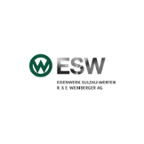
Eisenwerk Sulzau-Werfen (ESW)
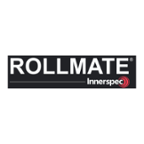
Innerspec Technologies Europe S.L.
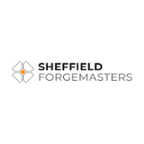
Sheffield Forgemasters
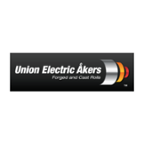
Union Electric Akers
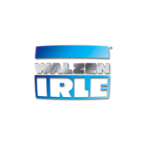
Walzen Irle GmbH
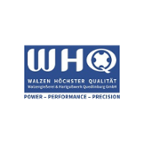
Walzengiesserei Quedlinburg - Deutsche Rolls
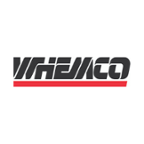
Whemco Steel Castings
9 June–21 July 2021
The Eisenwerk Sulzau-Werfen was founded in 1770 and has been in family ownership since 1899. The company has received several awards and nowadays annually produces about 2000 rolls with a final weight of up to 42 tonnes per roll. ESW is thus one of the world market leaders in this segment.
Rolls manufactured in Tenneck near Salzburg are involved in the making of sheet metal for cars, beverage cans and products for the building industry, and in the creation of many products used daily. The export ratio amounts to 97.8 per cent.
ESW focuses in particular on making investments in research and development so that products and procedures can be continually developed further and improved. Every year the company spends over two per cent of its turnover on this sphere.
The Eisenwerk Sulzau-Werfen is recognized as a company that pays due regard to environmental compatibility, emission neutrality, as well as the efficient use of energy and raw materials. Over 300 employees work for the family-owned company which is one of the most important employers in the Pongau district of Salzburg province.
Innerspec provides Non-Destructive Testing (NDT) solutions requiring high-power ultrasonic instrumentation, non-contact techniques, or customized integrations. The products developed by Innerspec include both integrated and portable systems that utilize non-contact EMAT (Electro Magnetic Acoustic Transducers), Dry-Coupled Piezoelectric and Eddy-Current transducers.
Since 1989, when Innerspec engineers designed a complete system for inspection of the booster rockets of the space shuttle, we can claim more first-of-a-kind NDT developments than any company in our industry. Innerspec pioneered commercial applications of Electro Magnetic Acoustic Transducers (EMAT) in the mid-90s becoming the world leader in this technology with hundreds of systems installed worldwide. More recently, we have added other techniques to our portfolio to serve our customers with all their advanced non-destructive testing needs.
Innerspec is headquartered in Forest, Virginia (USA) and Madrid (Spain) with an unmatched team of researchers, development engineers, customer support specialists and technicians dedicated to design and support our products and services. Our additional offices in Latin America, UK, and China along with representatives around the globe provide commercial and technical support with factory trained personnel.
Specifically in the world of Roll inspection, Innerspec was breaking ground with its first commercial system in 1996 and continuous development that include multiple roll inspection specific patents. For example, Innerspec patented the usage of creeping waves in UT roll surface inspection.
:
https://www.innerspec.com/integrated/mill-roll-inspection
:
innerspec-technologies
Sheffield Forgemasters provides Casting and Forging solutions for the world’s most complex engineering challenges and is a key supplier to the UK submarine programme.
The company specialises in the design and manufacture of high integrity forgings and castings offering a ‘one-stop shop’ for steel production from a single site in the UK and seeks out contracts that carry a premium value through their manufacturing complexity and safety critical requirements.
It operates a dedicated rolls making facility, serving global markets and offers design, project management, steel melting, forging, casting, machining, testing and delivery services.
Sheffield Forgemasters started producing forged steel rolls in the 1860’s. We are technology leaders in forged work roll, back up roll and plate mill back up roll production. In partnership with many OEMs we have pioneered the development of many modern roll making processes
Our steel processing facility was custom built for forged steel roll production and is among the most advanced, dedicated, forged roll plants in the world, delivering lowest cost of ownership to steel producers.
We provide a full support service to our customers to achieve the best possible performance from our rolls.
Sheffield Forgemasters has a dedicated research, development and technology arm, (RD&T) which is ran by a team of PhD engineers and designers who have refined the art of computer simulation to large scale engineering challenges and are adept at finding the best route to manufacture and the highest levels of manufacturing integrity.
Some of the largest bespoke engineered steel products in the world are produced at the Brightside Lane facility with capacity for castings of up to 350 tonnes, forgings of up to 200 tonnes finished weight and multiple finished sizes available from 2T up to 170T.
:
https://www.sheffieldforgemasters.com/
:
sheffield-forgemasters
:
@@forgemastersHQ
The name "WALZEN IRLE" stands for 200 years of experience, technological competence and continuous research and development in the production of rolls, pistons and wear-resistant castings. The traditional and consequently close cooperation with machine builders and operators of constructions has lead to permanent and successful improvements of the WALZEN IRLE technologies and has made them an innovative technology leader. Our motivation is to find better solutions, to develop innovative products and to satisfy customer needs. Continuous research and development is our key to success!
WALZEN IRLE Rolls for the steel industry are manufactured according to the most modern metallurgical and technical machining standards under the leadership of experienced engineers.
The certified quality management system according to DIN ISO 9001:2015 in connection with modernly equipped laboratories guarantees the precise testing of all production steps and has contributed to the worldwide good reputation for rolls.
The continuous improvement of our product materials results in ever increasing performance enhancements of our rolls. Due to the upgrading of our centrifugal casting capacities we are able to fulfill the increasing demands of the steel industry in the future with regards to numbers and dimensions. Technical sales specialists are always at hand to develop professional solutions for the various challenges our customers come across in their rolling mills.
WHQ, also "Deutsche Rolls“ is a premium roll maker with a truely global customer base, established 1865 in Quedlinburg, middle of Europe/Germany.
Main focus lies on customers from steel- (long/profile, not flat), tube- and brick industries.
Full control of the manufacturing process from A to Z inhouse, safe supply chain and premium quality reduce your total operating costs, providing you with the competitve edge you need.
Get in touch. We speak your language (English, French, Russian, Arabic).
Offered cast iron and half steel grades cover all known alloys.
WHEMCO, Inc., headquartered in Pittsburgh, Pa., USA, is the consolidation of North America’s leading roll manufacturers supplying both cast and forged work rolls and backup rolls. We also provide large castings and forgings to the metals, mining and power generation industries and to other heavy industrial applications globally. Our roll manufacturing capabilities are located at three facilities within the USA:
We are known as the best in the roll industry when it comes to providing technical support and service to our customers.