3D printing a natural-material flooring panel
A 3D-printed, single-piece of natural-material floor panel is strong enough to replace construction materials like steel, say designers in the USA.
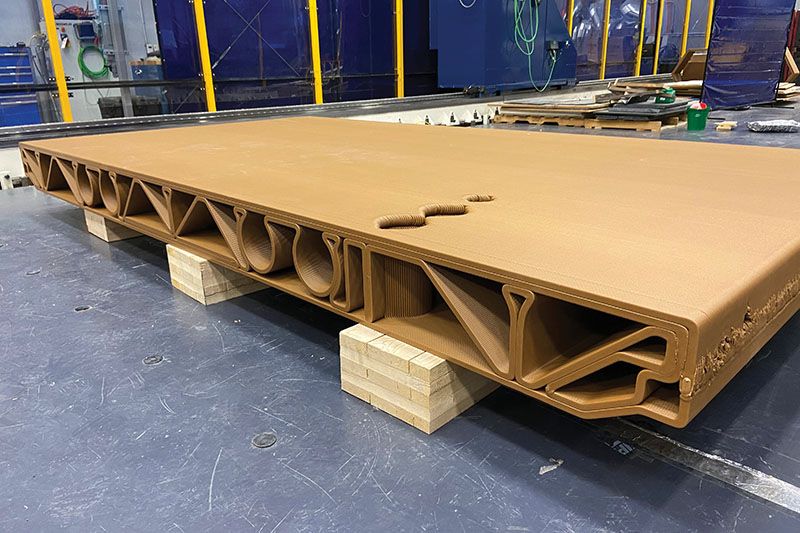
The SM2ART Nfloor single-cassette panel from Oak Ridge National Laboratory (ORNL) and the University of Maine, is to replace multi-component steel and concrete surface assemblies in flats.
The 3.6m-long, 1.2m-wide floor panel is made from wood flour from lumber waste and polylactic acid (PLA). The wood fibre/flour is a uniformly milled sawdust, which is normally burnt as a low-quality fuel or landfilled. The wood fibre content comprises 20-40% of the floor panel by weight.
Knowing the inherent properties of the PLA/wood flour material, such as its tensile, flexural and compressive strengths, the team designed the truss and parameters that control the wall thickness – like bead size and number of beads – to meet the mechanical requirements of the floor piece.
The researchers say these strong, stiff, biological sections could increase the number of sustainable structures in a modular multi-storey facility. And even though the floor cassette is heavier than the incumbent steel frame, the design distributes the load, with some of it being transferred to the steel frame of the whole module.
'By utilising bio-based, large-scale 3D printing, we replaced an assembly made from 31 parts and three materials with a single-material floor panel that is ecologically friendly, and with the same strength as traditional steel floor fabrication,' says ORNL Senior R&D Staff member, Dr Halil Tekinalp.
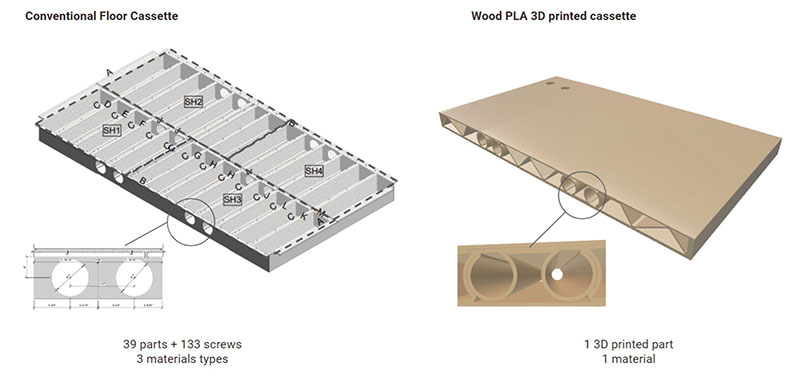
Four printed pieces can be used to assemble an entire floor in a studio apartment, reports the team, while the internal architecture of each floor cassette can vary depending on the piece.
'Our industry partner on this project (Assembly OSM) actually mentioned they like the sturdier feel of the printed floor piece because it feels more like walking on a ground floor, so this could be a benefit,' says Tekinalp and fellow ORNL R&D team member, Dr Katie Copenhaver.
A large-scale 3D printer deposits the PLA/wood flour mixture in a precise geometric shape, producing the cassette a layer at a time in around 30 hours. The teams says this saves ~33% labour compared to constructing a similar steel floor manually.
They are trying to further reduce the print time. A significant cost of a traditional steel frame is reportedly near completion when workers cut channels for electrics, plumbing and ductwork. Copenhaver comments that their method saves time and money by printing the floor with those cut-outs made, and only a sound-proofing skin and floor covering need to go over the top.
The floor can reportedly be shredded at the end of its life to make new PLA pellets for re-extrusion. 'We found that the recycled parts had almost identical mechanical performance to the original parts', say Copenhaver and Tekinalp.
The team has data on specific properties such as creep and stress relaxation under cyclic and static loads. They say that the flooring covering means it is unlikely to abrade or be exposed to potentially damaging materials such as solvents in household cleaners.
As the project is in initial stages of development, additional research will involve flame retardants, the possibility of adding natural-material insulation and improving the production technique.