to work with product formulators from the paints, coatings, composites and functional fluids industries to offer stable, dispersed graphenes that can be used in a controlled way by the end-user to deliver the required properties in commercial products.
Transformational performance
When a customer can take graphene dispersions and use them to great effect, the performance advantage can be remarkable. Banks of accelerated salt spray corrosion test cells, UV testing and electrochemical impedance testing as well as routine materials analytical equipment are typical of the supporting set-up to prove the efficiency of graphene as an additive, for example, for protective coatings technologies.
In the image at the top, we see an automotive, aerosol-format, acrylic, anti-corrosion primer, which routinely would be expected to last a few hundred hours in a prohesion salt spray test. With only 0.1% graphene solids added to the total formulation, delivered via a compatible dispersion matched to the chemistry of the coating formulation and with a particle size suitable for spray application, the paint system can endure 3,000 hours in the same test. Meanwhile, the graphene addition is sufficiently low to remain cost-effective and avoids upsetting the coating’s other properties such as mechanical robustness.
The upside is clear in terms of potential life extension of the coating through to an increase in maintenance period for the automotive owner. This model could be replicated on other infrastructure, cladding on a building or a marine application, for example.
Coatings to composites
Taking the substantial gains in liquid resins for coatings, there is also potential for matrix resin enhancement in composite materials. Already complex high-performance materials, composites often use a range of toughening mechanisms to enhance matrix-dominated attributes, and so it is quite challenging to further extend performance. However, adding graphene can enhance fracture toughness (G1c) in several composite types.
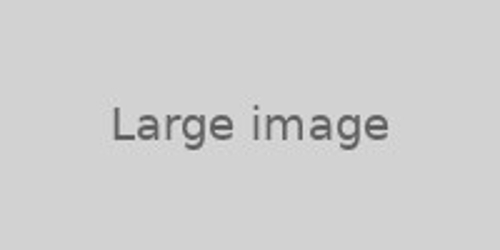
A small addition of GNPs through an appropriate dispersion – usually a component of the matrix formulation – reveals substantial uplifts in G1c – increases of 100% and more in a unidirectional carbon-fibre prepreg composite material. Allied to this, some recent customer-led applications developments have also seen improvements in
inter-laminar, flexural and impact performance which gives great confidence for wider use in this sector. This success is a direct result of the quality of GNP dispersion into the end materials, and there is a direct correlation to the quality of the dispersion supplied.
Moving forward, we are pursuing printing graphenes with compatible resin systems into composite laminates to boost matrix fracture performance precisely where it is required. This would seem to be a natural extension to the increased use, for example, of automated tape placement in composite manufacturing and may lend itself well to printable applications elsewhere.
Similar performance enhancements have been seen by customers in the world of aerospace adhesives, whereby thermal conductivity in tandem with low density delivers high specific performance. Supplied in this case as a two-part epoxy adhesive, the graphene is added to enable excellent heat transfer through the adhesive while also achieving good specific performance – important to weight-saving applications.
There is also scope to enhance Type V linerless pressure vessels for space applications. Cycling such cryo structures down to -300°F and to 600psi is a true test for the consistency of the graphene-containing composite materials products. The images on the page opposite show the structure at room temperature (left) and during the environmental cycling test (right).
2020 is a challenging year in many industries so far. Supplying materials solutions that have been demonstrated to work with clear user guidance and advice is important in this emerging market.
Lab bench to supermarket shelf
Applied Graphene Materials Founder Karl Coleman on graphene’s evolution and his own journey from laboratory to commercial enterprise.
What we are seeing now is that the over-inflated expectations have dissipated and the benefits from graphene as an additive in many different areas, particularly coatings and composites, can be seen.
What has struck you most in your journey from working with graphene in academia to scaling the material up for industry?
When AGM was formed, graphene was in its infancy and researchers were only really starting to discover the properties and how they could be used. The year AGM started, Andre Geim and Konstantin Novosolev were awarded the Nobel prize for Physics and graphene was catapulted into the imagination of the public. For me, it was about producing graphene on a scale where we could start to put it into something and test some of the material properties. This involved building the first large reactor in my labs in the Chemistry Department at Durham University, something we had never done before and seeing the finished design working was very satisfying.
I also learnt a number of new skills and started to think more about some of the chemical engineering challenges that needed to be addressed. It still excites me today to walk into the AGM production facility in Redcar and see how the design and methodology has changed over the years, and the size of the facility and production effort is awe-inspiring. What I have really enjoyed over the years is talking to a variety of people from engineers, chemists, application specialists to business development experts. Each person’s perspective on the important challenges facing graphene and its commercialisation have been different and thought provoking and I have truly learnt a lot.
Being an academic I found this very revealing and it has helped me think about my university research in a very different way. The proudest moment for me was being able to walk into a high street store and buy a product that contained AGM graphene. It is very rare for an academic to see something developed in their own lab sat on a shelf for people to buy.
Graphene has taken time for its promise to be realised. Why do you think that is?
Although research efforts in graphene have grown rapidly over the last decade or so, we are only now really starting to see applications come through. I fear the answer is multi-faceted and the first thing I would say is that given the unsurpassed properties of graphene and the hype generated, perhaps the community was too quick to embark on a quest for a so-called 'killer' application that was unique to graphene. This was a great aspiration but ultimately it comes down to market push or technology pull and there was no commercial grand challenge waiting for graphene to solve at the time, that’s not to say it won’t be there in the future.
What we are seeing now is that the over-inflated expectations have dissipated and the benefits from graphene as an additive in many different areas, particularly coatings and composites, can be seen.
Often multiple material properties are improved all at the same time rather than an individual property, which is typical for other additives. This is a step change and has now started to push forward the adoption of graphene in commercial products and deliver on the expectations.