A hydrogen-powered train
The UK’s first mainline hydrogen fuel cell powered rail vehicle is being developed by a collaboration between Porterbrook and the Birmingham Centre for Railway Research and Education. Stuart Hillmansen and Helen Simpson introduce HydroFLEX.
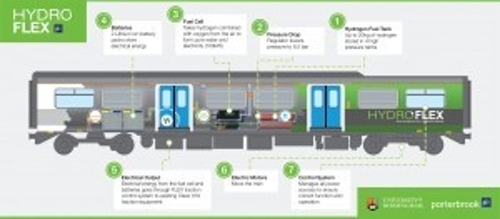
UK railways have made use of infrastructure-based power supplies for almost 130 years. This started in London in 1890 with track-based electrification and then in 1983 overhead electrification followed on the mainline. Today, much of the heavy-duty intensive and high-speed routes are fully electrified with the vast majority of passenger journeys provided by electric propulsion systems. There is now a mixture of overhead electrification, mostly AC but some DC, as well as third and fourth rail DC. Long before recent concerns regarding climate change, electrification was seen as the most effective engineering technology–led solution for delivering traction power to trains.
In recent years, the country’s electrification programme has seen its development along the Great Western route, as well as a number of other schemes. The high costs, and often delays in delivering these projects to a budget and on time are in part due to the highly complex engineering challenge in providing this new infrastructure. In fact, electrification of existing routes often renews most of the exiting railway system, and is not simply an exercise in installing wires.
Much of the railway is still not electrified, and is unlikely to pass the economic case for full electrification at any point in the future. These routes are often in rural locations, and they serve a vital role in local transport, as well as serving as feeders into the trunk part of the network. The vehicles that currently operate these services are diesel multiple units – they emit carbon dioxide at the point of use, as well as other gases and solids which if not collected by an exhaust after treatment system, can affect passengers using the train service. There is societal pressure to fix this problem, and the industry has recently been mandated to remove vehicles propelled only by diesel by 2040. This date is significant because it demonstrates that the industry takes the 2050 target of zero-net carbon seriously, but it is also significant because a new vehicle today would be expected to see service well beyond 2040. This means the industry has to find solutions to achieve zero-carbon and zero-emissions as soon as possible.
The Birmingham Centre for Railway Research and Education (BCRRE) has been investigating technologies suitable to provide autonomous traction, with zero emissions at the point of use for a number of years.
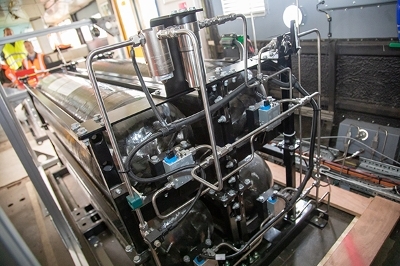
This work started in 2003, and since then has progressed from desktop studies, simulation and software development to emulate the systems, to practical testing at scale in the IMechE railway challenge, and most recently the HydroFLEX project.
Hydrogen power
The centre’s research has shown the best candidate to provide traction power to replace diesel multiple units is a combination of hydrogen fuel cell and battery technologies. Each of the sub-systems involved in creating the HydroFLEX train depends on advances in recent decades in the understanding of material science.
The fuel cell used in the HydroFLEX project is supplied by Ballard and can provide an output power of 100kW. The cell uses hydrogen, which is combined with oxygen present in the atmosphere to generate electricity through an electrochemical reaction. The hydrogen gas is kept separated from the oxygen using a membrane, which is coated with a platinum catalyst that enables the hydrogen molecules to split into H+ ions and electrons. On the other side of the membrane, the oxygen molecules also undergo a catalytic reaction and form negatively charged oxygen ions.
Therefore, there is a strong attraction between the H+ and O- ions across the membrane. The membrane allows the H+ ions to pass through and combine with the oxygen ions and electrons, creating water. The electrons, which were produced on the anode, also need to get to this side of the membrane as they are conducted from the anode through an external circuit before arriving at the cathode to form the water. The membrane itself is a highly complex piece of engineering which draws upon decades of material science research.
A fuel cell creates electricity directly, and there is no combustion, and therefore fuel cells can achieve a high efficiency. They are also quiet in operation and low maintenance. However, perhaps the most significant reason for using a hydrogen fuel cell is that the hydrogen can in theory be produced from renewable electricity and be decoupled from fossil fuels.
The research team at BCRRE has familiarity with a number of fuel cell formats and their operation. From a systems viewpoint, it is possible to treat the fuel cell as a black box and run it properly using the known system characteristics. It typically has a number of key interfaces, foremost is the hydrogen supply point, which takes 8.5 bar gas from the high-pressure storage via a gas regulator. Then there is the electrical power output connection, and the air intake which uses the oxygen in the atmosphere to combine with the hydrogen to produce the electrical energy. The fuel cell produces unwanted heat that needs to be removed through a cooling system. This heat can be used for saloon heating in colder months. Finally, there will be some control and communications interface connected to the vehicle.
Storage space
Hydrogen storage onboard the vehicle is the next part of the puzzle. Hydrogen is a very light gas and the molecules are very small, which means storing enough of it to give the vehicle meaningful range is a challenge.
The most mature and arguably promising technology for this is to use compressed gas. High-pressure tanks with aluminium liners and carbon-fibre wrapping are the most common solutions currently available. These are the same as the tanks used on the HydroFLEX project and were supplied by Luxfer. The pressure the gas is stored at is up to 350 bar, and we store 20kg of hydrogen on the train.
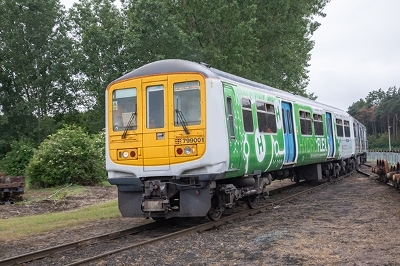
However, the tanks are rated far higher than this to enable a fast fill, which will take hydrogen gas at high pressure and decant it into the tank. Because of the negative Joule-Thompson effect, which is present for hydrogen gas at normal temperatures, the gas that is expanded into the vehicle tank increases in temperature. The temperature can rise, and the pressure be above 350 bar on the initial fill, returning to 350 bar once the gas has cooled. The mass and volume of the tanks give good energy storage, but fall short of what can be achieved in a diesel tank. This means a fuel cell train will likely have a smaller range than an equivalent diesel vehicle.
Another promising technology for hydrogen storage is in advanced solid-state systems. Metal hydrides and other exotic materials can be used to store hydrogen and it can achieve very high volumetric efficiency. The density of the materials used in this process is usually quite high, which could be a problem for passenger rail vehicles, but a virtue for freight locomotives that need a high vehicle mass in order to generate sufficient tractive effort to haul their loads.
It would be possible to develop a fuel cell only train, but if the system is hybridised with a battery, then the power rating of the fuel cell can be reduced, and the battery can be used to absorb braking energy through the regeneration system.
The HydroFLEX project uses lithium-ion batteries from Denchi Power, which are rated at 650V and can provide or sink 220A. These batteries are connected directly into the existing traction system on the train, and the Ballard fuel cell can be controlled to deliver a variable amount of power depending on the battery state, and the traction demand. During periods of high power demand, both work to provide the traction demand, and then at other times the fuel cell can be run at a nominal load to follow a charge sustaining strategy.
The donor train, a Class 319 example, has four vehicles, one of which contains all the traction equipment. Such models are still in service on some of our routes, but many of them are no longer on lease. Unmodified, the locomotive can take power from both overhead and third rail electrification systems, and has series wound DC traction motors, which are controlled using gate turn-off thyristors. A traction system is not configured to use regeneration during braking, and therefore we are unable to use this energy to recharge this vehicle’s batteries.
HydroFLEX’s total available traction power is much lower than the original train, but the installed power and energy will give sufficient performance for mainline testing. Additionally, the concept for the traction system is highly modular, and upgrading the system with more powerful components would be straightforward from an engineering point of view.
Porterbrook has experience of reengineering these trains and has introduced a bi-mode diesel version. This vehicle has two diesel generation sets at each end which feed power into the locomotive’s DC power bus. A great deal of work has already been done on understanding how to interface a new power source into the original traction system, and the HydroFLEX project benefited greatly from this knowledge.
The team was tasked to deliver the project in nine months, in a partnership between BCRRE and Porterbrook, linked through the UK Railway Research Innovation Network. Porterbrook provided the donor vehicle, and using their experience of previous traction modification projects on this type of vehicle, the team rapidly developed a concept design, and move through to detailed design, fabrication and building phases.
The finished train was demonstrated in June 2019, and has since undertaken several test runs at progressively higher powers and speeds. It can now operate at 40km/h which is approaching the speed limit on the available track.
The main items of equipment for the system are housed in a single vehicle on the train, which already contains all the propulsion equipment. These were fitted in the passenger space after the existing seating was removed. The traction power and control cables were routed through the floor and other cabinets to the existing train systems.
As part of the design there were minimal changes required to the driver cabs. Fitting the equipment in the train in the manner achieved two goals – firstly, the equipment was easily accessible for the install and initial commissioning, and secondly it enabled the team to showcase the technology. Visitors were allowed to view each of the main systems and tour the hydro-chamber. This educational piece was a vital part of the overall project mission to demystify any issues visitors may have regarding hydrogen fuel cell technology.
Mainline operation
The project has received a considerable amount of interest and the team is now preparing the vehicle to operate on the mainline, with funding support from InnovateUK. This involved following railway approvals processes to enable the vehicle to operate on Network Rail’s infrastructure. HydroFLEX will start serving the public in early spring 2020.
There is a growing interest from the industry to develop hydrogen technology for the railway, and our partnership is by no means the only team working on this. Organisations such as the Railway Safety and Standards Board are also engaging in work to facilitate the introduction of hydrogen as a viable fuel into the rail industry.
HydroFLEX presents the first iteration of a fuel cell vehicle on the UK mainline network, and there are likely to be more following soon. Importantly, the team is also working on the fuelling infrastructure with its partners fuel cell systems to make sure that we develop this in parallel with the rolling stock.