3D printer automatically configures to unknown materials
A 3D printer that automatically figures out how to print unknown materials could additively manufacture components from renewable or recyclable materials that are hard to characterise.
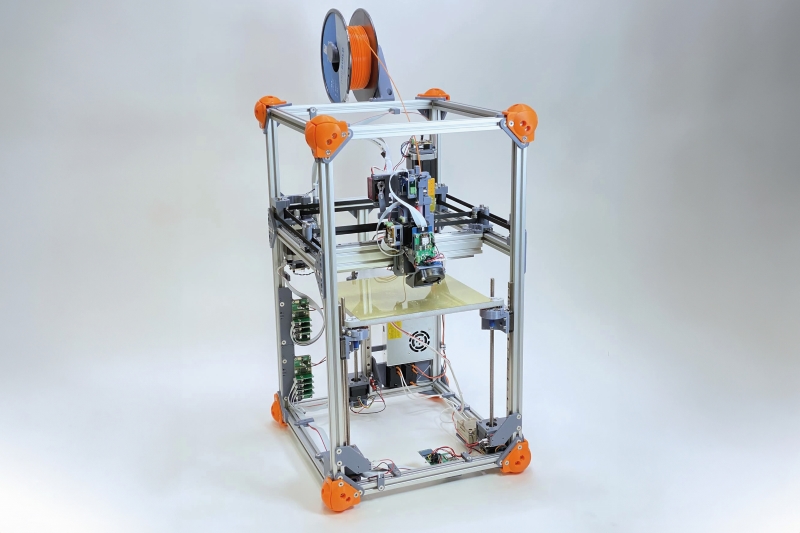
The machine is a joint effort from the Massachusetts Institute of Technology (MIT), USA, the US National Institute of Standards and Technology, and the National Center for Scientific Research in Greece.
Fused filament fabrication (FFF) – often used in rapid prototyping – extrudes molten polymers through a heated nozzle layer-by-layer. The software, or slicer, instructs the machine, but usually is configured for a particular material.
New materials can therefore be difficult to manufacture in this way, says the group, because settings need manually adjusting each time and the properties can vary widely due to the composition.
They estimate around 100 software parameters control a printer’s extrusion. Commonly used materials have parameter sets perfected by trial-and-error.
Nearly half of all print settings are related to two key parameters – flow rate and temperature – notes the group.
Starting with an MIT printer that captures data in operation, the group has integrated three instruments that measure a material’s forces and flow. A load cell measures the pressures on the printing filament, while a feed rate sensor measures the filament thickness and the actual flow rate.
The feed rate and width sensor are a roller wheel touching the filament, explains first author Jake Read. '…imagine a passive version of a normal FFF extruder’s drive gears. We measure that wheel’s rotation as a proxy for linear feed rate, and we measure its position as a proxy for the filament’s width.'
The load cell acts as a ‘strain gauge’, as it measures small deflections in a carefully designed structural element using variable resistance. This is positioned in the hot end’s structural loop, so any load travelling through the filament returns to the machine via the load cell.
A 20-minute test on a new material generates temperature and pressure readings at different flow rates. It involves setting the print nozzle to the hottest temperature, flowing the material at a fixed rate, before turning the heater off.
The collected data is fed into a mathematical function that generates parameters for the material and machine configuration, using relative temperature and pressure inputs. The user can then enter those parameters into off-the-shelf 3D-printing software and generate instructions for the printer.
'This is why we are essentially advocating adding these kinds of (very cheap) sensors to more printers,' asserts Read. 'Machines are all inherently different, so it is difficult to make data that is transferable across machines without doing very careful calibrations. By adding sensors to each machine, they can also be used as real-time feedback-control devices (which we are actively working on).'
The automatically generated parameters can replace about half the parameters that are typically manual, claims the team. In a series of test prints, including several renewable materials, the researchers report their method can consistently produce viable parameters to print a complex object.
They tried it on filaments of acrylonitrile butadiene styrene, polylactic acid (PLA), polyethylene terephthalate glycol and recycled materials, at 2-25mm3/s flow rates.
The team says the printer works on 'anything that can be extruded'. Read adds, 'Very soft or brittle materials may still be difficult since the test cannot yet recover from failures where a filament breaks in the extruder.
'We basically think that many filaments are avoided by users because there is no guarantee that they will work well. So, this ameliorates some of that problem because it lets the machine figure out how to operate automatically. We also suspect that with future work we will show that this kind of approach helps the printer operate ‘more optimally’ on even well-understood filaments like PLA.'