Defence Safety & Security Group Technical Networking: Additive Manufacturing in Defence
If you would like to take part in this event as a speaker, reach out to James Lee.
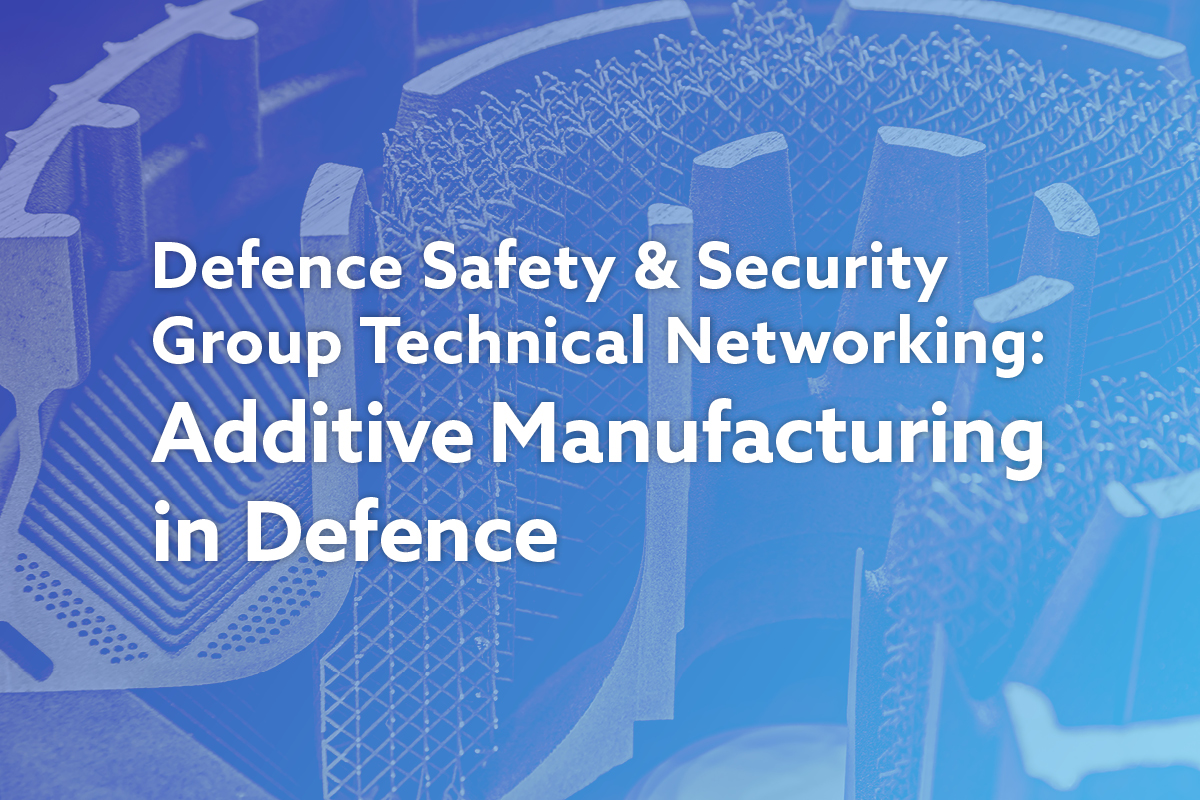
Join us for the IOM3 Defence Safety & Security Technical Networking Event: Additive Manufacturing in Defence.
This half-day event is designed for businesses, academia, and industry leaders to highlight their innovations and expertise. It provides a prime opportunity to network, present cutting-edge solutions, including advancements in additive manufacturing, engage in insightful discussions, and explore collaborative ventures that could shape the future of global security.
Don’t miss out on this unique platform to elevate your business or academic research and connect with influential figures in the defence and security sector. Register now to secure your spot!
Agenda |
20-minute presentation + 5-minute Q&A
13:00 | Registration |
13:25 |
Welcome Address Cem Selcuk, TWI |
13:30 |
Industrial techniques and equipment for sintered and additive manufactured parts quality control by X-ray imaging and Laser profilers 3D scan Mihai Iovea - AP2K, Romania |
14:00 |
Benchmarking of Additive Manufacturing Machines: A Standards-Based Approach Anna Terry, Additive Manufacturing Development, AWE |
14:30 |
Derisking Additive Manufacturing for UK Industry Tay Chauhan - MTC |
15:00 |
Approach to certification of AM in defence Charlotte Meeks - QinetiQ |
15:30 |
The Additive Manufacture of Refractory Metals David Rowe - Cedar Metals |
16:00 | Pitching Session |
16:00 |
Erikus Van Dyk - Zeeko |
16:10 |
Residual Life and Durability Anaylsis of Aerospace Components Ramesh Chandwani - Zentech |
16:20 |
Digitisation, Data and Automation with Radiography Systems Peter Fairley - Fairley Gunn Group |
16:30 |
Electroforming technology for defence applications Andy Bushby - Ultima Forma; Queen Mary University of London |
16:40 | Networking Drinks |
17:30 | Close of event |
We will hear from |
|
Abstracts |
Mihai Iovea - Industrial techniques and equipment for sintered and additive manufactured parts quality control by X-ray imaging and Laser profilers 3D scan
In the first part, we introduce our company, Accent Pro 200 s.r.l. (www.accent.ro), and its activities in the Research and Development of X/Gamma Ray Imaging Techniques for Security and Non-Destructive Testing industrial applications. Then, we present our new quality control technique using X-ray imaging and Laser Profilers 3D scans, showcasing results obtained from two developed equipment for military and industrial sintered parts quality control. In the final part, we introduce two new NDT techniques: a laser-based additive manufacturing process with real-time control by X-ray imaging and Gamma imaging technique driven by Femtosecond Laser.
Anna Terry - Benchmarking of Additive Manufacturing Machines: A Standards-Based Approach
To provide quality parts to our customers, a consistent approach to qualification is required. The approach is based upon guidance from auditing authorities, international standards organisations, and in-house expertise. This presentation explains the methodology AWE has adopted to benchmark machines including material testing, the challenges encountered and an overview of ongoing activities. Results to date will be shared and discussed.
Charlotte Meeks - Approach to certification of AM in defence
The UK is a world leader in Additive Manufacturing (AM) capability and has been at the forefront of developing this technology. To test the feasibility of pursuing ‘AM as a Service’ the MoD have invested in a number of AM technology development programmes and supported working groups on key topic areas bringing together industry providers. This presentation will summarise the work of the certification working group which aimed to convene key stakeholders to ascertain a future vision that supports the conditions to expand the uptake of this technology across the broadest range of defence inventory possible. The group investigated whether additive manufactured parts entering the defence inventory required changes to current policy, guidance or standards and identified gaps that need to be addressed to enable the uptake of AM technology. A living-guidance document has been produced aimed at bridging between the DO/DA and the regulator’s requirements linking with the abundant international AM standards landscape and providing guidance on best practice regarding an expected level of certification effort that is proportionate to part criticality.
David Rowe - The Additive Manufacture of Refractory Metals
Refractory metals are well known for their high temperature and corrosion resisting properties. However, they are also very reactive metals and oxidise above about 250°C in air. Thus, protective inert atmosphere or vacuum is required for processing. As all refractory metals are available in powder form, they can be used in additive manufacturing processes, a process useful for fabricating difficult to machine components. Tantalum, niobium and zirconium are mainly used in the chemical process industry and are little used in defence. These are readily machinable and weldable via conventional techniques, but tungsten and molybdenum are difficult to machine, especially into complex shapes so are ideally suitable for additive manufacture.
For additive manufacturing, a free-flowing powder is required, and this is usually accomplished by spray drying a slurry of the powder mixed with a suitable binder to produce a spherical powder which is sintered to give sufficient strength for processing. Conventional processing involves the use of conventional powder with poly-vinyl alcohol as binder. However, a process developed by the author in 1986 but never exploited due to changing circumstances, simplified spherical powder production without the use of PVA. High temperatures are required to sinter the additive manufactured components, and the presentation concentrates on an AM produced complex molybdenum component illustrated with an example produced at Oak Ridge Laboratories. |