3D printing tail rotor gearbox housing on drones
Italian manufacturer CRP Technology has partnered with the firm FLYING-CAM to create a 3D-printed protective system for the tail rotor actuators and GPS antenna on the latter’s 75kg unmanned single-rotor helicopter named Discovery.
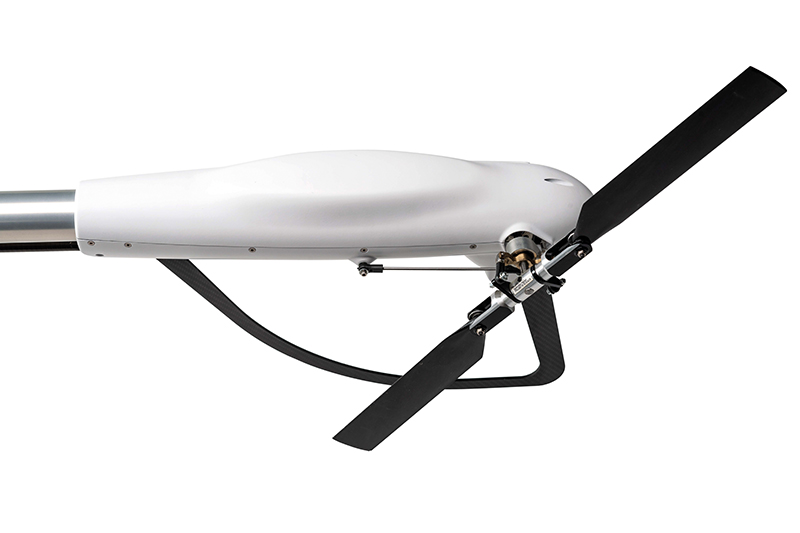
Engineer Franco Cevolini, CTO at CRP Technology, explains that the brief was to create lightweight, yet rigid, physical and aerodynamic protection.
The manufacturer chose selective laser sintering – a powder bed fusion (PBF) process – to complete the protective casing using a carbon-fibre-filled, polyamide-based, 3D-printed composite known as Windform XT 2.0 technology.
Emmanuel Previnaire, founder and CEO of FLYING-CAM, says, 'With the potential that drones offer the civil market, and the interest in Beyond Visual Line Of Sight (BVLOS) flights, we felt it was the right time to develop a drone that could not only capture beautiful imagery…but that could carry a variety of payloads to collect the necessary data for other industrial applications'. Discovery is kitted with sensors for a variety of applications suitable for high precision remote sensing.
The complexity, quality and shape of the brief for CRP Technnology was therefore demanding.
The part has been conceived to withstand specific issues, Previnaire shares. 'The component was planned to be clamped on the tail boom, and support also the carbon plate used as a tail rotor ground protection. For this reason, a good stress resistance was needed. The clamping strength depends on the construction material’s capabilities. We have chosen Windform XT 2.0 as it allows us to achieve it with a good weight-resistance ratio.'
The mechanical and thermal properties of Windform materials are strictly connected to the characteristics of the 3D printing manufacturing process.
CRP Technology undertook an internal ‘design review’ to ensure it could meet the exacting standards.
'We carried out dimensional inspections and destructive testing methods – in this case, tensile tests – to validate the 3D-printed part from a mechanical point of view,' Cevolini explains. 'These tensile tests were conducted on specimens manufactured along with the customer’s part.'
Cevolini explains that the design review is part of the legacy that the manufacturer has built on through its experience working with Formula 1, to maximise the potential of 3D printing.
Previnaire underlines, 'The most innovative aspect…is the free shape design, important for aerodynamic purpose, as well as the ability to create complex wiring channels inside with strong attachment point, in one unique piece. [The] PBF process and Windform materials allow the creation of hollow parts with a lot of functional details, such as fixation nuts integration [and] cable attachment points.'
Cevolini adds that the composite material offers other important benefits – it has passed outgassing tests for the major international space agencies so is ready for flight and space, and it has also achieved an HB rating in relation to the flammability UL 94 test.
The solution, he says, can provide reduced mass and weight; iterations can be produced more quickly; it is possible to obtain a very smooth surface finish; and the geometry can be optimised to improve the integration of internal parts. Going forward, 'One of the challenges we face is manufacturing 3D-printed structures that are becoming smaller, yet are capable of fitting in more systems, such as electronics, a camera and a radio.'