A ray of light - laser welding copper
Ralf Egerer at Nexans cuts through the challenges in welding copper.
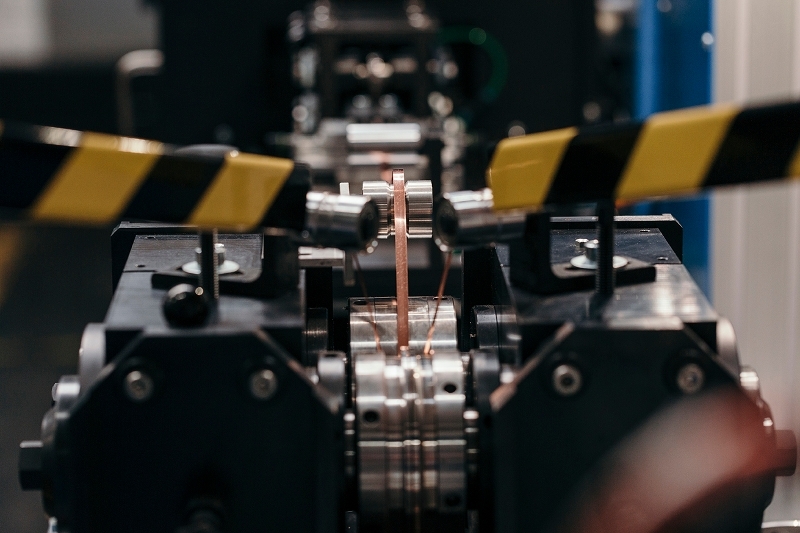
For the past 30 years, laser welding has been used in a variety of manufacturing processes, being precise, fast and suitable for automation. However, using lasers to weld copper has historically presented a major challenge.
CO2 lasers were the first type of laser to be used in welding, particularly in stainless steel. However, while they are effective, they have issues in terms of energy efficiency.
Laser welding has since advanced to solid-state technology, for example disc lasers. However, even these face challenges when it comes to welding materials such as aluminium and copper. This is due to
their low-energy transfer efficiency – the ratio of the laser output energy to the energy absorbed by the material. In some cases, only 10% of the laser energy directed at the surface will result in heating, and the high thermal conductivity, of copper in particular, means the heat rapidly flows away from the weld area.
This low absorption of laser energy is due to the high density of free electrons in the solid metal, which is the main reason why aluminium and copper are good reflectors of light. However, there is another critical factor at play, which is the laser wavelength used for welding. Here, the absorption of laser energy becomes more efficient as the laser wavelength decreases.
The infrared solid-state lasers commonly used for welding usually have a wavelength of 1,030nm. In contrast, a ‘green’ laser has a wavelength of 515nm and a ‘blue’ laser has a wavelength of 450nm. The shorter wavelength enables significant improvements in their ability to laser weld copper.
The cutting edge
The first blue laser had a power of 150W and introduced the ability to laser weld copper at a thickness of 80µm. Modern green lasers work at 1kW and the state-of-the-art function at 2kW, which promises to greatly increase work capacity.
Cutting edge blue and green laser technology can be implemented into machines in manufacturing lines for a range of applications. For example, the manufacturing of cables, continuous tubing, heat exchangers and medical needles.
Another major advantage is their ability to function on multiple materials at a range of thicknesses. Traditionally, only thin steel sheets have been welded by laser, whereas Tunsten Inert Gas welding (TIG) was the tool of choice for copper and bronze. The introduction of the 1kW green laser enables continuous welding of thin-walled, long-seam welded copper geometries at the same quality level and speeds as infrared lasers offer in stainless steel applications. While gaining the ability to take on copper, green lasers remain just as capable as infrared lasers in stainless steel applications.
A fair exchange
One key market that the technology addresses is the manufacture of heat exchangers. These units use large lengths of welded copper tubing to dissipate waste heat in various applications. Due to the increased capability of automated machinery with blue and green lasers, copper can now be welded at a much thinner wall thickness, helping to reduce the amount of copper needed per unit. As a result, the heat exchanger market is seeing significant cost savings and improved performance and reliability.
On the same wavelength
Some blue and green laser machinery can now weld different materials at different thicknesses. This is because the wavelengths of blue and green lasers are absorbed more easily by different materials, enabling a more energy efficient welding process.
Copper with a wall thickness of 0.3mm, for example, can be welded at 6m/min using an 8kW red laser, but only around 3-10% of the laser power is actually absorbed. The rest of the laser’s energy is reflected, and the welding process is unstable, producing an inconsistent and variable weld seam. Copper’s strong reflective properties also result in a significant delay before the welding starts to take place, allowing bubbles to form.
In contrast, copper absorbs as much as 70% of the power of blue and green lasers, allowing lower power lasers to be used for the same outcome, saving energy. The welding task described above can be fulfilled by a 1kW green laser, with significantly greater stability and a higher quality seam. Furthermore, the absorption of the green and blue laser is less sensitive to the surface quality of the copper strip, ensuring higher quality weld seams regardless of the strip’s finish.
The core of the matter
In the cable industry, we use laser welding to create the protective sheeting. This can be done with the cable core in place, or without, as some customers prefer that the cable is inserted into the tube at a later stage.
For heat exchangers, we are seeing that more and more companies are interested in using laser welding to create prototypes. Typically, copper tubes with wall thicknesses of 80μm can withstand pressures up to 120bar. However, some of the latest machines are able to form and weld thicker tubes to create tube designs that can withstand upwards of 200bar.
Some laser welding machines can also be used for longitudinal welding to form long pipes by welding over the full length. To reach long continuous longitudinally welded cable designs – longer than the initial coiled strip material – multiple coils of the same strip width can be connected with an automated cross-welding machine. Carrying out this process manually would take around 10 minutes – to cut the strips, position them precisely and weld them by hand. With the Unicross machine this is done automatically in just one minute. Additionally, using this technique, cable lengths of an astonishing 120km can be achieved.
Blue and green laser welding technology is still in the early stages of commercial application, but it is already clear that it will allow us to realise heat exchanger designs and manufacturing processes that were not possible before. The aim is to optimise production of thin-walled copper tubes and finned tubes. Here, tests are currently being carried out under industrial conditions with a 2kW green laser. This will also be used to produce Fibre in Metal Tube products with a length of up to 100km. This allows thin-walled copper to be formed and welded on the same machine as stainless steel and aluminium efficiently.