3D-printed ceramic monoliths neutralise PFAS chemicals
A way to remove harmful per- and polyfluoroalkyl substances (PFAS) ‘forever chemicals’ from water has been designed using 3D printing.
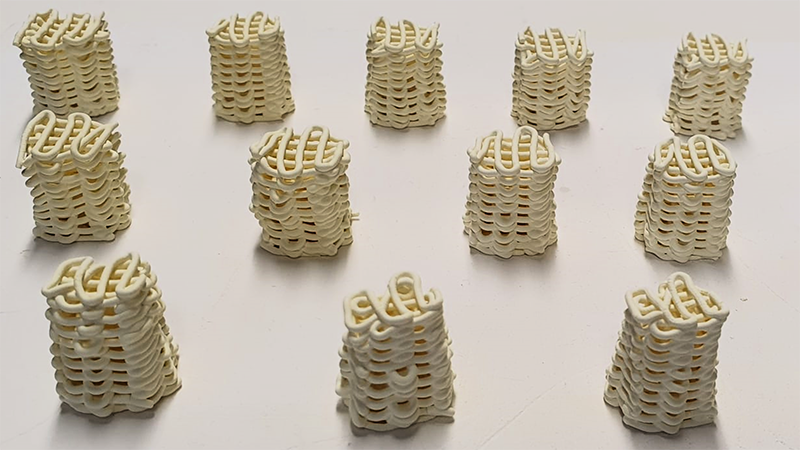
Engineers at the University of Bath, UK, say their ceramic-infused lattices remove at least 75% of the most common of these chemicals – perfluorooctanoic acid (PFOA) – under test conditions.
The ability to remove them from water in less than three hours with only small amounts of energy could help water utility companies eliminate these hazardous chemicals from drinking water, say its developers.
The paper on 3D-printed indium oxide monoliths for PFAS removal, published in the Chemical Engineering Journal, outlines how 3D printing is critical to the process because it creates self-supported, high-surface monoliths that can be fabricated quickly using a cost-effective extrusion-based approach.
The 4cm lattices made with ink infused with a ceramic indium oxide (In2O3) powder, are dispersed in a Pluronic F-127 solution (15% v/v) used as a binder. The ink solution is then mixed constantly for around 15 minutes at room temperature (25°C).
Once printed, the monoliths are dried at room temperature for 12 hours and then sintered at 500°C for 10 hours in a tubular furnace, with a heating rate of 5°C/minute and a cooling rate of 3°C/minute, notes the paper.
The geometry is designed to maximise the surface area, which 'improves the exposure of active sites and the flow of the pollutant solution [PFOA] permeating through it'.
The team has dropped them into water and studied their effectiveness in removing PFOA using a recirculating flow set-up.
The paper explains how a single monolith, measuring 21mm or 44mm in length and weighing 5.5g or 10g, is put inside a quartz tube. A recirculating water-cooling system is connected to the 500ml set-up, with a constant temperature of 10°C.
The initial concentration of PFOA is set to 10µM (4.1mgL-1). The solution pH is measured as 6.6 and is not adjusted further, adds the paper. The PFOA solution then flows through the quartz tube containing the monolith using a pulseless gear pump that operates from 100-700mLmin-1 for 180 minutes.
After that, the team removed less than 5% of the total PFOA solution with a disposable syringe and it is filtered into a polypropylene vial to remove any residual particles.
According to the paper, an additional pyrolysis process at 500°C regenerates the In2O3 monoliths, enabling them to be reused for three adsorption cycles, while also improving PFOA removal to 75% in three hours.
The researchers intend to find out why the monoliths appear to become more effective under repeated use after high-temperature thermal regeneration treatment.