A concise history of enamel
The word enamel comes the High German word 'smelzan' later becoming 'esmail' in Old French. Hence the current usage of 'smalto' in Italian, 'email' in French and German and 'enamel' in English.
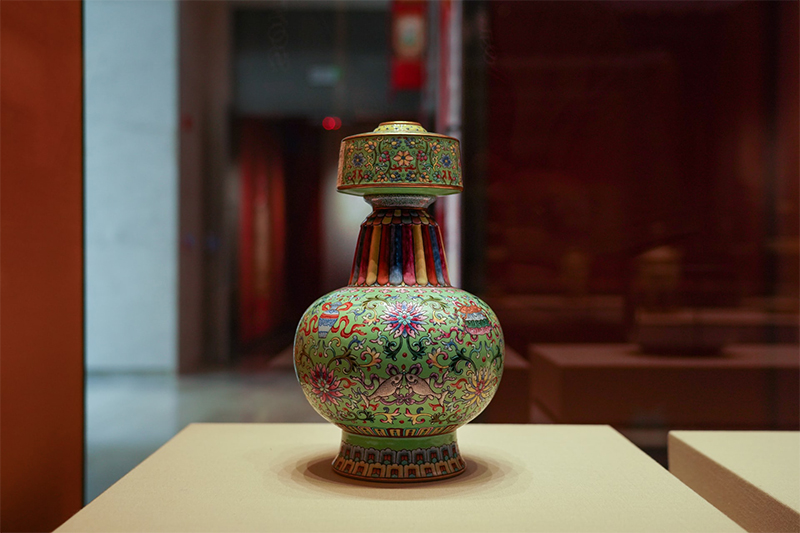
It is thus defined as a vitreous, glass like coating fused on to a metallic base. In history, enamels were initially applied on firstly gold, then silver, copper, bronze and more latterly on iron and steel. The term is also used for the application of decorative fusible glass applied to glass objects.
The earliest known enamelled objects were made in Cyprus in around the 13th century BC during the Mycenæan period. Six gold rings discovered in a Mycenæan tomb at Kouklia were decorated with various vitreous coloured layers fused on to the gold.
Earlier decoration of metal objects with glass, along with other materials such as precious and semi-precious stones, such as those found in the tombs of ancient Egypt relied on cementing the glass to the metal or a mechanical fixing by clasps. It was not until this unknown craftsman in Cyprus discovered that by fusing the glass on to the metal that the art of vitreous enamelling was born. The rings are chased gold, with an ornamentation of twisted square wires and it is almost certain that the glass was laid into the cells as very carefully cut pieces. These together with a gold sceptre and orb decorated with white pink and green are the earliest known pieces of enamel and can be found in the Nicosia museum in Cyprus.
This was the forerunner of the development of the Cloisonné technique for enamelling, where strips of gold, silver, copper or brass are attached to the metal base to form a network of small raised cells to form a border into which the enamel is laid, often as a paste. The final thickness is built up in layers with intermediate firings. In this way the ‘cloisons’ (the cells) prevent diffusion of the colours of the enamel and also give the mechanical adhesion of the enamel. When the enamel thickness is complete the cloisons are only visible as a fine network within the enamel. The final process involves grinding to smooth the enamel level with the tops of the cloisons and a polish to bring out the true colours and finish.
Cloisonné techniques pre-date enamel to 4000 BC and was employed as a method of setting semi precious stones into jewellery by cold cementing. This was used widely by the ancient Egyptians, one of the most famous pieces being the gold mask of Tutankhamun, which may look as if it is enamelled, but in fact it is not - the artist has used this early cloisonné method. Filigree work is a development of this technique.
Unfortunately there are only a few remaining enamelled relics from this very early period. It is likely that the craft spread to the ancient Greeks and via them to Europe. A 5th century BC Greek hair ornament shows remarkable skill, decorated on to gold and silver. Shield shapes around a lion’s neck are enamelled. This piece is in the museum in Birmingham. Apart from a very few pieces such as this, the Greeks are not well known for their enamels.
When Caesar conquered Britain, he found that the Celts were already using enamels and many examples of this early craft are in museums all around the British Isles with some very good examples in the British Museum. There is a mirror in Gloucester museum found at Birdlip in Gloucestershire with red enamel. They had used the champlevé technique, where a recess in the metal, either produced by casting, chasing or engraving is filled with opaque red, blue, white and green enamel. The enamel is polished flush with the divisions formed by the edges of the cells. The later Saxon hanging bowls found in the Sutton Hoo boat burial are some of the finest early champlevé work.
In the 9th Century AD Cloisonné technique enamels moved back into the Middle East in Byzantine Constantinople and a century later into Russia. The Byzantine style continued until the 12th Century and usually comprised small thin pieces of gold, which were set into much larger objects. One of the finest is an 11th century plaque of St Paul, which is in the Victoria and Albert Museum. Some two centuries later the Rhine, Meuse and Limoges areas were already producing some of their best work. The Limoges area also produced enamel work by the champlevé technique, continuing well into the 14th century AD.
A newer technique was developed in Italy in the 13th Century. Known as Basse-taille a translucent or transparent enamel is applied over a low relief, sunken or intaglio design, usually in gold or silver. The earliest known reference to this is in 1286 but the earliest known piece dates from 1290, a gold chalice made for the Convent of St Francis of Assisi.
The collections of the great cathedrals and churches account for the survival of these early works. A rare piece known as the King’s Lynn Cup or sometimes as the King John’s Cup is on display at King’s Lynn. It has been much restored over the years, but it originally dates to 1325 and is almost certainly the output of an English workshop. The Royal Gold Cup of the Kings of France and England was certainly made in Paris in 1380-1390 and may be found in the British Museum, where it is one of the most important treasures. This piece, although restored and added to, still shows the original colours as vibrant as the day that it was first fired. It is one of the best examples of the durability and longevity of enamels.
By the 15th Century the skills of enamellers were gaining in complexity. The earliest known use of the plique-a-jour technique was in the 13th Century. The technique involves the use of translucent or transparent enamels fused to form a span across a network of cells, without a backing under the enamel. The enamel is thus the structure of the piece – a shell supported within the network of metal cells. It is similar to cloisonné but without the base support. Often a temporary backing is used to support the enamel during the firing and then it is removed by dissolving or polishing when the piece is complete. This is undoubtedly the most difficult technique of enamelling, but the results can be very spectacular. The silver gilt Mérode cup in the Victoria and Albert Museum dates from the 15th Century and is thought to be of Flemish or Burgundian origin. It is the only known piece of plique-a- jour from this early period.
The Limoges area of France, already well skilled in Champlevé techniques, adapted the skill developed by the Venetian glass makers of painting enamels onto glass by painting enamels onto metals. This technique, adopted in the 15th Century, did not require the complex divisions or engraving and led the way forward to a method which with only slight modifications is still used by art enamellers today.
Until the 18th Century nearly all enamelling involved the production of works of art and religious artefacts.
Enamel work of these early eras is now highly valued and later names such as Faberge and Battersea became synonymous with the special appeal of vitreous enamel.
The first enamelling of iron is thought to have taken place in Germany in the 18th Century and by the end of the century, production of enamelled cast iron cooking vessels was being carried out. By then, enamelling of sheet iron was already taking place in Sweden. The Industrial Revolution drove forward the quality of this first adventure into industrial vitreous enamelling and by the mid 19th Century enamelled cooking vessels were commonplace.