A 3D-printed electrospray engine for CubeSats
The first fully 3D-printed, droplet-emitting, electrospray engine has been developed at the Massachusetts Institute of Technology, USA.
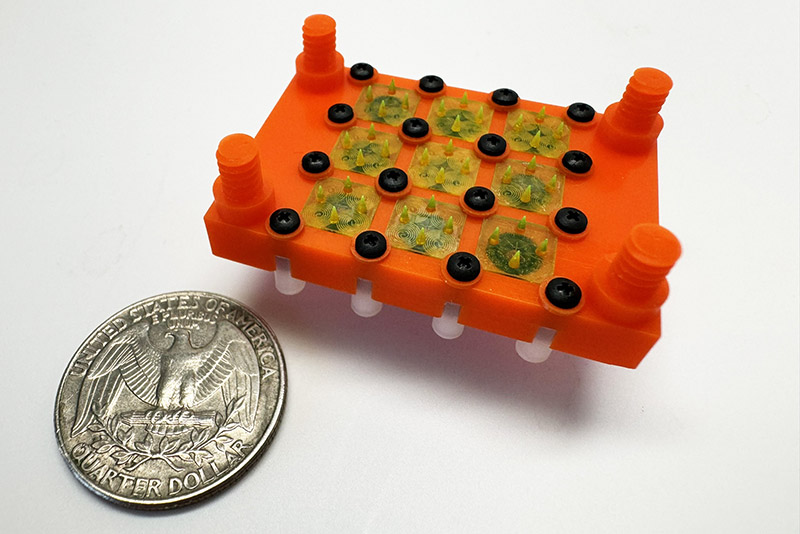
MIT engineers have demonstrated the first fully 3D-printed, droplet-emitting electrospray engine. The device, which would be ideal for enabling small satellites to make in-orbit manoeuvres, can be produced for a fraction of the cost of traditional thrusters
© Courtesy of the MIT researchersThe researchers say that the low-cost device can be fabricated more quickly than traditional thrusters, potentially from on board a spacecraft. It could enable CubeSats to perform precise, in-orbit manoeuvres, aiding space research projects.
An electrospray engine applies an electric field to a conductive liquid, generating a high-speed jet of tiny droplets that can propel a spacecraft. These miniature engines are thought to be ideal for small satellites called CubeSats that are often used in academic research.
Electrospray engines use propellant more efficiently than powerful, chemical rockets from a launchpad. The thrust generated by an electrospray emitter is tiny, so the engines typically use an array of emitters that are uniformly operated in parallel.
However, these are typically expensive and time-consuming to make via semiconductor cleanroom fabrication, which limits manufacturing and application.
The MIT proof-of-concept engine combines two types of vat photo polymerisation printing (VPP). This involves shining light onto a photosensitive resin, which solidifies to form 3D structures with smooth, high-resolution features.
The team used a VPP method called two-photon printing, which deploys a highly focused laser to solidify a resin in a precise area building a 3D structure one tiny brick at a time. This enabled them to produce extremely sharp emitter tips and narrow, uniform capillaries to carry propellant.
To produce the manifold block, the team used digital light processing, which uses a chip-sized projector to shine light into the resin, solidfying one layer at a time.
The engine comprises 32 electrospray emitters that operate together to produce a stable propellant flow. The group say the 3D-printed device can generate as much or more thrust than existing droplet-emitting electrospray engines.
The device also requires a complex hydraulic system to store and regulate the flow of liquid, efficiently shuttling propellant through microfluidic channels.
The emitter array is composed of eight emitter modules. Each emitter module contains an array of four individual emitters that must work in unison, forming a larger system of interconnected modules.