Navigating Industry 4.0 in Materials, Minerals & Mining - Additive Assembly
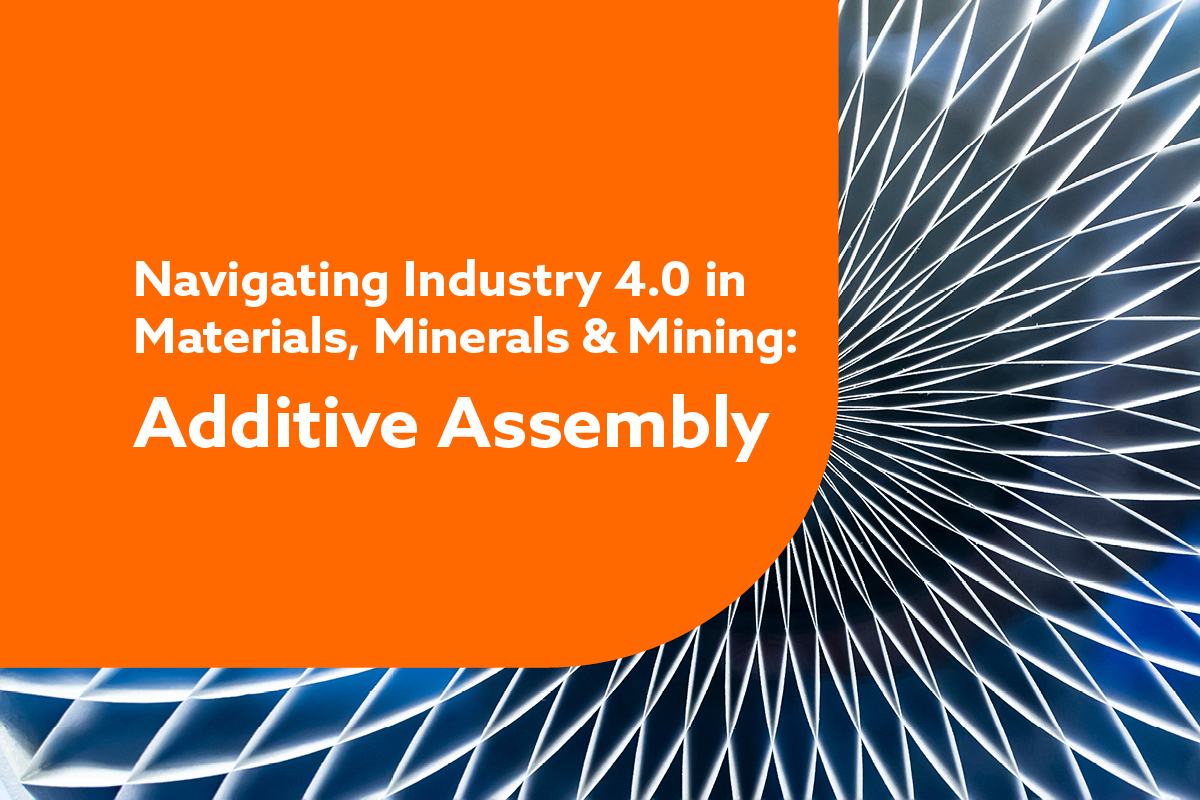
You are invited to join us for the third webinar in our new series Navigating Industry 4.0 in Materials, Minerals & Mining where will we focus on additive assembly
You will hear from:
Samanta Piano, University of Nottingham
Enhancing in-process monitoring of additive manufacturing through virtual fringe-projection simulations
-
Reliable and repeatable laser powder bed fusion systems require real-time in-process monitoring to deliver right-first-time production capability. While finding defects after the printing process is the standard procedure, to identify correlations among in-process parameters, defects and part performance remain difficult to establish.
-
By finding such correlations, we can design controlled processes capable of detecting functionally detrimental defects, in real time, through in-situ metrology. The first step to achieve real-time monitoring is to design and characterise a measuring system able to accurately measure the surface of the printed part and identify anomalies in the building part.
-
For this purpose, a multi-view optical fringe projection technology has been released using a virtual environment and its performance has compared to the real system.
Ian Laidler, Chief Technology Officer, Wayland
Wayland’s NeuBeam Additive Manufacturing Technology
-
Introduction to Wayland Additive and the next generation of Electron Beam Metal AM machines.
Iain Todd, Professor of Metallurgy
Digitalisation of Additive Manufacture - using less and doing more with metals
- Additive Manufacture is often discussed as a clean manufacturing technology but there are several barriers to this being truly the case.
- Here I will discuss work on process control to ensure right first time manufacture and also discuss emerging business concepts such as materials as a service and digitally distribute inventory as ones enabled by this exciting technology.