A shoe in? Can the global trainers industry be more sustainable?
Researchers from Queen Mary University and the University of the Arts London, UK, put trainers through their paces.
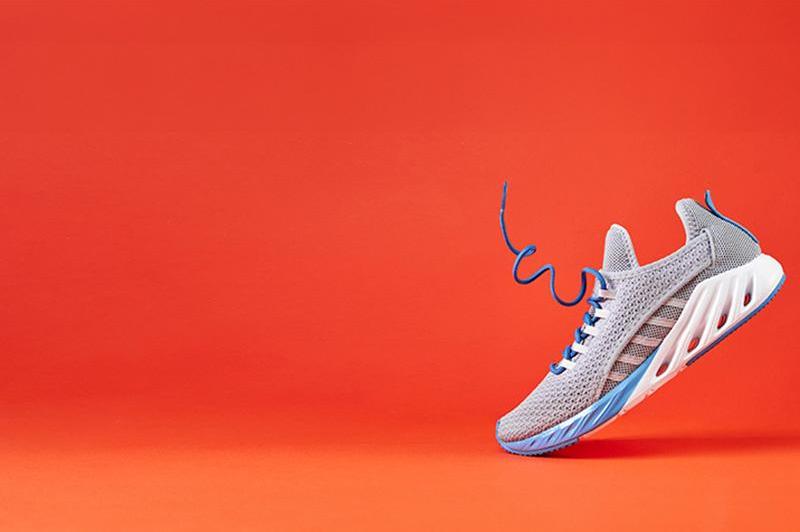
How many people are wearing trainers on the train to work? According to Shoeaholics, trainers are being worn to the office by two out of three Britons.
Environmental charity Global Action Plan estimates that one-in-10 teenagers has at least 10 pairs of trainers, and one-in-50 has 20 pairs or more. An additional study from them estimates that British teenagers own six pair of trainers, on average.
Their popularity has increased at an unimaginable pace. According to online platform Statista, the worldwide value market of these products is expected to reach US$91.66bln by 2024 – 10 times more than the value of the luxury watch market. But are there any collateral effects caused by the increased demand for these products?
One of the reasons why trainers are regularly chosen by consumers for daily activities is comfort. This is provided by a combination of materials and design.
Flexibility, breathability, durability, stiffness, and resistance to tear, slip and water are important attributes provided by the mechanical properties of the materials.
Careful selection is needed to ensure the effectiveness of the materials chosen for specific purposes. Different materials can provide us with different properties. For example, elastomers provide flexibility, metals provide strength, and polymers are both lightweight and durable.
Therefore trainers are built using a large number of materials. A study by researchers from the Massachusetts Institute of Technology (MIT), USA, titled Manufacturing-focused emissions reductions in footwear production, in the Journal of Cleaner Production, estimates that a pair of running shoes require 65 individual components and approximately 26 different materials. Depending on aesthetics, brand and technicality, 10-30 materials are used on average, the majority of which are derived from synthetics.
Running full steam
Trainers are composed of two main parts. The upper part, which is integrated by the toe box, the upper, shoelace, tongue, lining, padding, collar and heel counter; and the lower part, comprised of the midsole and outsole.
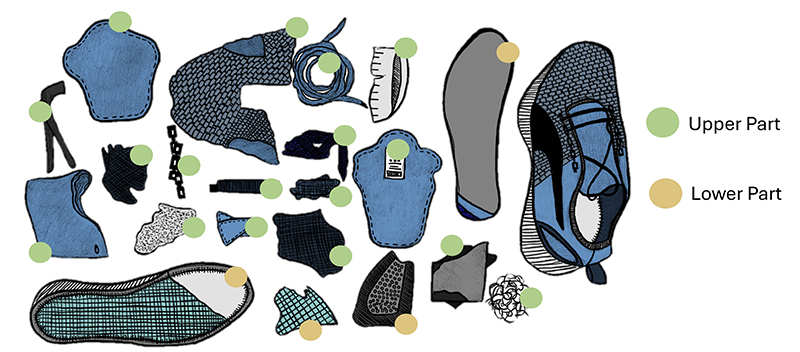
The upper part is meant to protect the superior part of our foot. It requires the materials to be soft, flexible and lightweight, while being resistant enough to shelter our feet. The most common materials used are leather, synthetic leather, cotton, polyester, polyamide, polyurethane (PU), elastane and PVC.
These materials fulfil a specific need for the parts they are employed for. PVC is applied on the heel counter to provide structure and support, while elastane is used on the lining to allow the fabric to stretch, facilitating movement.
PU and polyester are applied in the uppers because of their light weight and durability, making them suitable for a part that is in constant contact with our feet.
Leather and synthetic leather are used to provide a good fit, facilitating comfort. Additionally, designers and manufacturers have concluded that lightweight trainers have better performance.
Conversely, the lower part requires materials that can be resistant enough to avoid falls, provide stability and protect us from water and soil. These parts are required to be comfortable for our soles while providing security. Materials employed are rubber, ethylene-vinyl acetate (EVA), thermoplastic PU and PVC.
Rubber provides flexibility for the outsoles – a part that is in constant movement and friction with the ground. It is also lightweight and durable while bringing support.
EVA is applied on the insoles because of its shock-absorption properties, user comfort and light weight. Studies show the importance of materials like EVA to avoid injuries for runners and walkers.
Examples include, Immediate effects of EVA midsole resilience and upper shoe structure on running biomechanics: a machine learning approach submitted to PeerJ, and Running injury paradigms and their influence on footwear design features and runner assessment methods: A focused review to advance evidence-based practice for running medicine clinicians in Frontiers in Sports and Active Living.
Testing and research organisations evaluate the mechanical properties of the materials used in footwear products. This allows accuracy and credibility on how functional shoes are, providing a deeper understanding of the needs and challenges in selecting materials for footwear.
Keeping up the pace
Trainers therefore demand a high number of processes and steps to be produced. Researchers at MIT estimate that assembling a pair of trainers requires more than 360 steps.
Manufacturing can be divided into four main stages:
- Preparation
- First stitching
- Hand stitching
- Assembly
For the first stage, the trainer parts are prepared. The textile-based components, such as the tongue, the upper, the lining and the padding, are cut. First stitches to join the layers are made and labels are added at this point.
At the second stage, the first stitching process assembles the larger upper part elements by placing them as layers.
Flat stitching is the typical technique used due to the resistant stiches it provides to the upper part.
On the third stage, hand-stitching finishes the assembly of the upper part for better management of the production. It is important to mention that, while the stage is called hand-stitching, the components are stitched by machines but mostly manipulated by operators.
Finally, the assembly stage joins the upper with the lower part. The trainer is put into a shoe last to confer its final form, and a direct injection technique is applied to mould the sole into the uppers. The upper part is then stitched to the insole using the Strobel technique. Eventually the shoes are carefully inspected.
Tracking your run
This intensive production line has a negative environmental impact. According to the Environmental Impact of the Global Apparel and Footwear Industries Study by consultancy Quantis, the footwear industry is responsible for 1.4% of global greenhouse gas emissions – equivalent to 700Mt of CO₂. These come from the manufacturing and extraction of the raw materials needed for production.
Researchers have found that, on average, manufacturing a pair of running shoes generates 13.6kg of CO₂e, the equivalent of keeping a 100W lightbulb on for a week.
Another concern is the impact at the end of their lifecycle. There are a lot of adhesives used in the assembly operation and this makes potential disassembly for recycling difficult, meaning they end up in landfill. Trainers cannot disintegrate quickly either because of the high percentage of synthetic materials.
However, different approaches have been taken to decrease the environmental footprint. The World Footwear 2030 report predicts that sustainability is the key factor that will drive innovation in the footwear industry and will lead consumer decisions and habits.
By rethinking the materials and manufacturing techniques, we can start implementing innovative technologies and recyclable materials to introduce circularity into the supply chain.
One more step
But how can this be tackled? Can the number of components within a trainer be reduced without compromising their functionality and performance? Is it possible to have one or two materials to provide all the mechanical properties needed?
Manufacturing starts with design and the material selection. Looking at these two aspects is the first step towards a more sustainable journey.
Hybrid materials allow a single material to have a much wider range of properties. This means that a single polymer could be extruded and drawn to create fibres that are much stiffer and stronger than the base polymer, or the polymer could be foamed to create a material that is much less stiff.
Thermoplastic elastomer materials are a good fit due to their versatility to be moulded or extruded, making it easier to be designed and produced in a variety of ways.
Their properties, such as good tear and abrasion resistance, excellent resistance to chemicals, high elasticity, and high recyclability make them good candidates.
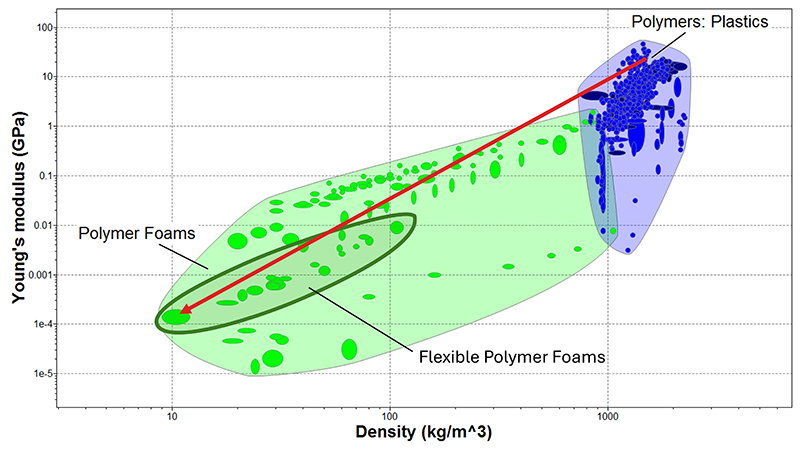
The FutureCraft Loop, created by Adidas, is a running shoe billed as 100% recyclable, made of only thermoplastic polyurethane. This trainer has demonstrated the versatility of materials and how they can be applied for different purposes within the same product, increasing the use of recycled materials and reducing the extraction of raw virgin materials.
Furthermore, other strategies implemented by different companies include the use of bio-based and recycled materials, handcrafted techniques, environmental standardisation of the manufacturing processes, repairability workshops for consumers, trainers designed for repairing/disassembly and recovery schemes for recycling.
Bio-inspired techniques in textile design are also a useful tool to start designing and creating with circularity in mind. Designers and researchers have indentified nine bio-inspired structures – fibrous, helical, texture, cellular, tubular, overlap, gradient, layer, and suture – to design for efficiency, longevity and recovery (see image below).
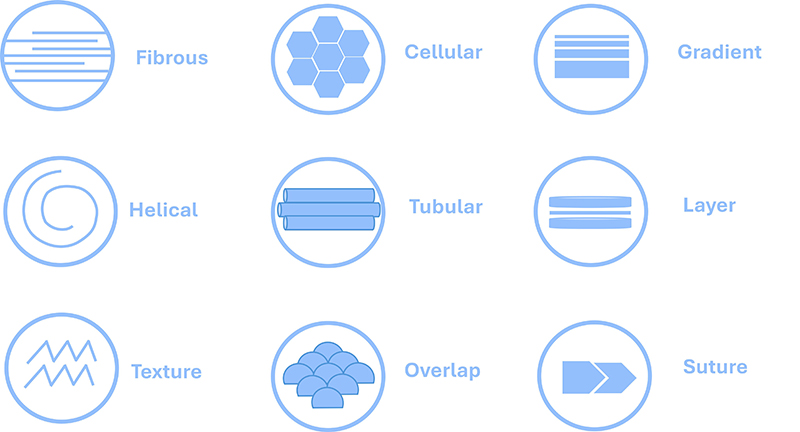
Bio-inspired design structures
© Kapsali and Hall (2023) Bioinspired Textiles; Observations from the Evaluation of a Novel Practice-Based Framework Linking Lessons on Sustainable/Circular Design from Biology to Textile Practice. Journal of Textile Design Research and Practice, doi: 10.1080/20511787.2023.2240062. creativecommons.org/licenses/by/4.0
Helical structures can create reinforcement for example, cellular structures can generate 3D constructions that provide reduced stiffness and lightweighting, while overlapping structures allow the materials to bend even if they are stiff in tension.
Gradient structures offer multiple properties by adjusting the ratios of the same components, texture provides protection against erosion and stops agents sticking into our materials, and fibrous and tubular structures provide strength.
Using such structures allows the basic range of properties for a given material to be greatly expanded and are already applied in textiles materials, for example, through 3D weaving, multilayered structures and nonwovens.
Consequently, if we can then provide a single material with the properties we need, then we can reduce the number of components in a product, increase its recyclability, facilitate its disassembly, and reduce its environmental footprint during the lifecycle and at the end of it.
Bio-inspired structures can also be constructed by 3D printing to further reduce the number of manufacturing steps, facilitating its recyclability.
A recent study made at MIT highlights the beneficial use of 3D printing in providing a much wider range of properties, while brands such as Adidas, Reebok and New Balance are introducing 3D-printed elements in their designs.
Step on it
The environmental footprint of trainers is increasing with growing use and their production needs to adapt with the times. A wider perspective and a better understanding of new technologies can make these sustainable changes a reality and form a novel way of manufacturing the next generation’s must-have accessories.