3D-printed superalloy could cut power plant carbon emissions
A new 3D-printed, high-performance, metal alloy is reportedly stronger and lighter than materials in current gas turbine machinery.
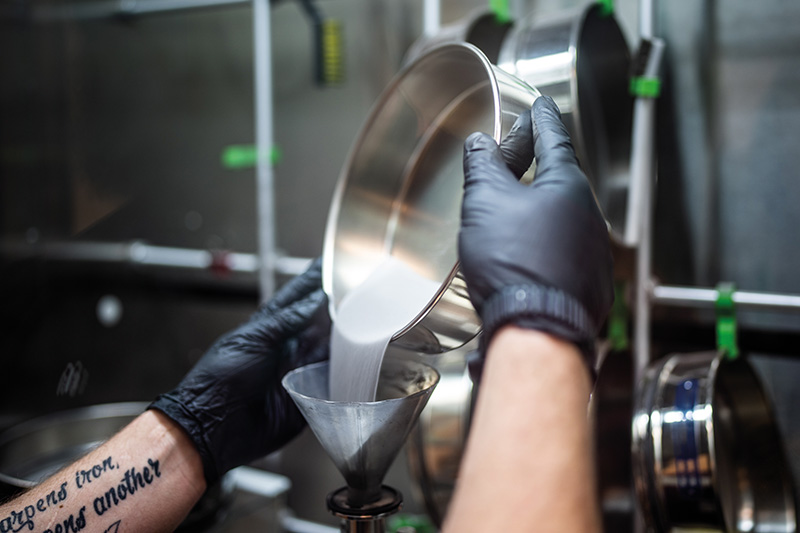
The alloy could generate more electricity for power plants with less carbon emissions, benefit aerospace and the automotive industry. It is said to have a previously unobtainable combination of high-strength, low-weight and high-temperature resilience.
The group, led by Sandia National Laboratories, USA, says the superalloy is stronger at 800°C than other high-performance alloys with a hardness of 8GPa, and stronger at room temperature with a hardness of 10-15GPa. Gas turbines that operate at higher temperatures are more efficient. They report the alloy’s low density to be 5.7g/cm³, with an equivalent uniaxial tensile strength of 3-4.5GPa at room temperature and 2.5GPa at 800°C, and a specific strength of 411-765MPa-cm³/g.
First author Andrew Kustas notes that the maximum hardness/strength is more than three times greater than Inconel 718, a nickel-based superalloy used in aerospace.
Unlike many alloys, no single metal constitutes more than half the material – with 42% aluminium, 25% titanium, 13% niobium, 8% of zirconium and molybdenum each, and 4% tantalum. Kustas says that an alloy of the same metals but different ratios, published by Miracle et al. in a 2017 Acta Materialia article, was a starting point.
Materials modelling is based on electronic structure theory – led by Ames Laboratory, USA – which gave a thermodynamic understanding at an atomic level. The modelling shows that the alloy’s high strength is from the complex energy-composition space in a certain composition range.
Then a laser engineered net shaping (LENS) printer – a type of directed energy deposited printer patented and commercialised by Sandia – melted and cyromilled powdered metals.
'You can think of the approach as a layerwise laser welding method, where you are welding together tiny metal particles. A primary advantage of this approach is the ability to use small powder batches as feedstock, on the order of only a few hundred grammes, which is ideal for exploring expensive and experimental metals/alloys,' Kustas explains. The new paper posits using 20%-70% aluminium and 55-70% of titanium, with refractory elements, for a high-strength alloy.
The team is now exploring how advanced modelling can discover more high-performance superalloys using additive manufacturing. Kustas says, 'One possibility is to explore opportunities to replace conventional alloys that are currently used as turbine blades, bearings and seals within turbomachinery devices. However, a key challenge is scaling up this current alloy with viable manufacturing routes, like additive manufacturing, to achieve desired component size and shape.'
Ames and Sandia are partnering with industry to explore uses for automotive manufacturers – they believe aerospace could also benefit. Kustas notes that it could be difficult to produce a new superalloy in large volumes without microscopic cracks, a general challenge for additive manufacturing, and the metals used are expensive. 'We are looking to expand our search in this alloy system to other candidate alloys that may have higher resistance to cracking, but still retain similar strength and temperature resiliency. The prospect of finding even better alloys is perhaps the most exciting.
'Though an important missing link regarding the material properties is also the creep behaviour, that is, the mechanical properties of the alloy during long (continuous) exposures to high temperatures. The alloys in turbomachinery must survive many thousands of hours at high temperatures without failing. Our alloy must demonstrate appropriate creep behaviour to be a viable replacement to conventional superalloys – this has yet to be demonstrated for this material.'
He mentions that thermal stress might be reduced by different manufacturing methods as well as exploring alternative feedstocks.